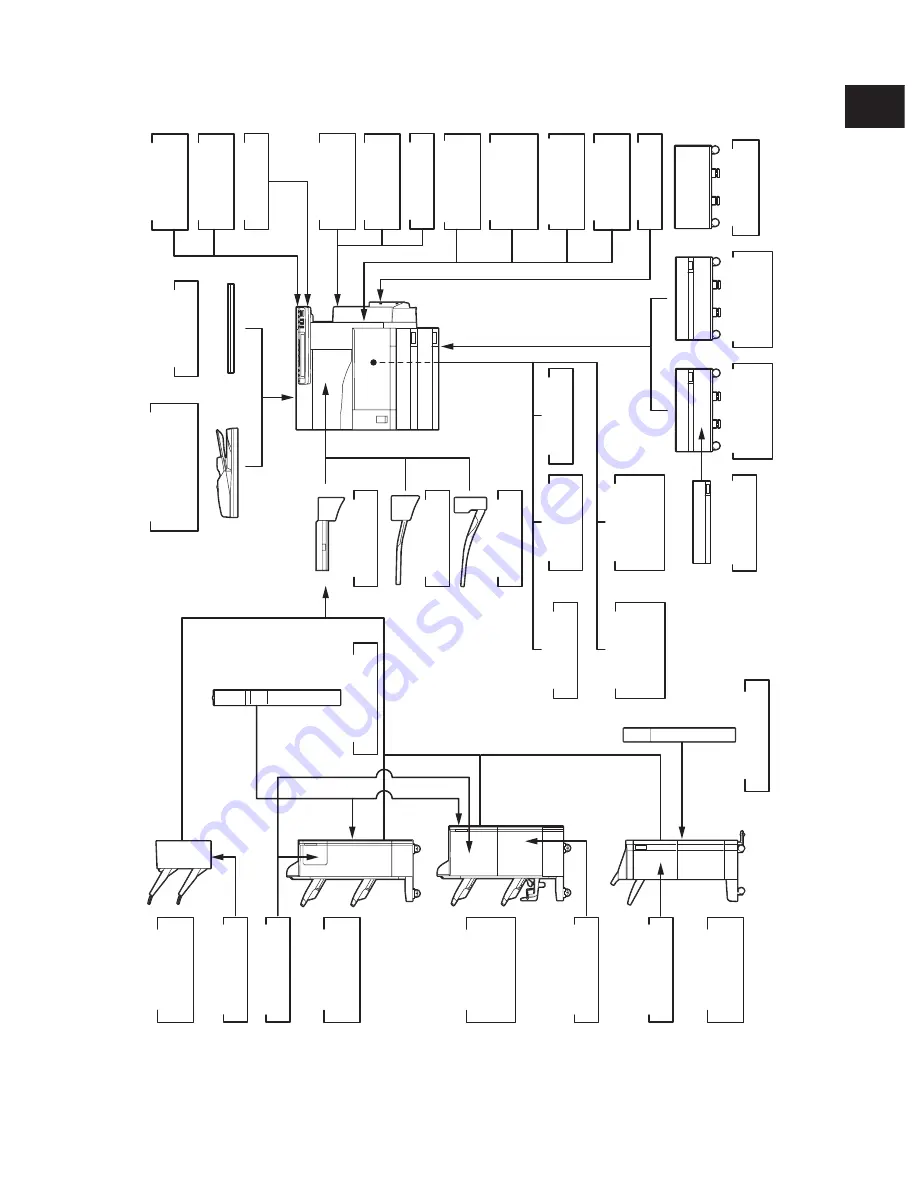
1 - 11
© 2003 - 2008 TOSHIBA TEC CORPORATION All rights reserved
1
e-STUDIO350/352/353/450/452/453
SPECIFICATIONS
1.5.2 e-STUDIO352/353/452/453
Work Tray
KK-3511
Antenna
GN-3010
Memory
GC-1230
Printer/
Scanner Kit
. ELK
GM-2060/2061
GM-2120
Scanner Kit
. ELK
GM-4060
GM-4120
Printer Kit
. ELK
GM-1060/1061
GM-1120
Wireless LAN
Module
GN-1041
e-BRIDGE
ID Gate
KP-2005
e-BRIDGE
ID Gate
KP-2004
Bluetooth
Module
GN-2010
Data
Overwrite Kit
GP-1060
Platen Cover
KA-3511
Reversing Automatic
Document Feeder
( RADF
)
MR-3018
Bridge Kit
KN-3520
Job Separator
MJ-5004
Offset Tray
MJ-5005
Scrambler
Board
GP-1040
PCI Slot
GO-1060
FAX Board
GD-1200
NA/EU/AU/AS/
C/TW/KR
2nd Line for
FAX Board
GD-1160
NA/EU-N/TW/C
Damp Heater
MF-3520 U/E
Desk
MH-1700
Drawer Module
MY-1021
Large Capacity
Feeder (LCF)
KD-1012 A4/LT
Paper Feed
Pedestal (PFP)
KD-1011
Hole Punch Unit
MJ-6101 N/E/F/S
Staple Cartridge
STAPLE-1600
Staple Cartridge
STAPLE-2000
Hole Punch Unit
MJ-6004 N/E/F/S
Staple Cartridge
STAPLE-600
Staple Cartridge
STAPLE-2400
Finisher
( Hanging type
)
MJ-1022
Finisher
( Console type
)
MJ-1023
Finisher
( Console type
)
MJ-1101
Finisher
( Console saddle
stitcher type)
MJ-1024
Fig. 1-502
08/04