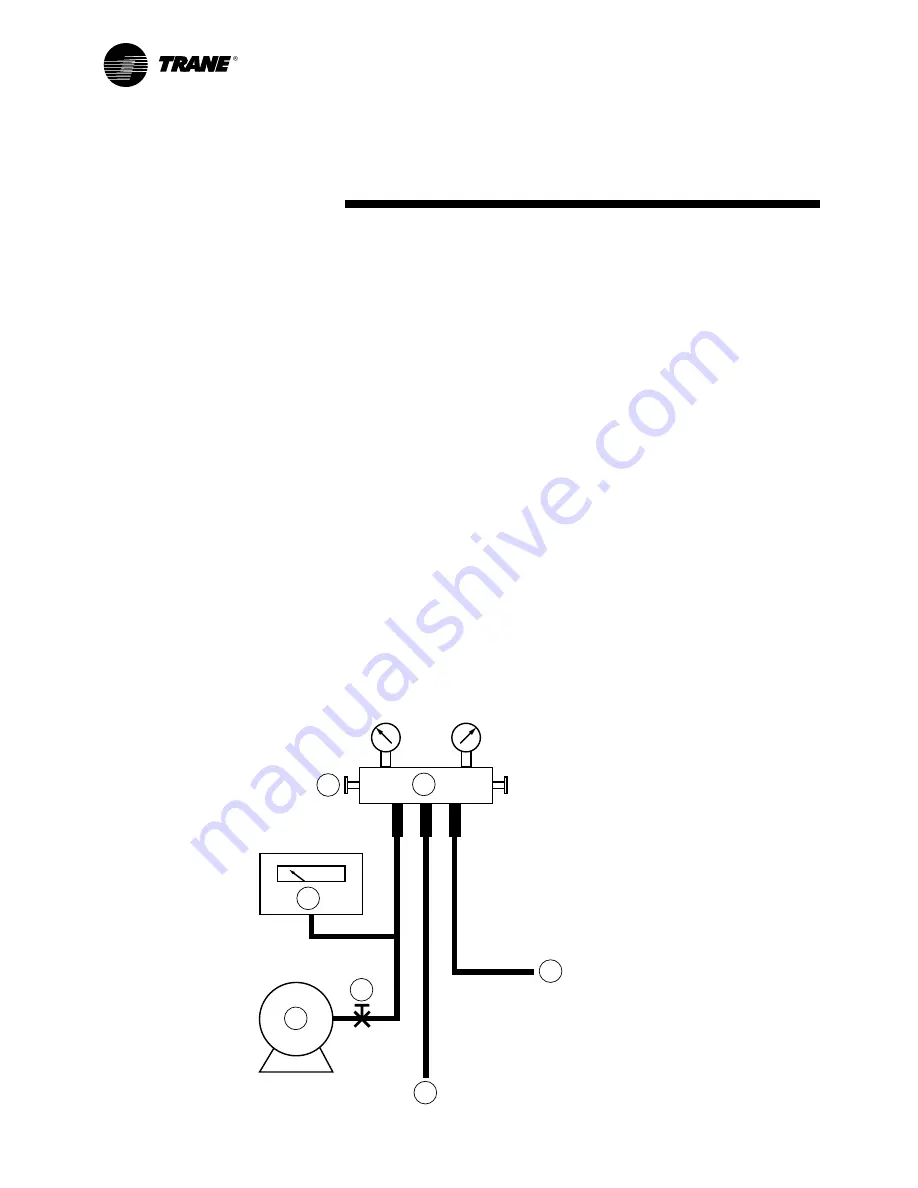
20
Vacuum pumping
For this operation, use a vane pump
making it possible to obtain a partial
vacuum or 100 microns or less.
When pumping out to create a
vacuum, it is important to connect
the pump to the high and low
pressure sides of the system. Follow
the pump manufacturer's
recommendations. The pipes used to
connect the pump to the system
must be made of copper, with the
largest diameter possible. A large
pipe diameter reduces flow
resistance and shortens the duration
of the vacuum pumping.
Do not use rubber or synthetic pipes
which retain humidity, increase the
duration of the vacuum pumping
and cause pressure rises during the
vacuum tests. An electronic vacuum
measurement manometer must be
installed upstream of the vacuum
pump stop valve.
1. Close valve B and open valve A.
After a few minutes, the
manometer reading indicated the
lowest vacuum level that can be
obtained by the pump.
2. Open valve B and operate the
vacuum pump until 1500 Hg
microns (0.67 mbar) or less is
obtained. Close valve A when you
read the manometer.
3. Once the value of 500 microns or
less has been reached and valve A
has been closed, the pressure will
rise.
The maximum permissible increase
is 200 microns after 15 minutes. If
this limit is exceeded and the value
remains constant, there is too much
humidity in the system. A continuous
increase in pressure indicates there
is a leak in the system.
Installation
1
2
4
3
6
7
5
Figure 14 - Vacuum pump connection
1 Header
2 Valve B
3 Vacuum pump
4 Vacuum manometer
5 Valve A
6 Low pressure side
7 High pressure side
RLC-SVX03A-E4