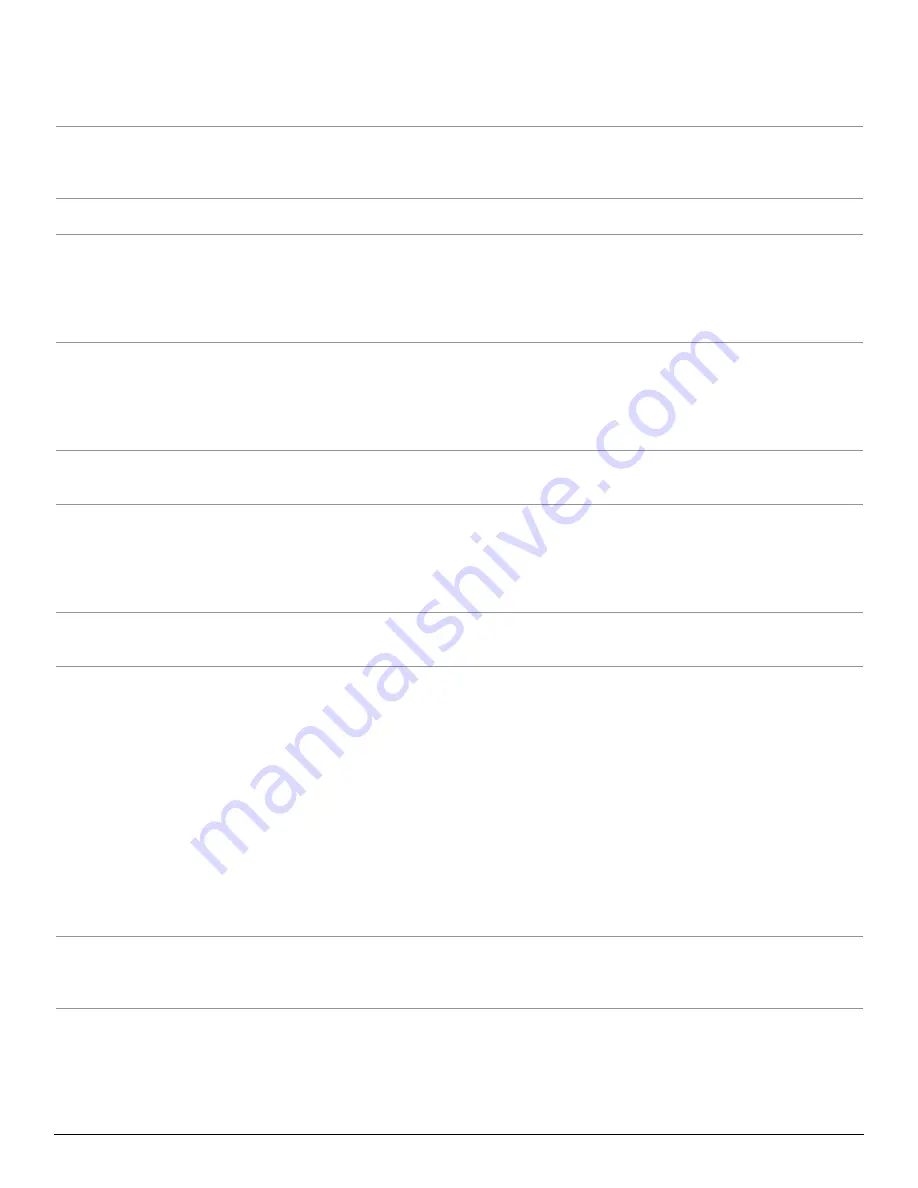
Trouble Shooting Guide
Vacuum and pump will not run
• Check that electrical cord is firmly seated in wall outlet.
• Check and reset building circuit breaker if tripped.
• Check main power switch.
Trips building circuit breaker
• Circuit is overloaded – move cord to a different wall outlet.
• If using an extension cord, make sure it is in good condition, less than
70 feet long and #10 gauge or heavier.
• Check pigtail plug, and extension cord for damage.
Vacuum won’t run
• Check vacuum switch, it should be in the “on” position.
• Check fuse inside.
Pump won’t run
• Check pump switch – it should be in the “on” position.
• Check pump circuit breaker (5 amp) and reset if tripped.
• Check fluid level – there must be enough water to float the low
water shut-off
• Lift the low water float. Pump should come on. If it doesn’t contact
Technical Service.
Pump tries to run and then trips circuit breaker
• Check pigtail and extension power cord for frayed, cut or worn spots.
• Check plugs and connectors.
• If using an additional extension cord, make sure it is in good condition,
less than 70 feet long and #10 gauge or heavier.
• Check pump static p.s.i. – must be 400 p.s.i. ± 10 p.s.i.
• Check wall outlet voltage. If below 105 volts, pump will not work.
Pump starts and stops
• Thoroughly clean main filter.
• Check fluid level – there must be enough water to float the low-water
shut-off.
Excessive pressure drop when cleaning
• Adjust static pressure to 400 p.s.i. when not cleaning.
(exceeds 100 p.s.i. drop)
• Check and clean main filter and ball strainers in tank.
• Check and replace worn spray nozzles and loose or leaking
fittings/inline strainer.
• Re-prime pump.
• Rebuild pump or pressure regulator, if necessary.
Water dripping from bottom
• Check machine for excess foaming. Add Defoam to tool hose
of machine exhaust
and tank. Open machine top cover and let vacuum run for 10 minutes
to dry out vacuum motor, then close lid and resume cleaning.
Poor recovery.
• Check tool head and hose for any obstructions.
• Check tool head - it must seat firmly on carpet in lowered position.
• Check clear lid cover sealing properly. Is lid gasket in good shape
with no cuts, cracks, or worn/compressed areas?
• Check drain hose and fittings for cracks and tears. Make sure drain
plug is securely fastened.
• Check wand hose for holes, cracks, or cuts.
• Check vacuum hose cuffs – it must seat firmly on inlet fitting and
tool head.
• Check carpet installation. Some carpets are installed on uneven
surfaces with ridges and bumps. It is difficult to get good drying times
with this type of installation.
• Check drain hose plug, it must be securely fastened to prevent air
leaks to vacuum causing vacuum flooding. Hose will vibrate if there is
an air leak.
Streaks on carpet or no fluid
• Check nozzles for full spray. Clean if clogged or replace if worn.
from tool head
• Check tool and hose for obstructions.
• Check and clean inline strainer filter.
• Check and clean main filter and ball filters.
Pump will not prime
• Attach priming hose assembly to quick disconnect on front of machine.
Place hose end in solution tank and run pump for 30 seconds.
• Remove priming hose assembly, attach main solution line and
check p.s.i.
• If above does not work, reattach priming hose. Seal priming hose end
in the vacuum hose inlet on front of machine. Run vacuum and pump
motors for 30 seconds to siphon solution into pump.