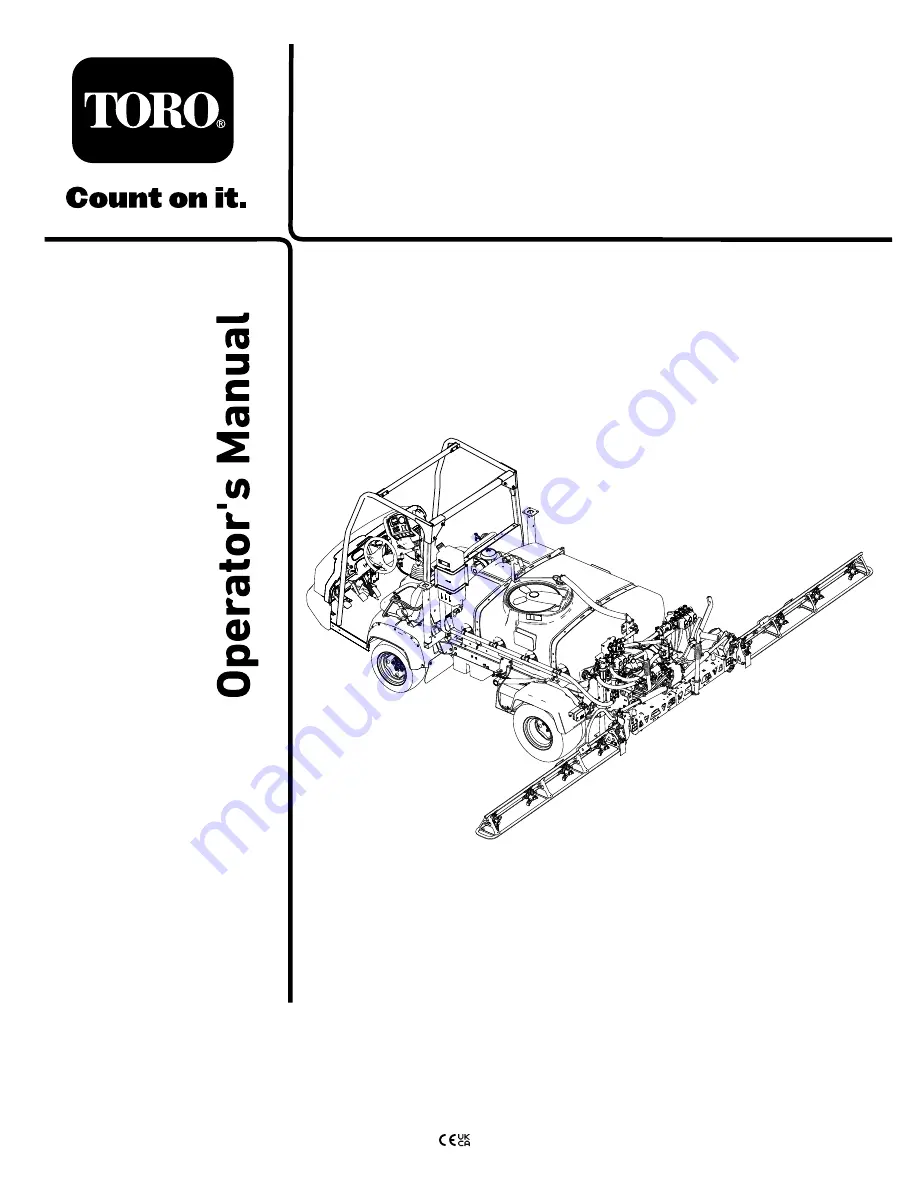
Form No. 3447-819 Rev A
Note:
The installation of the Multi Pro WM requires the installation
of 1 or more interdependent kits. Contact your authorized
Toro distributor for more information.
Multi Pro
®
WM Turf Sprayer
Model No. 41240—Serial No. 409500000 and Up
Register at www.Toro.com.
Original Instructions (EN)
*3447-819*