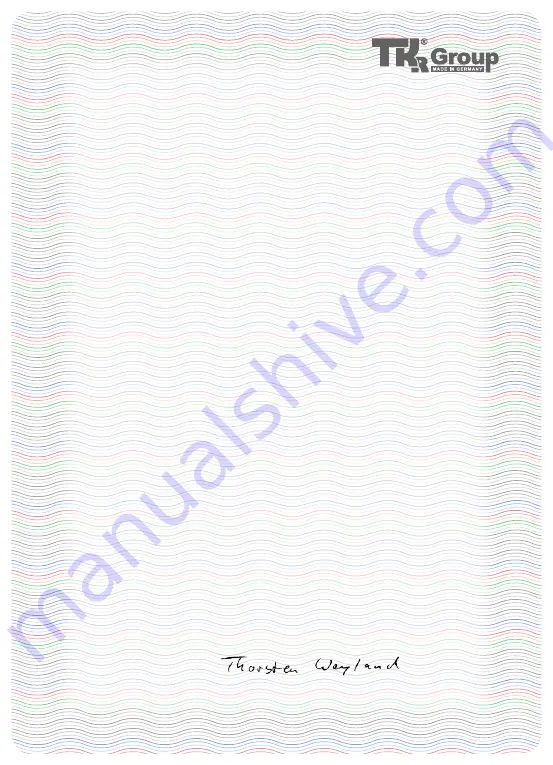
35
EC Declaration of Conformity
In accordance with EU Machinery Directive
2006/42/EC
Manufacturer:
TKR Spezialwerkzeuge GmbH
Am Waldesrand 9–11
58285 Gevelsberg, Germany
Contact:
Thorsten Weyland, Technical director
Technical documentation
Tool type:
Pneumatic/hydraulic stamping and riveting tool
Type designation:
PNP 90 SNW / RIV
Has been developed and designed in accordance
with the standards and guidelines specified
below by
TKR Spezialwerkzeuge GmbH
Am Waldesrand 9–11
58285 Gevelsberg (Germany)
Referenced
German Product safety law (ProdSG)
harmonised
EN 693; EN 11148-1; EN 11148-10; EN 792-13;
standards:
EN ISO 4413; EN ISO 4414; ISO 11200;
ISO 11202; EN ISO 12100
EU-Machinery Directive:
2006/42/EC
Statement of manufacturer:
The products specified herein comply with the
requirements of the referenced guidelines
and standards.
Gevelsberg, den 20.01.2017 Thorsten Weyland
Technical director
Summary of Contents for PNP 90 SNW-RIV
Page 31: ...31...