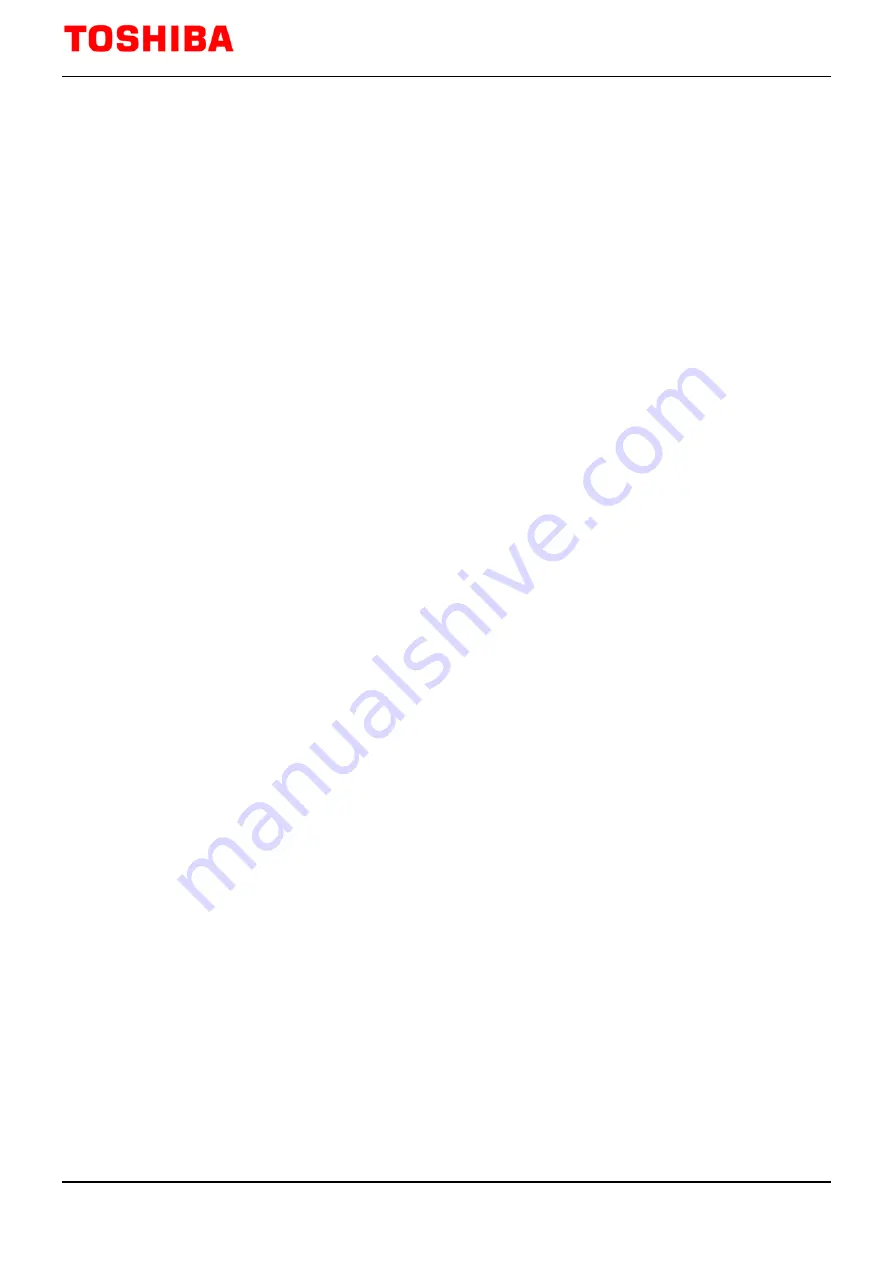
RD022-RGUIDE-01-E
2019-Jan-15
Rev.1.0
23
/
31
© 2019
Toshiba Electronic Devices & Storage Corporation
7.14.3. PI Tuning Procedure
1. Keep Ki and Kd values to zero at first, increase the Kp until the output of the loop oscillates. Then the
Kp should be set to about half of that value for a "quarter amplitude decay" type response.
2. Then increase Ki until any offset is corrected in sufficient time for the process. However, too much Ki
will cause instability.
3. The tuning is a repeat process to approach the balance between the response speed and system
stability.
7.14.4. Source code
err = rotateSpeedHp - detectedHp; //error = set value - actual value
if (detectedHp == 0) {
bias = Kp_s * (err - err1); // do once only at startup when speed is zero
}
else
{
bias = Kp * (err - err1) + Ki * err;
if (err < 2 && err > -2)
{
pidOver_U = pidOver2_U;
pidOver_D = pidOver2_D;
}
else
{
pidOver_U = pidOver1_U;
pidOver_D = pidOver1_D;
}
if (bias > pidOver_U)
bias = pidOver_U;
else if (bias < pidOver_D)
bias = pidOver_D;
}