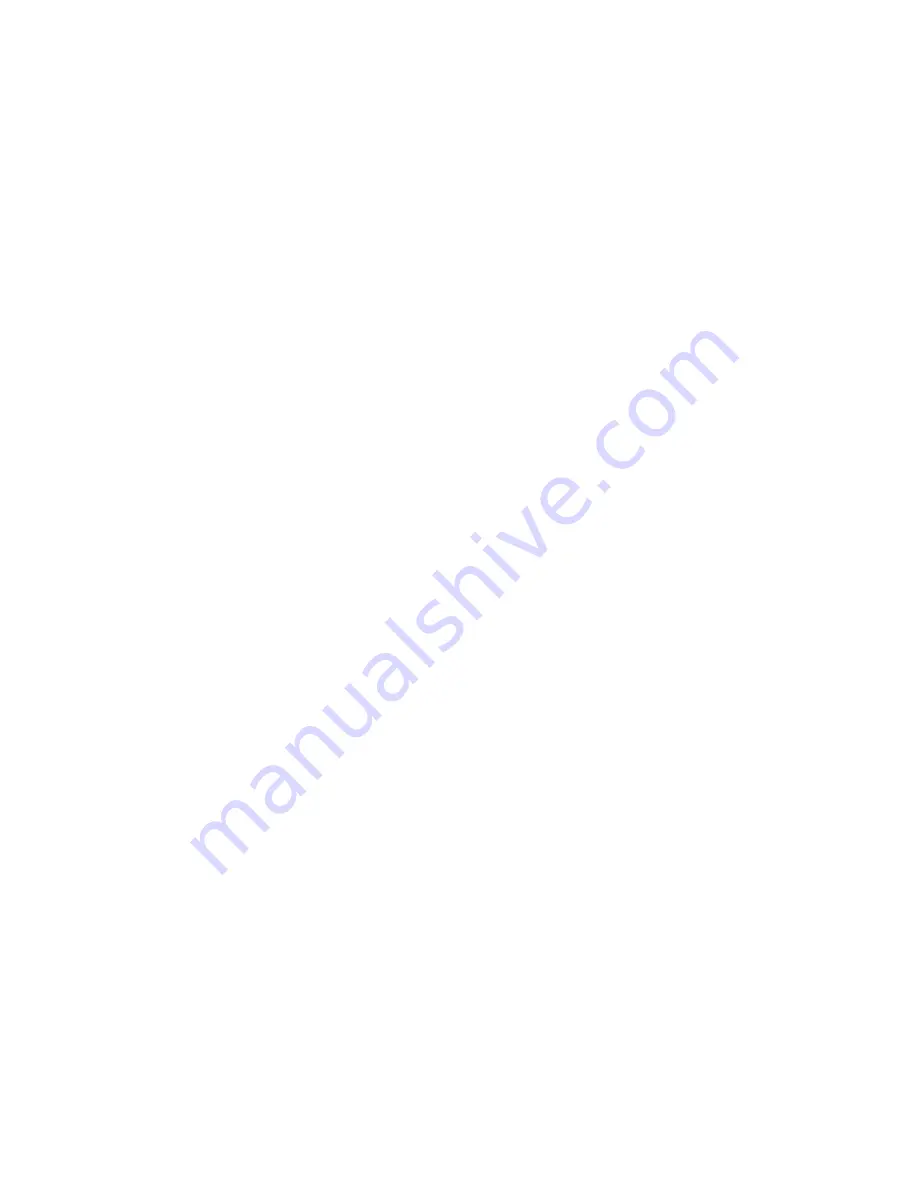
in the feed water sediment filter outlet manifold plumbing). Turning this lever to point to the side
opens the valve. This allows feed water to flow through the unit just at feed water pressure. To get
the maximum flushing conditions, close the re-circulation valve and open the brine valve. This flow
will flush the brine out of the membrane(s) and will produce a small product flow.
For systems with atmospheric tanks, the product will flow to the tank. For systems with pressure
tank storage, dump the pressure in the tank to zero so product flow can occur. Allow feed water to
flow for at least 20 minutes for the TV-6000, to 30 minutes for the TV-8000.
Close the feed water valve and allow the filter pressure to go to zero. Remove the sediment filter
housing and element. Dump the water and set the filter element aside to drain and dry. The sedi-
ment filter must be reinstalled for each subsequent flush.
Observe the product and brine water at the beginning of the flush operation. If either the product or
brine seem to be fouled, a more frequent flushing is indicated.
8.2 RESTART PROCEDURE
Perform a flush cycle as indicated above (with feed water sediment filter installed). Move the sole-
noid valve lever to the closed position. Turn the RO system on and adjust brine and re-circulation
valves to produce the original operating pressure and flow conditions.
9.0 PARTS, ACCESSORIES AND SPARES
Where the spares schedule is shown at the group heading, determine the component installed in
your RO unit. We recommend spares be available after the time indicated. Some components
scheduled for spares are for options, different voltages or 50 Hz units. Ensure the spares you
choose are applicable to your RO system. Feed water conditions may indicate more frequent
replacement, particularly for filtration and membranes.
SPARES
SCHEDULE
PUMPS
2 years
107454
TV-6000, 16 Stage 1.0 HP
107455
TV-8000, 14 Stage 1.0 HP
VESSELS
101216
Vessel Assy, 4”ODx40”L, SS, End Cap Clamp, FT Style
100083
O-Ring set
1 year
105270
Vessel Assy, 4”ODx40”L, PVC, Lock Ring, Side Ports, FT Style
105998
Plug
105999
Locking Ring
101113
O-ring Set
1 year
MEMBRANES
2 years
107712
membrane, 4040, TF, ESPA1, FT style, Low Energy
107787
membrane, 4040, TF, ESPA2, FT style, Low Energy
MONITORING AND CONTROL
105991
Microprocessor Control in Enclosure, Wiring Harness
102880
Feed Solenoid Valve, 3/4”, 220V
2 years
105818
Flush Solenoid Valve, 3/8”, 220V (Auto Flush System)
2 years
105285
Gauge, 100 psi, 2.5”, SS Case, Bronze Int., Glycerin Filled 2 years
23
Summary of Contents for TV-6000
Page 2: ...TOMAR TV 6000 SYSTEM ...
Page 7: ...Figure 1 Typical System Configuration TV 12K shown 5 ...
Page 13: ...Figure 2 System Plumbing Diagram 11 ...
Page 14: ...Figure 3 System Electrical Schematic Diagram ...
Page 20: ...Figure 4 PVC Vessel Membrane Assembly 18 ...
Page 21: ...Figure 5 Stainless Steel Vessel Membrane Assembly 19 ...
Page 28: ...25 NOTES ...
Page 31: ......