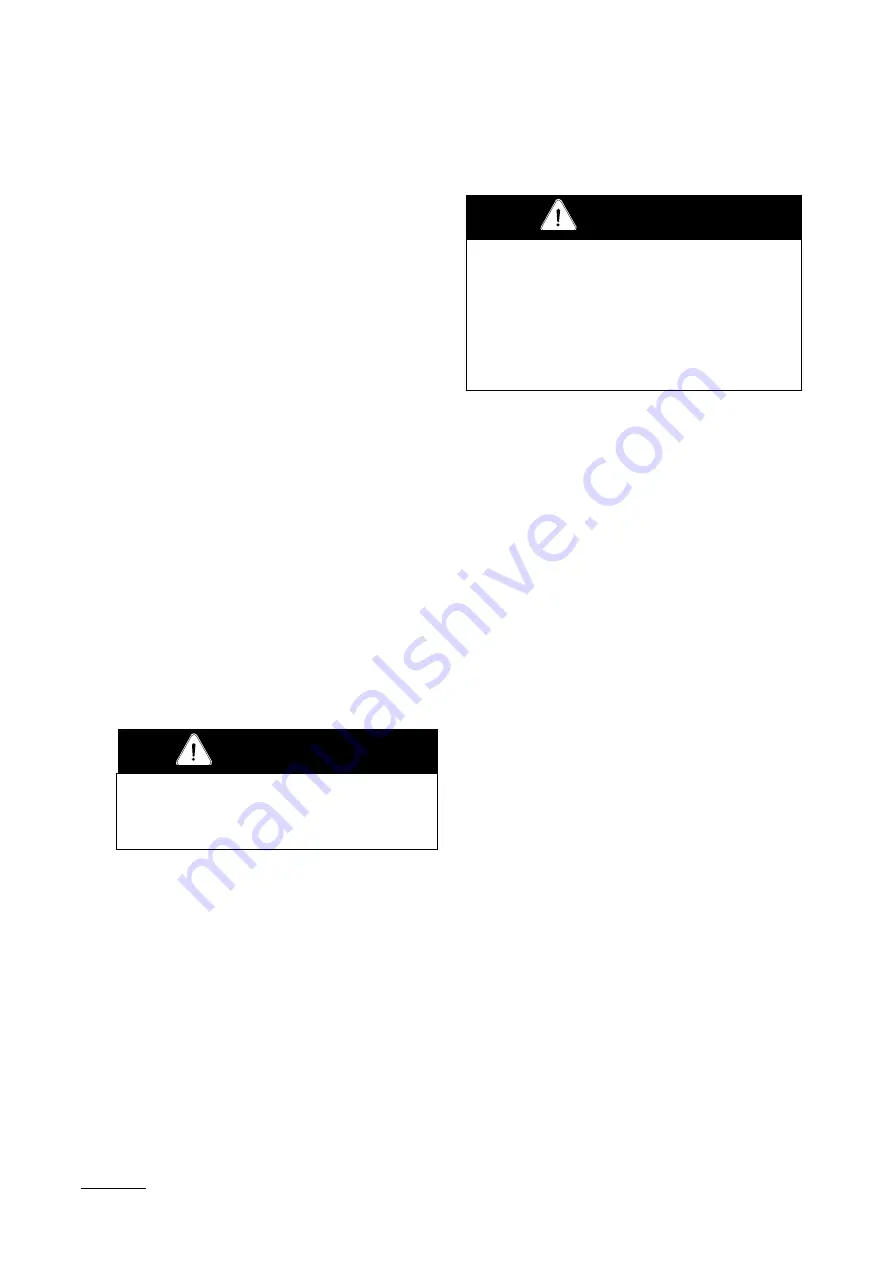
STARTING/STOPPING THE
ENGINE
1.
Ensure the parking brake is set, the PTO switch
is in OFF and the lift lever is in the TRANS-
PORT or FLOAT position (Fig. 9). Remove
your foot from the traction pedal and make sure
it is in neutral.
2.
Pull the choke (Fig. 9) to the full choke position
and move the throttle control (Fig. 9) to the
slow position.
3.
Turn the key in the ignition switch to START
(Fig. 9). Release the key immediately when the
engine starts and allow it to return to the RUN
position. Regulate the choke to keep the engine
running smoothly.
4.
When the engine is started for the first time, or
after an engine oil change or engine, transmis-
sion or axle overhaul, operate the machine in
forward and reverse for one to two minutes.
Also operate the lift lever and the PTO lever to
assure correct operation of all parts. Turn the
steering wheel to the left and right to check
power steering response. Then shut the engine
off and check fluid levels, check for oil leaks,
loose parts and any other malfunctions.
5.
To stop the engine, move the throttle control
backward to SLOW, move the PTO switch to
OFF and turn the ignition key to OFF. Remove
the key from the switch to prevent accidental
starting.
CHECKING THE INTERLOCK
SAFETY SYSTEM
The purpose of the safety interlock system is to pre-
vent the engine from cranking or starting unless the
traction pedal is in neutral and the PTO switch is in
the OFF position. Also, the engine will stop when
the PTO control is engaged or the traction pedal is
depressed with the operator off the seat.
1.
Move the PTO switch to OFF and remove your
foot from the traction pedal so it is fully
released.
2.
Turn the key to START. The engine should
crank. If the engine cranks, go to step 3. If the
engine does not crank, there may be a malfunc-
tion in the interlock system.
3.
Rise from the seat and engage the PTO switch
while the engine is running. The engine should
stop within 2 seconds. If the engine stops, the
switch is operating correctly; thus, go to step 4.
If the engine does not stop, there is a malfunc-
tion in the interlock system.
4.
Rise from the seat and depress the traction
pedal while the engine is running and the PTO
lever is disengaged. The engine should stop
within 2 seconds. If the engine stops, the switch
is operating correctly; thus, continue operation.
If the engine does not stop, there is a malfunc-
tion in the interlock system.
OPERATING
CHARACTERISTICS
Practice driving the GROUNDSMASTER
®
1000L
before initial operation because it has a hydrostatic
transmission and its characteristics are different than
some turf maintenance machines. Some points to
consider when operating the traction unit and cutting
unit are the transmission, engine speed, load on the
cutting blades, and the importance of the brakes.
To maintain enough power for the traction unit and
16
Operation
Shut the engine off and wait for all moving
parts to stop before checking for oil leaks,
loose parts or other malfunctions.
CAUTION
Do not disconnect the safety switches because
they are for the operator’s protection. Check
operation of the switches daily to be sure the
interlock system is operating correctly. If a
switch is malfunctioning, replace it before oper-
ating the machine. Replace the switches every
two years to be sure of maximum safety.
CAUTION
Summary of Contents for 30200-70001
Page 19: ...19 Maintenance Figure 16 Figure 17 Figure 18...
Page 30: ......
Page 31: ......
Page 32: ......