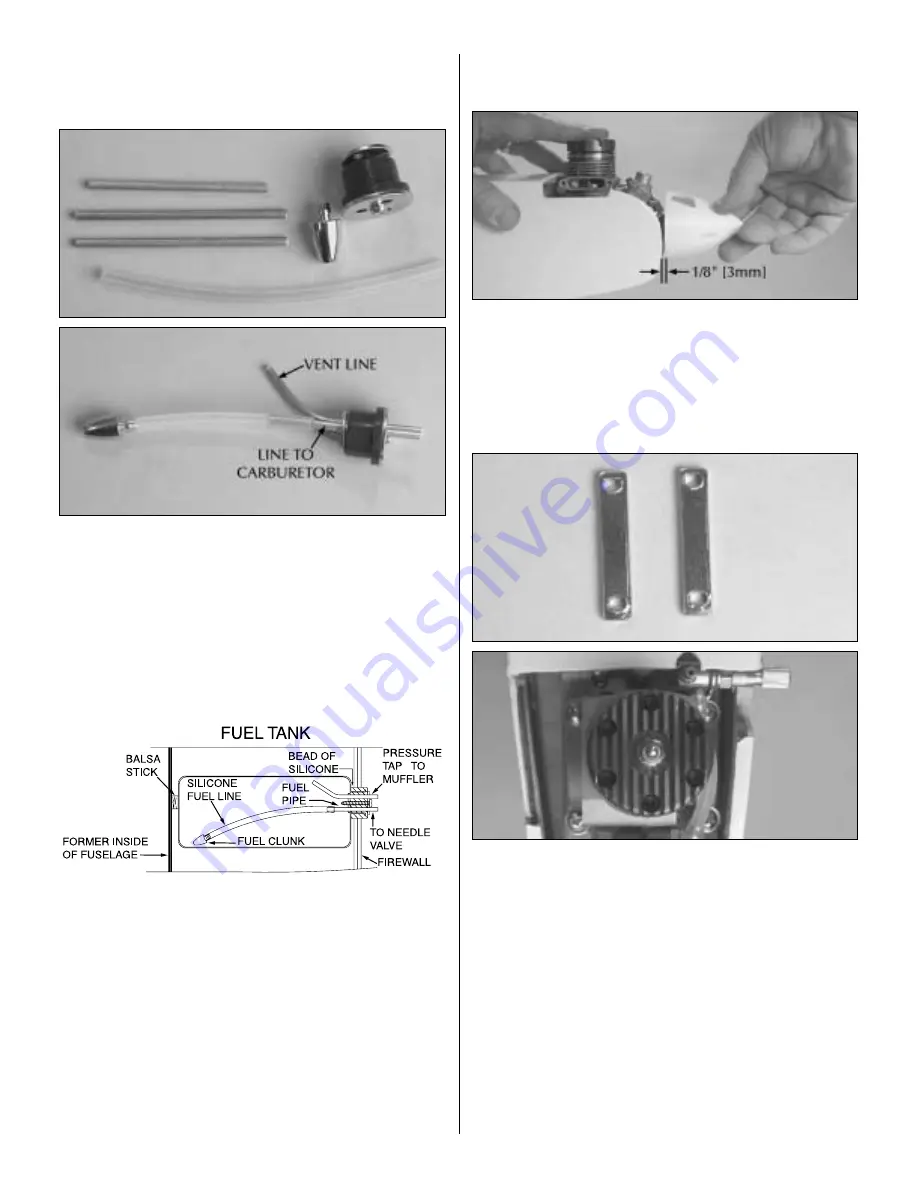
INSTALL THE FUEL TANK & ENGINE
❍
1. Locate the
fuel tank
. Remove the parts from inside of the tank.
❍
2. Assemble the components. Included in the fuel tank
parts are three aluminum tubes. If you will be fueling your
plane with a third line rather than filling the tank through the
carburetor line, you will need to use the third aluminum tube.
If not, assemble the tank as shown with a vent line and
carburetor line. Once assembled, use a fine tip marker and
mark the front of the fuel tank so you can identify which is the
vent line and which is the carburetor line.
❍
3. Insert the fuel tank into the fuselage. Hold the tank in
place either by using silicone glue around the front of the tank
or insert a small balsa stick (not supplied) behind the tank and
glue the stick to the former.
❍
4. Install fuel tubing on the aluminum lines, long enough
to reach the carburetor inlet and the pressure tap on the
muffler.
❍
5. Test fit your engine onto the engine mount. Depending
on your particular brand of engine and whether it has a
remote needle valve you may need to make additional cut-
outs or enlarge the cut-outs that are already made in the
engine compartment. Make the necessary adjustments as
needed to allow your engine to fit.
❍
6. Locate the
plastic spinner
. Remove the nut and washer
from the engine crankshaft and slide the spinner onto the
crankshaft. Place the engine on the engine mount, positioning
it so that there is a least 1/8" [3mm] clearance between the
back of the spinner and the sides of the fuselage. Remove the
spinner.
❍
7. Locate the two engine mounting straps. Install them on
the engine and engine mount by inserting a 4 x 25mm
machine screw, 4mm lock washer and a 4mm flat washer
through the holes in the end of the strap. Attach the strap to
the engine mount. Be careful not to push too hard on the nuts
you glued in the bottom of the engine mount earlier. Doing so
could cause the nuts to fall out of the mount, requiring you to
remove the engine mount to replace the nuts.
❍
8. Locate the remaining 14" [356mm] white pushrod tube.
Roughen one end of the tube with 220-grit sandpaper. Insert
the un-sanded end of the tube into the hole in the top right
side of the firewall. Apply a small amount of 6-minute epoxy
to the end of the white nylon tube. Position the tube so that it
extends beyond the firewall approximately 1/4" [6mm]. Allow
the epoxy to cure.
14