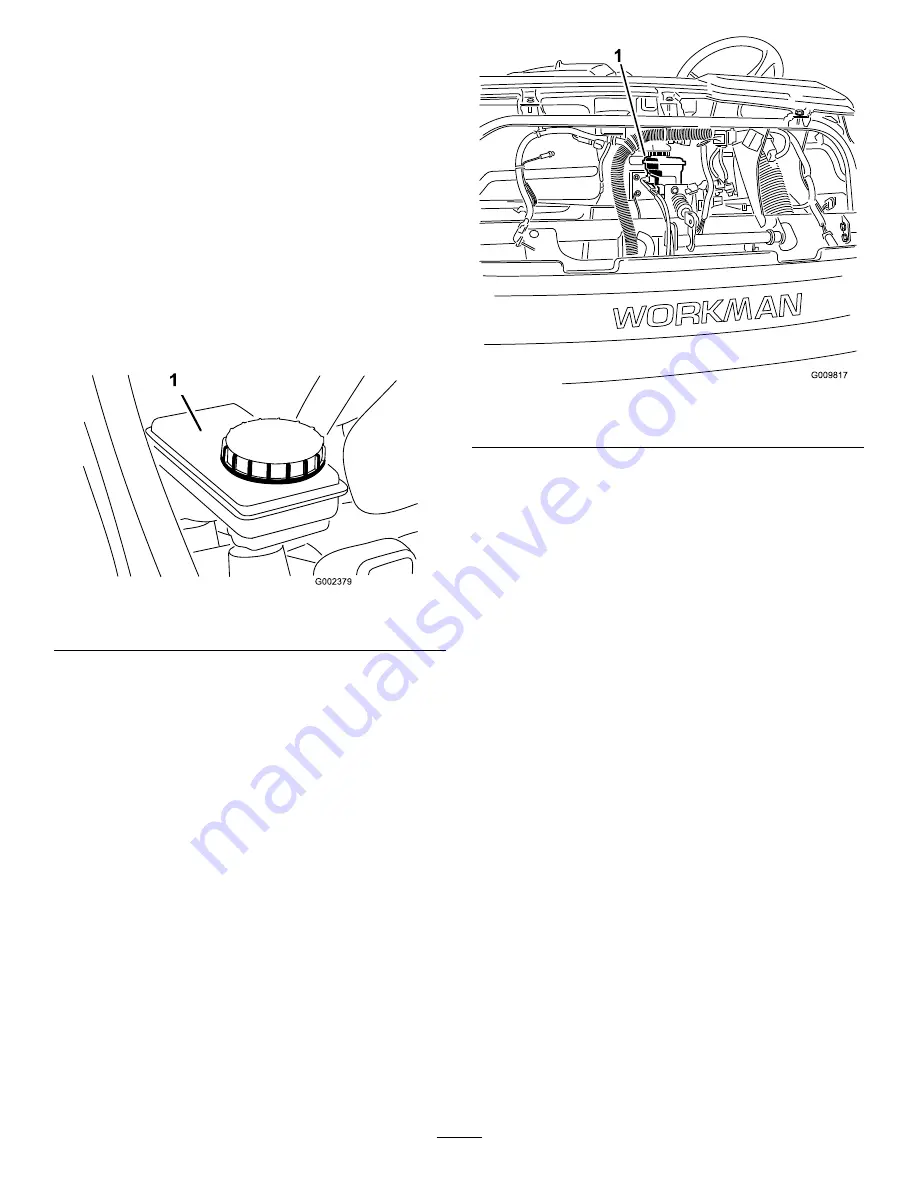
Checking the Brake-Fluid
Level
Service Interval:
Before each use or daily—Check the
brake-fluid level. (Check the level before
the engine is first started and every 8
hours or daily, thereafter.)
Every 1,000 hours/Every 2 years (whichever comes
first)—Change the brake fluid.
Brake fluid type:
DOT 3 brake fluid
The brake-fluid reservoir is located under the dash.
1.
Park the machine on a level surface.
2.
Ensure that the fluid level is up to the Full line on the
reservoir (
).
Figure 19
1.
Brake-fluid reservoir
3.
If the fluid level is low, clean the area around the cap,
remove the reservoir cap, and fill the reservoir to the
proper level with the specified brake fluid (
Note:
Do not overfill the reservoir with brake fluid.
Note:
You can remove the hood access to the reservoir from
the front of the machine (
Figure 20
1.
Brake-fluid reservoir
Starting the Engine
1.
Sit on the operator’s seat and engage the parking brake.
2.
Disengage the PTO and the high-flow hydraulics (if
equipped) and move the throttle lever to the O
FF
position (if equipped).
3.
Move the shift lever to the N
EUTRAL
position and
press the clutch pedal.
4.
Ensure that the hydraulic-lift lever is in the center
position.
5.
Keep your foot off the accelerator pedal.
6.
Insert the key into the ignition switch and rotate it
clockwise to start the engine.
Note:
Release the key when the engine starts.
Important:
To prevent overheating of the starter motor,
do not engage starter longer than 15 seconds. After 15
seconds of continuous cranking, wait 60 seconds before
engaging the starter motor again.
24
Summary of Contents for Workman HD 07369
Page 55: ...Notes 55...