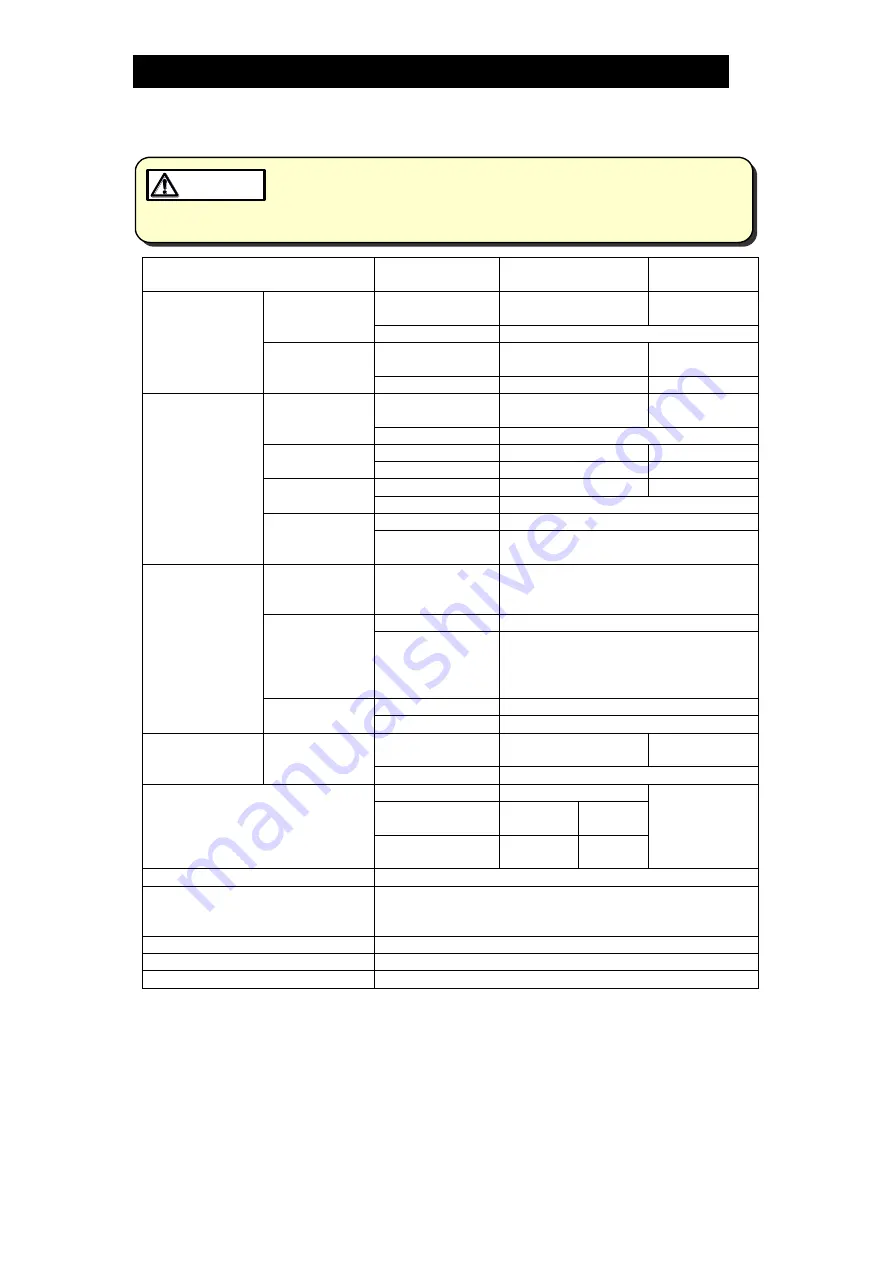
172-65608MA-03 (RGDS) 5 Oct 2021
5
System Specifications
Install properly and DO NOT use this system outside the recommended
operating pressure, temperature and other specification ranges.
Improper use may result in such hazards as damage to the system or
malfunctions which may lead to serious accidents. Local regulations
may restrict the use of this system to below the conditions quoted.
CAUTION
Item
Property
RGDS (Standard
Specification)
Ex-proof
Specification
Pressure
Reducing
Section
Steam Control
Valve
Model
CV10
1)
(Non Ex-proof)
CV10
1)
(Exd II BT5)
Size/Connection Depends on specifications
Pressure
Sensor
(With Siphon)
Model
MBS33M
1)
(Non Ex-proof)
KD43
1)
(Exd II BT4)
Size/Connection R 3/8
R 1/2
Desuperheating
Section
Temperature
Control Valve
Model
CV10
1)
(Non Ex-proof)
CV10
1)
(Exd II BT5)
Size/Connection Depends on specifications
Temperature
Sensor
Model
TR1-35S
1)
R1G
1)
(d2G4)
Connection
R 3/8
R 1/2
Strainer
Model
Y3
1)
Size/Connection Depends on specifications
Check Valve
Model
CKF3M
1)
Connection
Flangeless (wafer) type
Size depends on specifications
Water Mixing
and Separation
Section
Water
Injector,
Static Mixer
Size/Connection
50
– 200 mm (2 – 8 in): JIS 10K,
20K, 30K, ASME/JPI Class 150, 300
Condensate
Separator
Model
DC3
Size
50
– 150 mm (2 – 6 in)
(For 200 mm (8 in) water
injector/static mixer, 150 mm (6 in)
separators installed in parallel)
Steam Trap
Model
JS-X series, JH series
Size/Connection Depends on specifications
Pump Section
2)
Pump
Model
CRN
1)
(Non Ex-proof)
CRN
1)
(eG3, d2G4)
Size/Connection Depends on specifications
Control Panel
Power rating
200 V
Special order
Installation
Location
Indoor
Outdoor
Installation Type Wall-
mounted
Stand-
alone
Pressure Range
0 to 1.6 MPaG (0 to 250 psig)
Minimum Set Temperature
5
C (10
F) above saturated steam temperature
(Size 200 mm (8 in): 10
C (20
F) above saturated
steam temp.)
Steam Supply Temp. Stability
Within
1
C (1.8
F)
3)
Steam Velocity
5 to 50 m/s (20 to 160 ft/s)
Steam Discharge
200 to 30,000 kg/h (450 to 66,000 lb/h)
1)
Standard products when the components are supplied by TLV. The model type may differ
depends on the installation environment.
2)
This device is required when the pressure of the desuperheating water supplied to the
system is insufficient.
3)
This value depends on the status of the process as well as the PID setting and is only to be
used as a reference.
For details regarding components, refer to the individual specification data sheets (SDS).