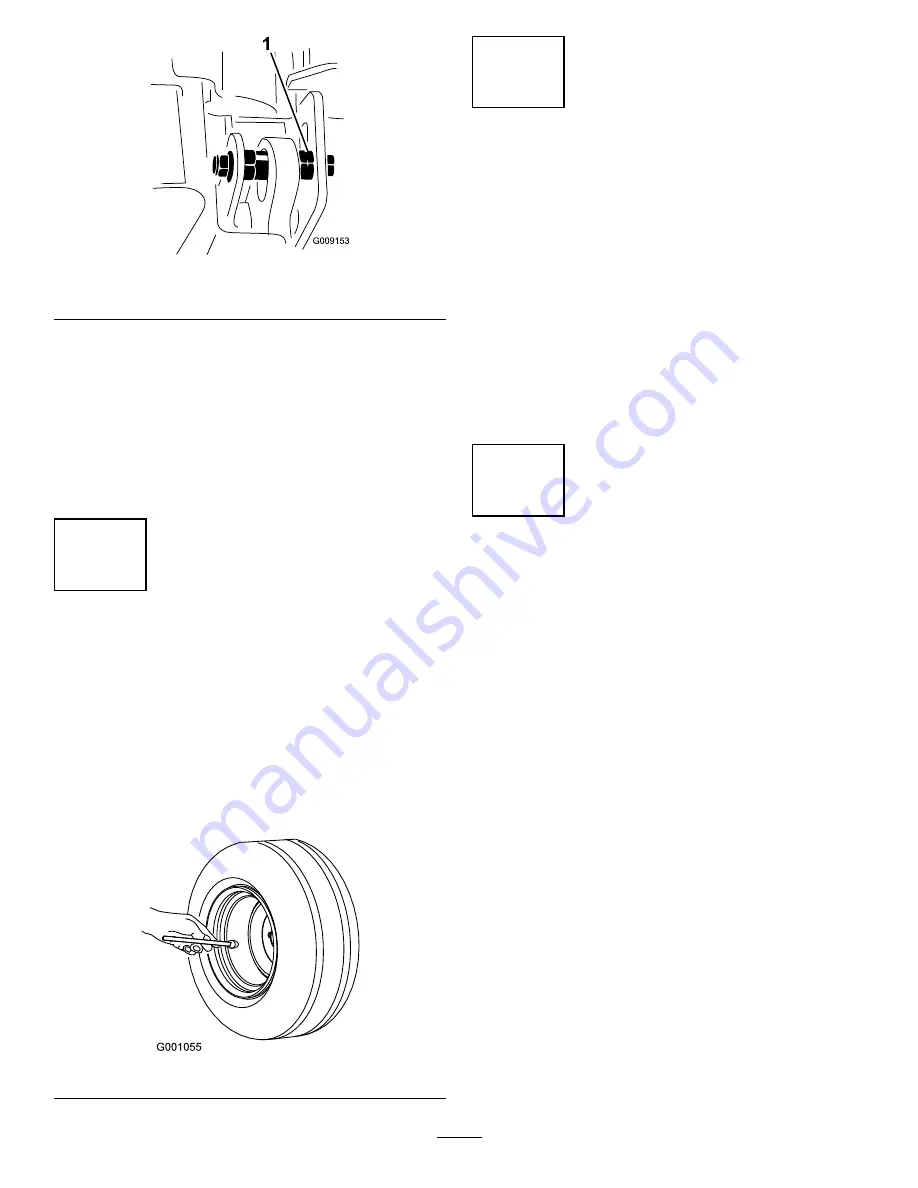
Figure 8
1.
Eccentric notch
•
Tighten the bolt and nut for this eccentric to 149 N-m
(110 ft-lb).
•
Adjust the forward eccentric until it just makes contact
with the inner slot surface of the winglet pivot brackets.
•
Tighten the bolt and nut for this eccentric to 149 N-m
(110 ft-lb).
•
Repeat the procedure on the opposite winglet. Refer to
Adjusting the Cutting Unit Pitch procedure in Mower
Maintenance.
5
Checking the Tire Pressure
No Parts Required
Procedure
Check the air pressure in all the tires before operating the
machine. The correct air pressure in the front tires is 345 kPa
(50 psi) and the rear tires is 207 kPa (30 psi) (
).
Important:
Maintain pressure in all tires to ensure a
good quality-of-cut and proper machine performance.
Do not under-inflate.
Figure 9
6
Checking the Fluid Levels
No Parts Required
Procedure
1.
Check the engine oil level before starting the engine,
refer to Checking the Engine Oil Level in Engine
Maintenance.
2.
Check the hydraulic fluid level before starting the
engine, refer to Checking the Hydraulic Fluid Level in
Hydraulic System Maintenance.
3.
Check the cooling system before starting the engine;
refer to Checking the Cooling System in Cooling
System Maintenance.
7
Greasing the Machine
No Parts Required
Procedure
Before the machine is operated, it must be greased to
ensure proper lubricating characteristics; refer to Greasing
the Bearings and Bushings procedure in Lubrication in the
Maintenance Section. Failure to properly grease the machine
will result in premature failure of critical parts.
18