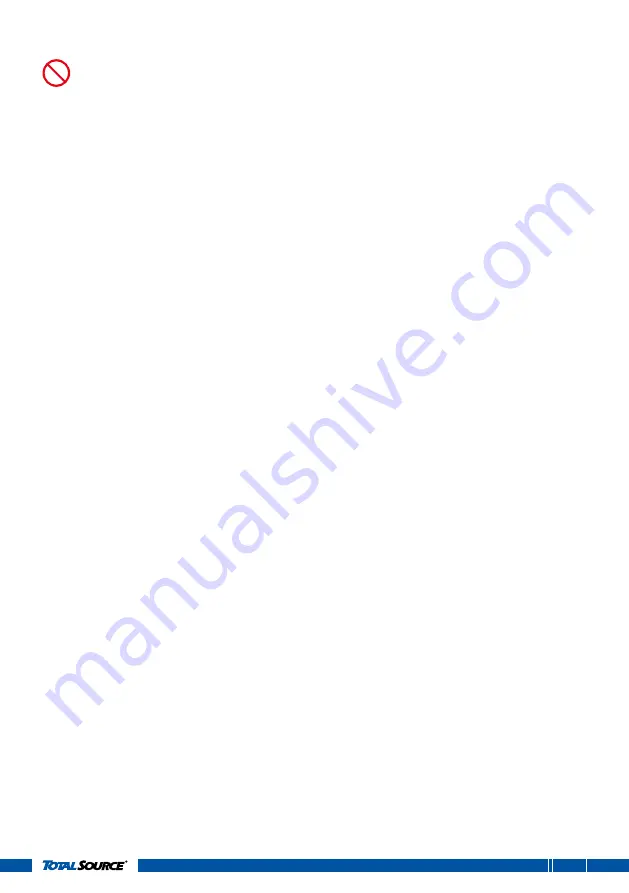
29/44
8.4. Battery maintenance instructions
Safety regulations for handling batteries
• Replacement of the battery may only be made by a qualified service technician and
according to the manufacturer’s instructions.
• Park the pallet truck securely before carrying out any work on the batteries.
• Batteries may only be charged, serviced or replaced by trained personnel.
The operator manual must be observed when carrying out the work.
• Fire protection:
– Smoking and open flames must be avoided when working with batteries.
– The area must be well ventilated.
– Fire protection equipment must be provided.
• Protection against electric shocks:
– The battery supplies a high voltage and current.
– Avoid short circuits.
– Keep metal objects and tools away from the two terminals of the battery,
as these could create sparks. Don’t wear any jewellery.
• Wear glasses to protect your eyes, rubber overshoes and rubber gloves
• Disconnect the battery plug
Batteries contain an acid solution which is poisonous and corrosive. Therefore,
always wear protective clothing and eye protection when carrying out work on
batteries. Above all, avoid any contact with battery acid.
Nevertheless, should clothing, skin or eyes come into contact with acid, the affected
parts must be rinsed with plenty of clean water. If the skin or eyes are affected, call a
doctor immediately. Immediately neutralise any spilled battery acid.
Battery maintenance
Following checks should be done monthly:
1. Check the nodes, such as the conductive strips and voltage collection terminals, for any
looseness, shedding, oxidation or deformation to ensure that the series-parallel harness
used in the battery pack is firm and reliable.
2. Check the battery casing for cracks, deformation, loose poles, bulging and other
abnormal conditions.
3. Check the reliability of the charging device to ensure that it performs the charging action
in accordance with the voltage regulation and current regulation, to ensure that the
battery is not overcharged.
4. Check the discharge protection equipment like fast-acting fuses, DC contactors and
relays to ensure that the battery pack can be quickly disconnected from the main circuit
in the event of a dangerous situation.
5. Check the insulation resistance between the battery pack and the vehicle body to ensure
that there is no electric leakage within the battery.
Do not overuse the battery. If you use up all the battery energy, you will shorten its
operational life. If the battery indicator shows an orange light, the battery must be charged
quickly.
The battery cell covers must be kept dry and clean. The terminals and cable shoes must
be clean, secure and have a light coating of dielectric grease. Batteries with non-insulated
terminals must be covered with a non-skid insulation mat.
Summary of Contents for ELP15EULIT
Page 35: ...35 44 12 ANNEXES 12 1 CE certificate...
Page 36: ...36 44...
Page 39: ...39 44 12 3 Hydraulic diagram...
Page 41: ...41 44 NOTES...
Page 42: ...42 44 NOTES...
Page 43: ...43 44 NOTES...