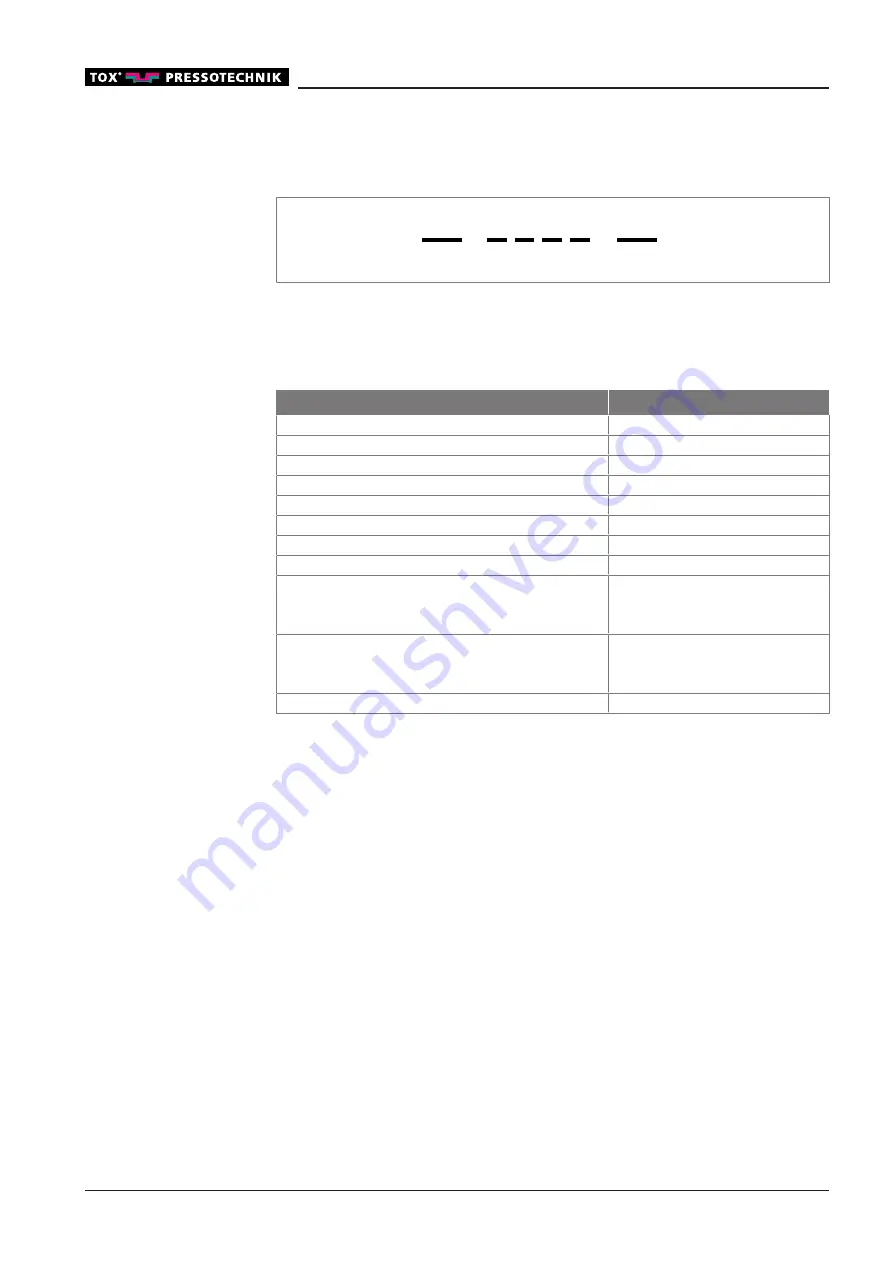
Troubleshooting
TOX_Manual_ElectricPowerDrive_EQe-K_en
47
10.3
Detecting faults TOX
®
-EdgeUnit
Fig. 9
Example blink code 4x blink
First, the LED lights up red for a long time, followed by a pause, and then
the LED lights up in blink code.
Error description
Error blink code
No content in the EProm
Red flashes permanently fast
Control system NOK - or no software installed
Lights up red
Control system OK - no error
Green flashes permanently
EtherCAT error
Red flashes 1x
Short-circuit at digital output
Red flashes 2x
Temperature outside of tolerance
Red flashes 3x
Encoder error
Red flashes 4x
Control system OK - Emergency stop actuated
Red flashes permanently
Voltage US1 outside of tolerance
Minimum: 22V
Maximum: 25V
Red flashes 6x
Voltage US2 outside of tolerance
Minimum: 22V
Maximum: 25V
Red flashes 7x
Supply voltage 5V faulty
Red flashes 8x
Summary of Contents for EQe-K
Page 2: ...2 TOX_Manual_ElectricPowerDrive_EQe K_en ...
Page 12: ...Important information 12 TOX_Manual_ElectricPowerDrive_EQe K_en ...
Page 26: ...About this product 26 TOX_Manual_ElectricPowerDrive_EQe K_en ...
Page 28: ...Technical data 28 TOX_Manual_ElectricPowerDrive_EQe K_en ...
Page 32: ...Transport and storage 32 TOX_Manual_ElectricPowerDrive_EQe K_en ...
Page 38: ...Installation 38 TOX_Manual_ElectricPowerDrive_EQe K_en ...
Page 44: ...Software 44 TOX_Manual_ElectricPowerDrive_EQe K_en ...
Page 48: ...Troubleshooting 48 TOX_Manual_ElectricPowerDrive_EQe K_en ...
Page 50: ...Maintenance table 50 TOX_Manual_ElectricPowerDrive_EQe K_en ...
Page 58: ...Maintenance 58 TOX_Manual_ElectricPowerDrive_EQe K_en ...
Page 60: ...Repairs 60 TOX_Manual_ElectricPowerDrive_EQe K_en ...
Page 64: ...Appendices 64 TOX_Manual_ElectricPowerDrive_EQe K_en ...
Page 65: ......
Page 66: ......
Page 70: ...Index 70 TOX_Manual_ElectricPowerDrive_EQe K_en ...