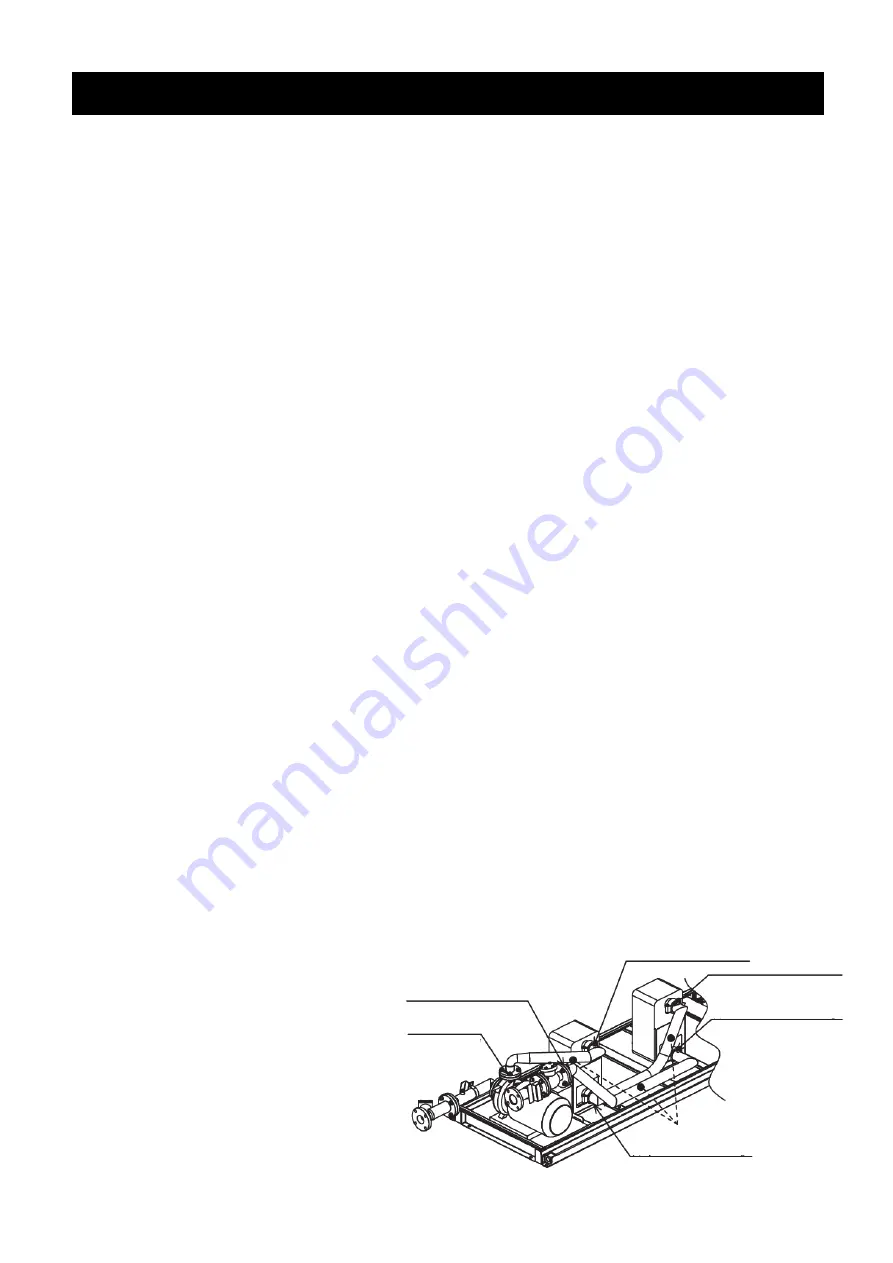
- 75 -
Scales can cause a drop in water heat exchanger capacity and a drop in the flow rate, which can lead to
fracturing due to freezing. Because of this, regularly scheduled maintenance is required to prevent scaling.
(1) Perform the checks described below before entering the operational season.
Perform a water quality test and confirm that the results are within standard.
Clean the strainer.
Confirm the water flow rate is to the specified required.
Confirm there are no operational problems (pressure, flow rate, entering/leaving temperature, etc.)
(2) The brazing water heat exchanger is manufactured in a way that does not allow it to be dismantled and
cleaned, so the below steps should be performed to clean it.
(a)
A 5% solution of formic acid, citric acid, oxalic acid, acetic acid, or phosphoric acid can be used as
an anti-scaling wash. Never use hydrochloric acid, sulphuric acid, nitric acid, or other strongly
corrosive agents.
(b)
Close the gate valves at the inlet and outlet of chilled (warm) water in the heat pump unit to
prevent water from entering the unit.
(c)
Drain water from the three drain plugs which are installed within each module. (See the Installation
Manual for the position of each plug.)
(d)
When water is drained completely, remove the clamp of water outlet, and remove downstream
water heat exchanger outlet connection ((1) in the figure below) and the flange of water outlet ((2)
in the figure below) to take out the pipes.
(e)
Remove upstream water heat exchanger outlet connection ((3) in the figure below) and
downstream water heat exchanger inlet connection ((4) in the figure below) to take out the pipes.
(f)
Remove upstream water heat exchanger inlet connection ((5) in the figure below) and the flange at
the internal pump discharging side ((6) in the figure below) to take out the pipes.
(g)
Connect the circuit pipe used for the chemical treatment to the inlet and outlet of the plate heat
exchanger, and fill the plate heat exchanger with cleaner at a temperature between 50°C and 60°C.
Next, use the pump to circulate the chemical for two to five hours. The circulation time depends on
the temperature of the chemical treatment and the scaling condition. The colour of the liquid being
removed should be taken into account to determine how much scale is being removed.
(h)
After circulating the chemical treatment, remove it from the plate heat exchanger. Next, fill the
plate heat exchanger with an aqueous solution of 1 to 2% sodium hydroxide (NaOH) or sodium
bicarbonate (NaHCO
3
). Circulate the solution for 15 to 20 minutes to neutralize.
(i)
After neutralization is complete, very carefully and thoroughly rinse the interior of the plate heat
exchanger with clean water.
(j)
When using a commercially available cleaning agent, confirm beforehand that it is a cleaning liquid
that does not corrode stainless steel or copper.
(k)
For detailed information about cleaning procedures, contact the manufacturer of the cleaning
agent.
(l)
After cleaning, return the removed three water drain plugs and three water pipes to the original
position.
(3) After cleaning, make sure that there are no water leaks and that the unit is operating normally.
Water Heat Exchanger Maintenance
(2) Chilled (warm) water outlet piping
flange
(6) Internal pump
discharge side flange
(5) Upstream water heat exchanger
inlet side connection
(4) Downstream water heat exchanger
inlet side connection
(1) Downstream water heat exchanger
outlet side connection
(3) Upstream water heat exchanger
outlet side connection
Remove the three pipes.