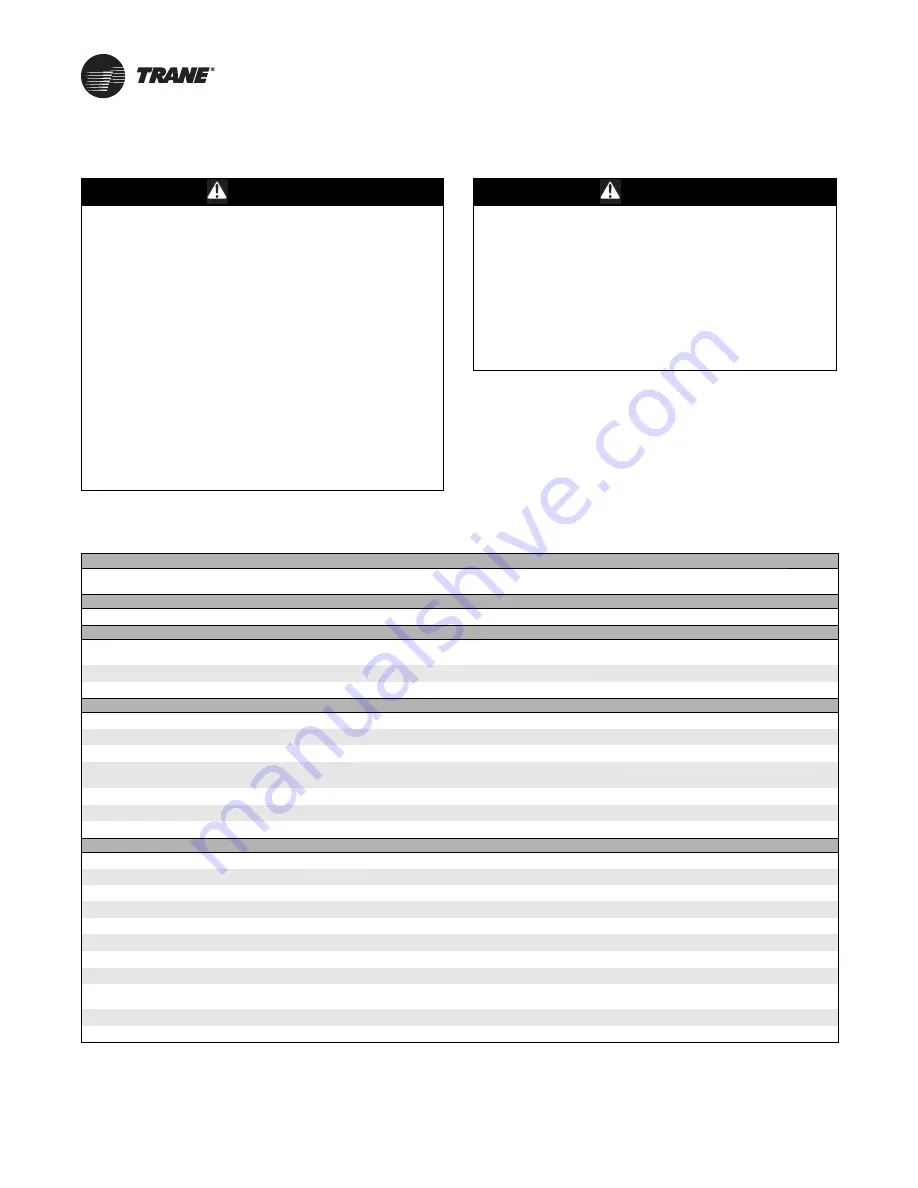
CLCH-SVX009J-EN
65
Routine Maintenance
WARNING
Hazardous Service Procedures!
Failure to follow all of the recommended safety
warnings provided, could result in death or serious
injury. The maintenance and troubleshooting
procedures recommended in this manual could result
in exposure to electrical, mechanical or other potential
safety hazards. Always refer to the safety warnings
provided throughout this manual concerning these
procedures. Unless specified otherwise, disconnect all
electrical power including remote disconnect and
discharge all energy storing devices such as capacitors
before servicing. Follow proper lockout/tagout
procedures to ensure the power can not be
inadvertently energized. When necessary to work with
live electrical components, have a qualified licensed
electrician or other individual who has been trained in
handling live electrical components perform these
tasks.
WARNING
Rotating Components!
Failure to secure rotor or disconnect power before
servicing could result in rotating components cutting
and slashing technician which could result in death or
serious injury. The following procedure involves
working with rotating components. Disconnect all
electric power, including remote disconnects before
servicing. Follow proper lockout/ tagout procedures to
ensure the power can not be inadvertently energized.
Secure rotor to ensure rotor cannot freewheel.
Maintenance Checklist
Table 18. Maintenance checklist
After 48 hours of operation
For belt-drive fans, the belts have acquired their permanent set. Readjust but do not overtighten. See
for more
information.
Every week
Observe unit weekly for any change in running condition and unusual noise.
Every month
Clean or replace air filters if clogged or dirty; coat permanent filters with oil after cleaning; change bag filters when pressure drop is 1 in. wg.
See
for more information.
Belt-drive fans - re-lubricate fan bearings if necessary. See
“Fan Bearing Lubrication,” p. 73
for more information.
Belt-drive fans - check and adjust fan belt tension. See
for more information.
Every three to six months
Belt-drive fans - check fan bearing grease line connections. Lines should be tight to the bearings.
Check motor bracket torque. See
for torque requirements.
Belt-drive fans - check bearing bolt torque and bearing setscrew torque. See
for torque requirements.
Belt-drive fans - align fan and motor sheaves. Tighten sheave set screws to the proper torque. See
“Align Fan and Motor Sheaves,” p. 64
for
more information.
Inspect and clean drain pans. See
for more information.
Tighten electrical connections.
Inspect coils for dirt build-up. See
for more information.
Every year
Inspect the unit casing for corrosion. If damage is found, clean and repaint.
Clean the fan wheels and shaft. See
for more information.
Inspect and clean drain pans.
Check damper linkages, set screws, and blade adjustment. Clean, but do not lubricate, the nylon damper rod bushings.
Clean damper operators.
Inspect electrical components and insulation.
Inspect wiring for damage.
Rotate the fan wheel and check for obstructions. The wheel should not rub. Adjust the center if necessary.
Lubricate motor bearings in accordance with motor manufacturer’s recommendations (see
“Motor Bearing Lubrication,” p. 73
for more
information).
Check condition of gasketing and insulation around unit, door and dampers.
Examine flex connections for cracks or leaks. Repair or replace damaged material.