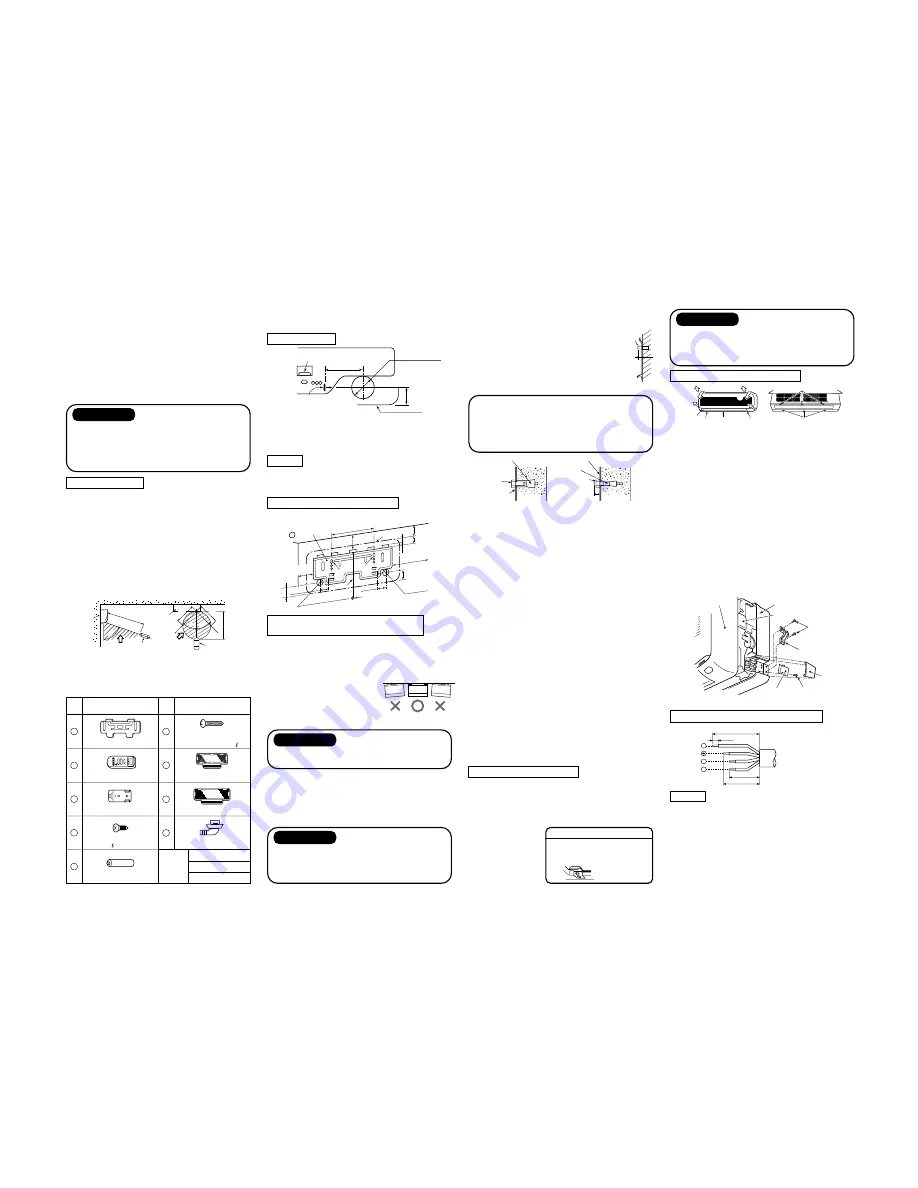
– 17 –
8-3. Indoor Unit
8-3-1. Installation Place
• A place which provides the spaces around the
indoor unit as shown in the above diagram.
• A place where there is no obstacle near the air inlet
and outlet.
• A place which allows an easy installation of the
piping to the outdoor unit.
• A place which allows the front panel to be opened.
CAUTION
• Direct sunlight to the indoor unit wireless
receiver should be avoided.
• The microprocessor in the indoor unit should
not be too close to r-f noise sources.
(For details, see the owner's manual.)
Remote control
• A place where there are no obstacles such as a
curtain that may block the signal from the indoor
unit.
• Do not install the remote control in a place exposed
to direct sunlight or close to a heating source, such
as a stove.
• Keep the remote control at least 1 m apart from the
nearest TV set or stereo equipment.
(This is necessary to prevent image disturbances or
noise interference.)
• The location of the remote control should be
determined as shown below.
Fig. 8-3-1
8-3-2. Installation Parts
Part with an asterisk (
*
) is packaged with outdoor unit.
Deodorizing filter x 1
Purifying filter x 1
Name
Owner’s manual
Installation manual
1
5
9
2
6
3
7
4
8
Name of parts (Q'ty)
Part
No.
Name of parts (Q'ty)
Part
No.
Installation plate x 1
Wireless remote control x 1
Remote control holder x 1
Pan head wood screw
Ø3,1 x 16 x 2
Batteries x 2
Mounting screw Ø4x 25 x 8
Drain nipple
*
x 1
Others
(Top view)
Indoor unit
5m
5m
45˚
45˚
Remote
control
Reception
range
*
: Axial distance
Remote
control
Reception
range
7m
Indoor unit
(Side view)
*
7m
75˚
8-3-3. Cutting a Hole and Mounting
Installation Plate
Cutting a hole
47mm
100mm
Refrigerant pipe hole
Ø65mm
Indoor unit outline
Hooking
section
Center of pipe hole is located
on the line indicated by the
arrow and 100 mm apart from
the pipe hole center line.
Fig. 8-3-2
When installing the refrigerant pipes from the rear.
Determine the pipe hole position using the installation
plate, and drill the pipe hole Ø65 mm slightly downward.
NOTE
When using the drill to pierce the wall that contains a
metal lath, wire lath or metal plate, be sure to use a
pipe hole brim ring sold separately.
Mounting the installation plate
For installation of the indoor unit, use the paper
pattern on the back.
Fig. 8-3-3
When the installation plate is directly
mounted on the wall
100mm
44mm
or more
40mm
130mm
or more
450mm
Anchor
bolt hole
Refriger
ant pipe hole
Ø65mm
1 Installation plate
Refriger
ant
pipe hole
Ø65mm
Indoor unit
outline
Thread
Weight
100mm
47mm
4mm
40mm
21mm
80mm
or more
1. Securely fit the installation plate onto the wall by
screwing it in the upper and lower parts to hook up
the indoor unit.
2. To mount the installation
plate on a concrete wall with
anchor bolts, utilize the
anchor bolt holes as
illustrated in the above figure.
3. Install the installation plate
horizontally in the wall.
Installation plate
(Keep horizontal direction)
Fig. 8-3-4
CAUTION
Failure to firmly install the unit may result in
personal injury and property damage if the unit falls.
1. Adjust the lateral position of the installation plate
without changing the height, so that each screw hole
in the plate comes in the center of a pillar or stud.
2. Make pilot holes with a bit to prevent the studs
from cracking, and then drive the screws into the
holes and tighten.
CAUTION
When installing the installation plate with
mounting screw, do not use the anchor bolt hole.
Otherwise the unit may fall down and result in
personal injury and property damage.
• In the case of a reinforced concrete wall
(1) In the selected area on the reinforced concrete wall,
bore holes at intervals of 450 mm, and drive
clip anchors or hole in anchors into them.
(2) Attach the installation plate to the wall by
screwing bolts or nuts into the anchors.
However, in the case where hole in
anchors are used, the depth of the
holes should be adjusted so that the nut-
heads extend no more than 15 mm.
Fig. 8-3-5
Anchor
bolt
Projection
15mm
or less
• There may be a wire conduit embedded in the wall.
Confirm on the blue prints or ask the builder.
• Install the installation plate using 4 to 8 pieces of
mounting screw securing four corners with screws.
• Make sure of the proper installation of the
installation plate before mounting the indoor unit.
Concrete wall
Concrete wall
Installation
plate
Hole in anchor
Bolt
Hole in anchor
Installation plate
Nut with threaded
hole 8 mm dia.
Less than 15 mm
Fig. 8-3-6
• In the case of the pipe on the back
Using the pattern, position the pipe hole, and bore the
hole slightly downward.
8-3-4. Electrical Work
Important items of indoor unit wiring
1. For electrical works the wiring and cables must be
performed in compliance with national wiring
standard or regulation. If incorrect and incomplete
wiring is carried out, it will cause an electrical fire
or electrical shock.
2. Do not use the inter-connecting cable.
Never execute the connection of electrical wiring
with other method than the approved one.
(exp. use the terminal block etc.)
3. Prepare the interior power supply cord capacity
sufficient for starting and usage current of air
conditioner.
4. Connect the connecting cable to the terminal as
identified with their respective matched numbers
on the terminal block of outdoor unit.
5. Fix the cable securely with the cord clamps to the
specified position.
6. Do not damage or scratch the conductive core &
inner insulator of power supply and inter
connecting cables when peeling them.
7. Do not deform or smash the surface of the cables.
Do not press or fix the cord and cables firmly with
staples, etc.
How to connect the cable
1. Remove the side panel. (2 screws)
2. Remove the electric parts cover and cord clamp.
3. Insert the connecting cable fully into the terminal
block and secure it by screw tightly.
Tightening torque : 1,2 N•m (0,12 kgf•m)
4. Secure the con-
necting cable with
the cord clamp.
5. Fix the electric
parts cover and
side panel.
How to open the screw cap
• Place your finger on the
lower part and push up to
open the screw cap.
Fig. 8-3-7
CAUTION
• Be sure to refer the wiring system diagram
labeled inside the side panel.
• Check local electrical codes and also any
specific wiring instruction or limitation.
How to remove the front panel
Fig. 8-3-8
(1) Open the screw caps and remove three front
panel fixing screws.
(2) Put the screw caps back as they were.
(3) Press the part saying “PUSH” on the air inlet grille
to open the air inlet grille.
Remove three black front panel fixing screws.
(4) Close the air inlet grille.
(5) Manually open the vertical air flow louver directly
below.
(6) Open the front panel lower portion until it comes in
contact with the vertical air flow louver. Lift up the
front panel upper portion in a forward diagonal
direction to unhook the clicks inside the front
panel upper portion.
(7) After unhooking the nails inside the main unit
upper portion, rotate the front panel upper portion
towards you to remove the front panel from the
unit body.
(6)
Screws
(6)
(7)
(7)
(1) (2)
(1) (2)
(1) (2)
Screw caps and screws
(5)
(3) (4)
(3) (4)
Fig. 8-3-9
Stripping length of connecting cable
Front panel
Rear plate
Rear plate
bushing
Electrical component
box cover
Screws
Cord clamp
Wiring cover
Screw
Fig. 8-3-10
NOTE
• Use standard wire only
• Wire type : More than H05 RN-F (1,3 mm² or more)
• Insert the connecting cable fully into the terminal
block and secure it by screw tightly.
• Tightening torque : 1,2 N•m (12 kgf•cm)
• Secure the connecting cable with the cord clamp.
• Fix the wiring cover, rear plate bushing and front
panel on the indoor unit.
3
2
1
10 mm
220 mm
50 mm
60 mm