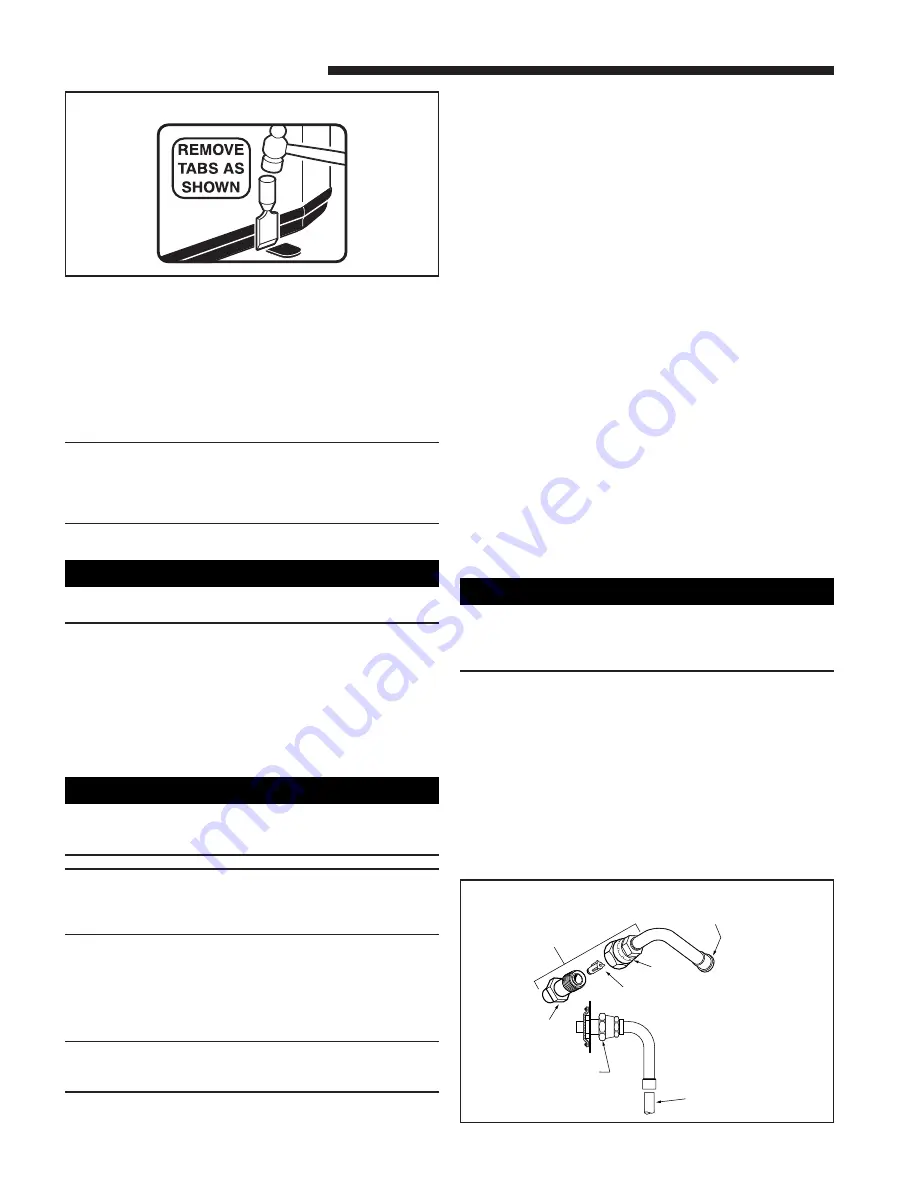
© 2010 Trane
18-AC51D5-5
Installer’s Guide
C. ACCUTRON™ FLOW CONTROL VALVE
If the indoor unit System Refrigerant Flow control is an
Accutron™ orifice and check valve assembly, an orifice size
change may be necessary. See Figure 3.
The outdoor model determines the required orifice size. Check
the listed orifice size on nameplate of the selected outdoor
model. If the indoor unit is factory shipped with a different
orifice size, the orifice must be changed to obtain system
rated performance.
IMPORTANT:
The outdoor unit is shipped with the proper size orifice and a
stick-on orifice size label in an envelope attached to the outdoor
unit. Outdoor unit nameplate will have correct orifice size
specified as BAYFCCV---A for rated performance.
D. INSTALLING REFRIGERANT LINES
▲
CAUTION
!
If using existing refrigerant lines make certain that all joints
are brazed, not soldered.
Condensing units have provisions for braze connections.
Pressure taps are provided on the service valves of outdoor
unit for compressor suction and liquid pressures.
The indoor end of the recommended refrigerant line sets may
be straight or with a 90 degree bend, depending upon situa-
tion requirements. This should be thoroughly checked out
before ordering refrigerant line sets.
The gas line must always be insulated.
▲
CAUTION
!
In scroll compressor applications, dome temperatures may
be hot. Do not touch top of compressor, may cause minor
to severe burning.
IMPORTANT:
The unit has a NITROGEN holding charge which will need to
be evacuated before charging per local system application
requirement.
Refrigerant charge adjustment is necessary.
Use the
Charging Charts in the outdoor unit Service Facts.
1. Determine the most practical way to run the lines.
2. Consider types of bends to be made and space
limitations.
NOTE:
Large diameter tubing will be very difficult to rebend once it
has been shaped.
3. Determine the best starting point for routing the refriger-
ant tubing — INSIDE OR OUTSIDE THE STRUCTURE.
4. Provide a pull-thru hole of sufficient size to allow both
liquid and gas lines.
5. Be sure the tubing is of sufficient length.
6. Uncoil the tubing — do not kink or dent.
7. Route the tubing making all required bends and properly
secure the tubing before making connections.
8. To prevent a noise within the building structure due to
vibration transmission from the refrigerant lines, the
following precautions should be taken:
a. When the refrigerant lines have to be fastened to floor
joists or other framing in a structure, use isolation
type hangers.
b. Isolation hangers should also be used when refriger-
ant lines are run in stud spaces or enclosed ceilings.
c. Where the refrigerant lines run through a wall or sill,
they should be insulated and isolated.
d. Isolate the lines from all ductwork.
E. SERVICE VALVE OPERATION
BRASS LIQUID AND GAS LINE SERVICE VALVES
The Brass Liquid and Gas Line Service Valves are factory
shipped in the seated position to hold factory charge. The
pressure tap service port (when depressed) opens only to the
field brazing side of the valve when the valve is in the seated
position. The liquid line valve is
not
a back seating valve
(see
WARNING
below).
▲
WARNING
!
Extreme caution should be exercised when opening the
Liquid Line Service Valve. Turn valve stem counterclock-
wise only until the stem contacts the rolled edge. (See
Figure 4) No torque is required.
BRASS GAS LINE BALL SERVICE VALVE
The Brass Gas Line Ball Service Valve is shipped in the
closed position to hold the factory refrigerant charge. The
pressure tap service port (when depressed) opens only to the
field brazing side when the valve is in the closed position. The
Gas Line Ball Service Valve is full open with a 1/4 turn. See
Figure 5.
BRAZING REFRIGERANT LINES
1. Remove lower access cover to access service valves.
2. Before brazing, remove plugs from external copper stub
tubes. Clean internal and external surfaces of stub
tubes prior to brazing.
BASEPAN TAB REMOVAL
2
SEALING CAP
ADAPTER
FLOW CONTROL
CHECK VALVE
(F.C.C.V.) ORIFICE
FIELD SUPPLIED
LIQUID LINE
AS SHIPPED
BODY
ACCUTRON
TM
COMPONENTS
BRAZE TYPE INDOOR END
3