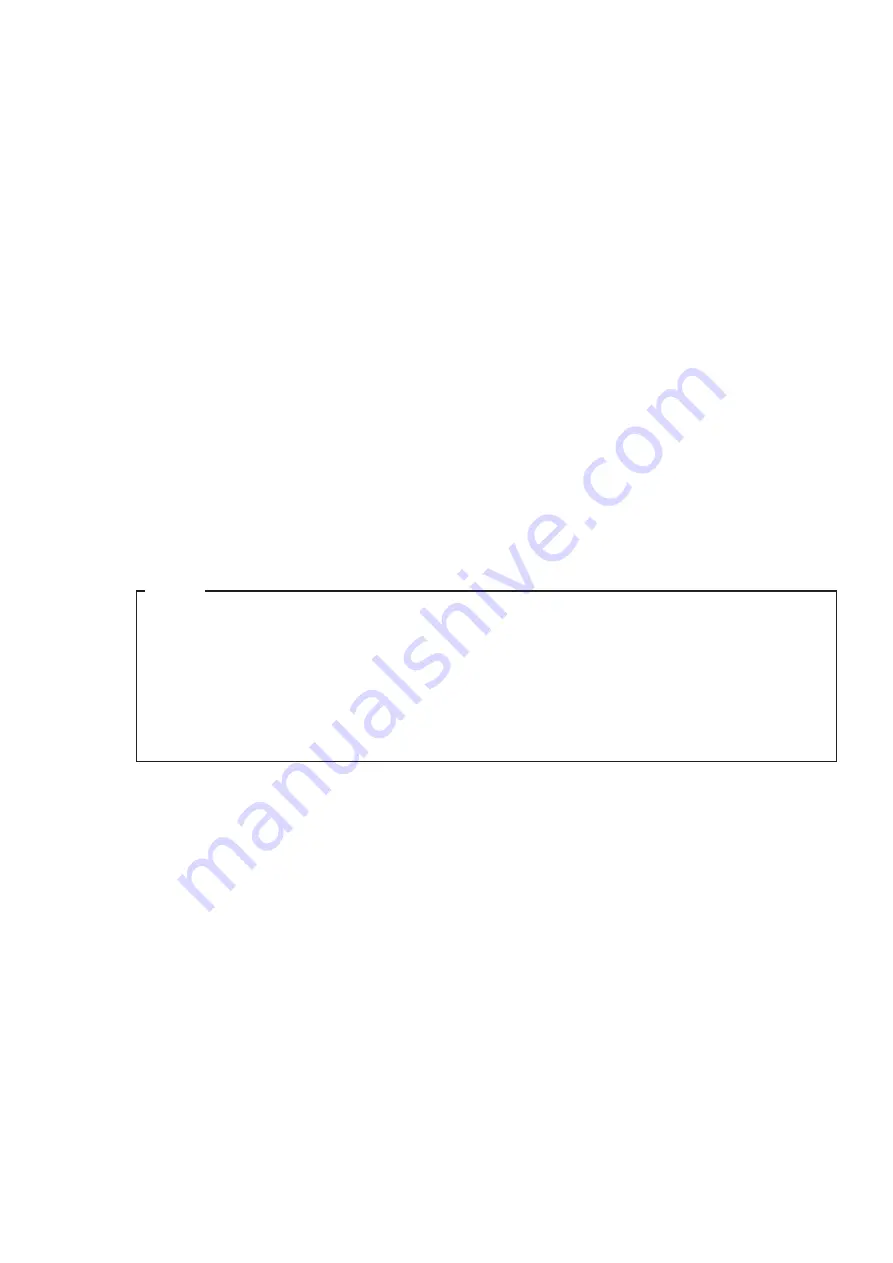
- 73 -
Note 3) Water System Maintenance
The appropriate water processing should be carried out to ensure the prevention of corrosion,
water scaling and also the pipework/equipment from freezing during the winter period.
When draining the complete system, pipework, water heat exchanger and intend to stop the
unit for a long period of time, the use of nitrogen gas to prevent internal corrosion is advised. In
places where the temperature can drop below 0°C, the use of a specified antifreeze is
permitted and should be circulated through the whole water system before draining any water.
Care should be taken when choosing the antifreeze to ensure it does not corrode any parts of
the water system.
Trained professionals should be used throughout maintenance activities and should be
working to the relevant regulations and legislation of the water service provider.
Note 4) Water Quality Management
The brazing water heat exchanger is manufactured in a way that does not allow it to be
dismantled, cleaned or have components replaced. Care should be taken in regards to the
quality of water used in the water heat exchanger in order to prevent corrosion and water
scaling.
When using a rust inhibitor, scale inhibitor, or any other type of agent, make sure that it is a
type that will not corrode cast iron, stainless steel, copper, bronze, rubber and gasket.
Note 5) Flow rate management
An insufficient chilled (warm) water flow rate is one of the faults that can cause the freezing of
the water plate heat exchanger. If the flow rate has been reduced, the following could be the
cause; Clogged strainer, cavitation, faulty water pump etc. Also, measurement should be taken
of the temperature difference and pressure differential between the water plate heat exchanger
inlet and outlet. An increase of temperature or pressure differential beyond the specified range
could indicate a drop in the water flow rate. If the case of a reduced flow rate, stop the system,
rectify the fault and restart operation.
Note 6) Antifreeze density management
When using antifreeze in the chilled (warm) water, use it only in the models and at the
densities specified by the manufacturer. Do not use calcium chloride antifreeze, which will
corrode the plate heat exchanger.
Antifreeze will absorb water in the air and lose density over time. Low antifreeze density can
cause the water plate heat exchanger to freeze up, so it is important to minimize the amount of
antifreeze surface area exposed to the atmospheric air. Also, measure the density of the
antifreeze at regular intervals and replenish it as required to maintain the proper density.
Note 7) Precautions for freeze protection measures during winter
In locations where the winter temperatures can drop to 0°C or less, the pump installation
location and the water piping should be taken into consideration.
In the cases where installation conditions or structural limitations make it impossible to locate
the pump where it will prevent freezing or pipework where you cannot fully insulate, the
previous steps should be carried out to protect the system against freezing.
(1) Consider the installation position of pump freeze protection thermostat sensors at locations
where the water temperature in the pump or piping drops the earliest to trigger pump
operation.
If operation of a freeze protection device is triggered while operation is in progress, be sure to
eliminate the cause before restarting operation. The plate heat exchanger is partially frozen at the
moment that a freeze protection device operation is triggered. Attempting to restart operation
without first eliminating the cause not only make it impossible to melt ice that is blocking the plate
heat exchanger, repeated freezing will damage the plate heat exchanger, and lead to refrigerant
leaks and the invasion of water into the refrigerant circuit.
Note