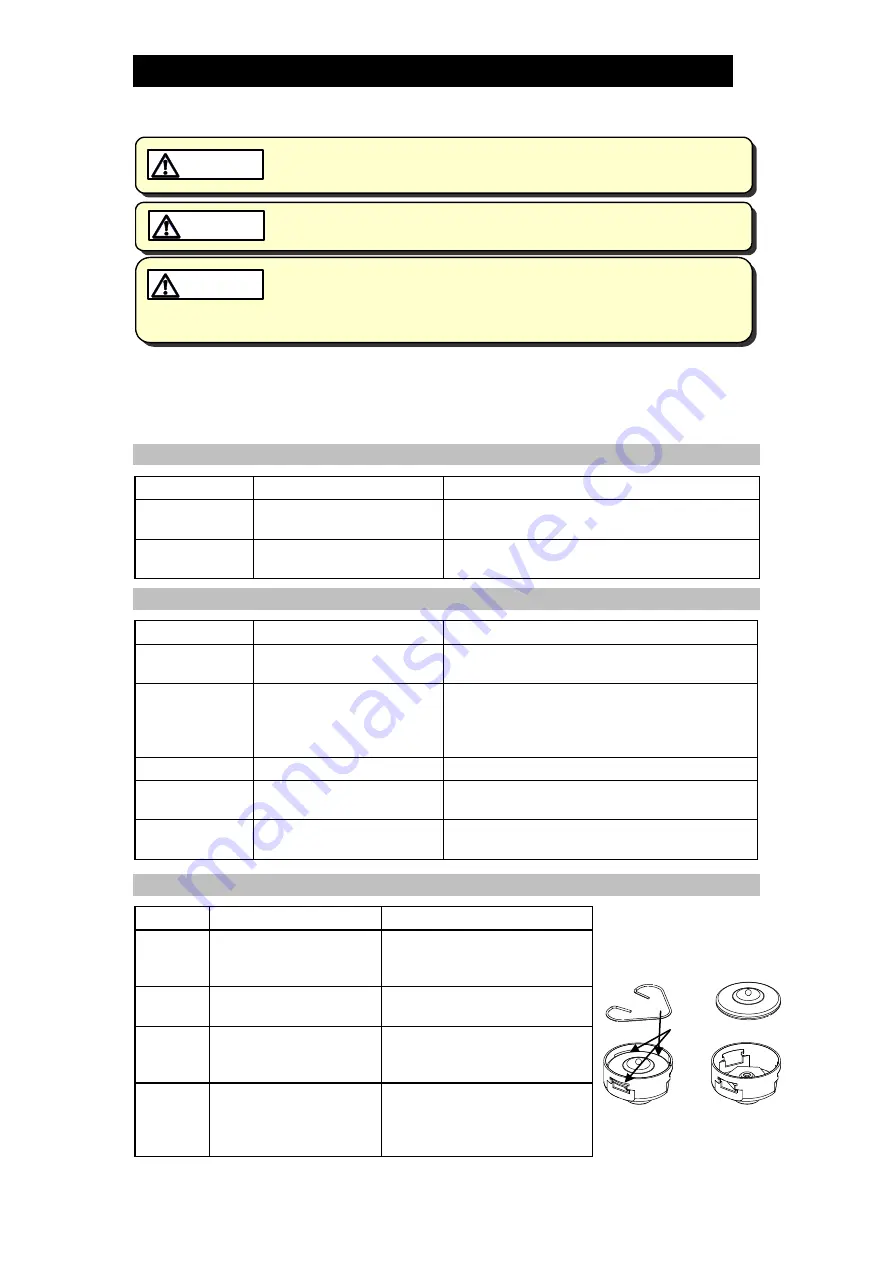
172-65451MA-04 (JH5RL-X) 3 Jul 2018
9
Disassembly/Reassembly
NEVER apply direct heat to the float. The float may explode due to
increased internal pressure, causing accidents leading to serious injury
or damage to property and equipment.
WARNING
Use hoisting equipment for heavy objects (weighing approximately
20 kg (44 lb) or more). Failure to do so may result in back strain or other
injury if the object should fall.
CAUTION
When disassembling or removing the product, wait until the internal
pressure equals atmospheric pressure and the surface of the product
has cooled to room temperature. Disassembling or removing the
product when it is hot or under pressure may lead to discharge of fluids,
causing burns, other injuries or damage.
CAUTION
Use the following procedures to remove components. Use the same procedures in
reverse to reassemble. (Installation, inspection, maintenance, repairs, disassembly,
adjustment and valve opening/closing should be carried out only by trained
maintenance personnel.)
Drain Plug (Option)
Part
During Disassembly
During Reassembly
Drain Plug
Remove with a socket
wrench
Consult the table of tightening torques and
tighten to the proper torque
Drain Plug
Gasket
Remove the gasket and
clean sealing surfaces
Replace with a new gasket; coat surfaces with
anti-seize
Detaching/Reattaching the Cover
Part
During Disassembly
During Reassembly
Cover Nut
Remove with a socket
wrench
Consult the table of tightening torques and
tighten to the proper torque
Cover
Remove by lifting up and
off
Make sure there are no pieces of the old
gasket left on the sealing surfaces of the
body and cover, align the arrows on the body
and cover and reattach
Connector
Remove the connector
Reinsert into the hole in the body
Connector
Gasket
Remove the gasket and
clean sealing surfaces
Replace with a new gasket
Cover Gasket
Remove the gasket and
clean sealing surfaces
Replace with a new gasket
Disassembly/Reassembly of Components Inside the Cover
Part
During Disassembly
During Reassembly
Spring
Clip
Pinch the insides
together and remove
from the X-element guide
Insert securely into the groove
in the guide (fig. A)
X-element Remove from the
X-element guide
Insert after making sure of the
correct orientation (fig. B)
Air Vent
Valve
Seat
Remove with a socket
wrench
Consult the table of tightening
torques and tighten to the
proper torque
X-element
Guide
Remove without
bending
Fix with the Air Vent Valve
Seat and make sure that the
X-element can be inserted
smoothly
Figure A Figure B
Groove