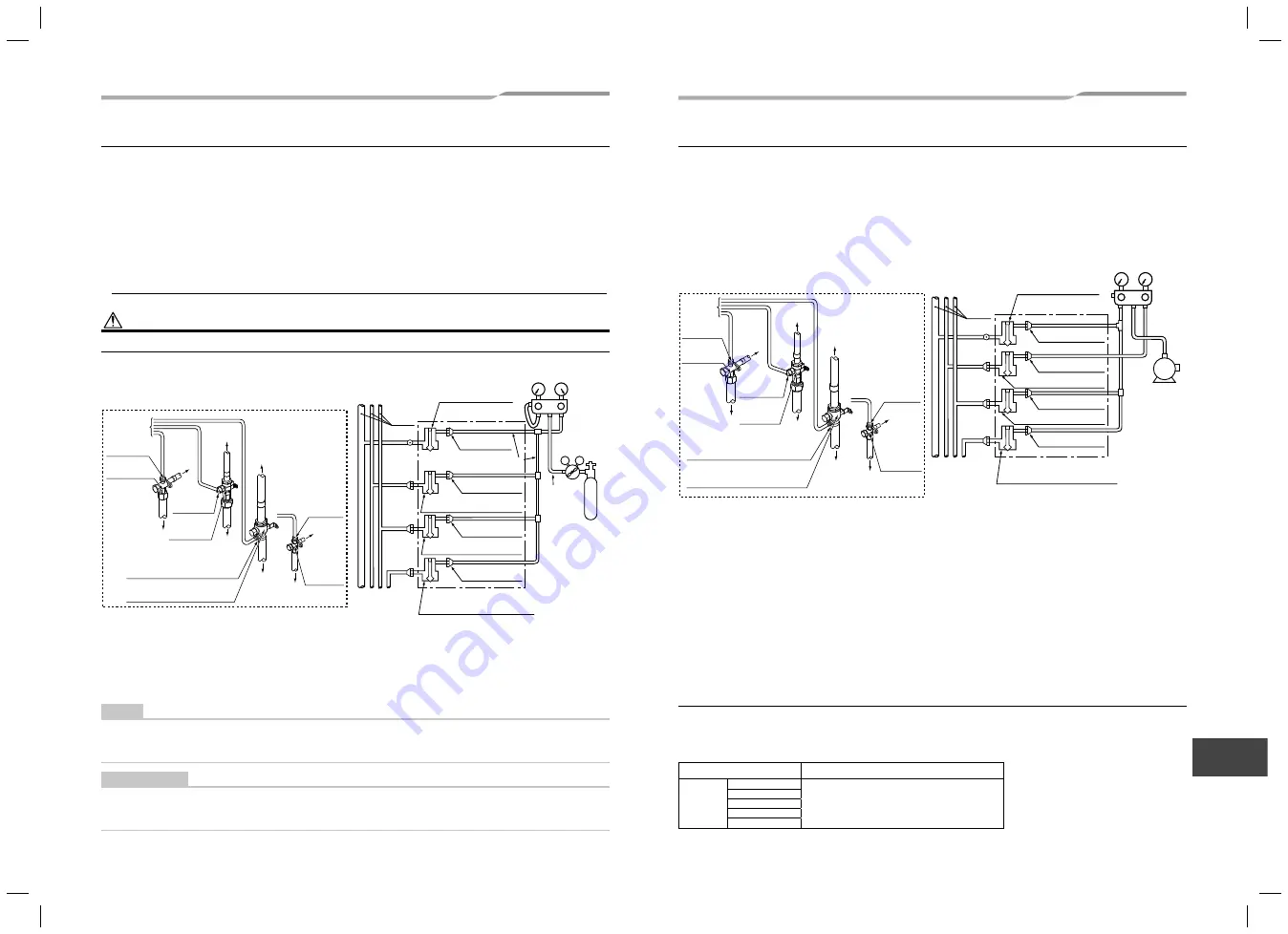
– 14 –
27-EN
28-EN
EN
FR
■
Vacuum drying
• Be sure to use a vacuum pump equipped with the counter-flow prevention function so that oil in the pump will
not flow back into piping for air conditioners. (If oil in the vacuum pump enters in the air conditioner with R410A
refrigerant, a problem may be caused in the refrigerating cycle.)
After finishing the airtight test and discharging nitrogen gas, connect the gauge manifold to the service ports of the
suction gas side, discharge gas side, liquid side and balance pipe side and connect a vacuum pump as shown
in the figure below. Be sure to perform vacuuming for the suction gas side, discharge gas side, liquid side and
balance pipe side.
P
V
L
V
H
Packed valve details
To gauge
manifold
Liquid-side
service port
Liquid-side
valve
Piping at site
To
outdoor
unit
Piping
at site
To outdoor unit
Piping
at site
Connected to
other follower
units
Main
pipe
Connected to
indoor unit
Low pressure
gauge
High pressure
gauge
Gauge
manifold
Vacuum
pump
Balanced pipe side valve fully
closed
Liquid side valve fully
closed
Discharge gas side valve
fully closed
Fully
closed
Fully
closed
Fully
closed
Brazed
Suction gas side valve
fully closed
Header outdoor unit
Service port
Service port
Service port
Piping
at site
Ball valve of suction gas side
Service port of suction gas side
Service port
of discharge
gas side
Ball valve of
discharge
gas side
To outdoor
unit
To
gauge
manifold
Service
port
of balance
pipe side
Packed
valve
of balance
pipe side
To
outdoor
unit
Service port
• Use a vacuum pump with a high vacuuming degree [14.6 psi (5Torr, -755mmHg)] and large exhaust gas amount
(40L/minute or larger).
• Perform vacuuming for 2 or 3 hours, though the time differs depending on the pipe length. Check that all the
valves at the suction gas side, discharge gas side, liquid side and balance pipe side are fully closed.
• If the pressure does not reach 14.6 psi or less even after vacuuming for over 2 hours, continue vacuuming for 1
hour or more. If the pressure does not reach 14.6 psi after 3 hours of vacuuming, stop vacuuming and check for
air leakage.
• If the pressure reaches 14.6 psi or less after vacuuming for 2 hours or more, close the valves VL and VH on
the gauge manifold fully and stop the vacuum pump. Leave it as it is for 1 hour to con
fi
rm that the vacuuming
degree does not change.
If the degree of vacuum loss is large, moisture may remain in the pipes. In that case, inject dry nitrogen gas and
apply pressure to 7.3 psi and perform vacuuming again.
• After
fi
nishing the above procedure of vacuuming, exchange the vacuum pump with a refrigerant canister and
advance to the additional charging of refrigerant.
■
Adding refrigerant
After finishing vacuuming, exchange the vacuum pump with a refrigerant canister and start additional
charging of refrigerant.
1. Refrigerant charge amount at shipment from the factory does not include the refrigerant for pipes at the local site.
For refrigerant to be charged in pipes at the local site, calculate the amount and charge it additionally.
Model name
Refrigerant amount charged in factory
MMY-MAP
0726FT9P-UL
24.3 lbs
0966FT9P-UL
1206FT9P-UL
1446FT9P-UL
1686FT9P-UL
2. Additional refrigerant charge, please calculate from the calculation of additional refrigerant charge amount.
■
Airtightness test
After the refrigerant piping has been finished, execute an airtight test.
For an airtight test, connect a nitrogen gas canister as shown in the figure on this page and apply pressure.
• Be sure to apply pressure from the service ports of the packed valves (or ball valves) at the suction gas side,
discharge gas side, liquid side and balance pipe side.
• An airtight test can only be performed at the service ports at the suction gas side, discharge gas side, liquid side
and balance pipe side.
• Close the valves fully at the suction gas side, discharge gas side, liquid side and balance pipe side. As there is
a possibility that the nitrogen gas will enter into the cycle of outdoor units, re-tighten the valve rods at the liquid
side and balance pipe side before applying pressure.
• For each refrigerant line, apply pressure gradually in steps at the suction gas side, discharge gas side, liquid
side and balance pipe side.
Be sure to apply pressure at the suction gas side, discharge gas side, liquid side and balance pipe side.
WARNING
Never use oxygen, flammable gases, or noxious gases in an airtight test.
V
L
V
H
Packed valve details
To gauge
manifold
Liquid-side
service port
Liquid-side
valve
Piping at site
To
outdoor
unit
Piping
at site
To outdoor unit
Piping
at site
Connected to
other follower units
Main
piping
Connected to
indoor unit
Low pressure
gauge
High pressure
gauge
Gauge
manifold
Reducing
valve
Ø6.4
copper
pipe
Nitrogen
gas
Balanced pipe side valve
fully closed
Liquid side valve fully closed
Discharge gas side valve
fully closed
Fully
closed
Fully
closed
Fully
closed
Brazed
Suction gas side valve
fully closed
Header outdoor unit
Ø6.4 copper pipe
Service port
Service port
Service port
Service port
Piping
at site
Ball valve of suction gas side
Service port of suction gas side
Service port
of discharge
gas side
Ball valve of
discharge
gas side
To outdoor
unit
To
gauge
manifold
Service
port
of balance
pipe side
Packed
valve
of balance
pipe side
To
outdoor
unit
Able to detect a serious leakage
1. Apply pressure 43.5 psi (0.3 MPa) for 5 minutes or more.
2. Apply pressure 217.5 psi (1.5 MPa) for 5 minutes or more.
Available to detect slow leakage
3. Apply pressure 601 psi (4.15 MPa) for approx. 24 hours.
• If there is no pressure decrease after 24 hours, the test is passed.
NOTE
However, if the environmental temperature changes from the moment of applying pressure to 24 hours after that,
the pressure will change by about 1.45 psi (0.01 MPa) per 1.8 °F. Consider the pressure change when checking
the test result.
REQUIREMENT
When pressure decrease is detected in steps 1-3, check the leakage at the connecting points.
Check the leakage using a foaming agent or other measures and seal the leak with re-brazing, flare retightening
or other methods. After sealing, execute an airtight test again.
1122001101_EN FR.indd 14
1122001101_EN FR.indd 14
6/27/16 4:58 PM
6/27/16 4:58 PM