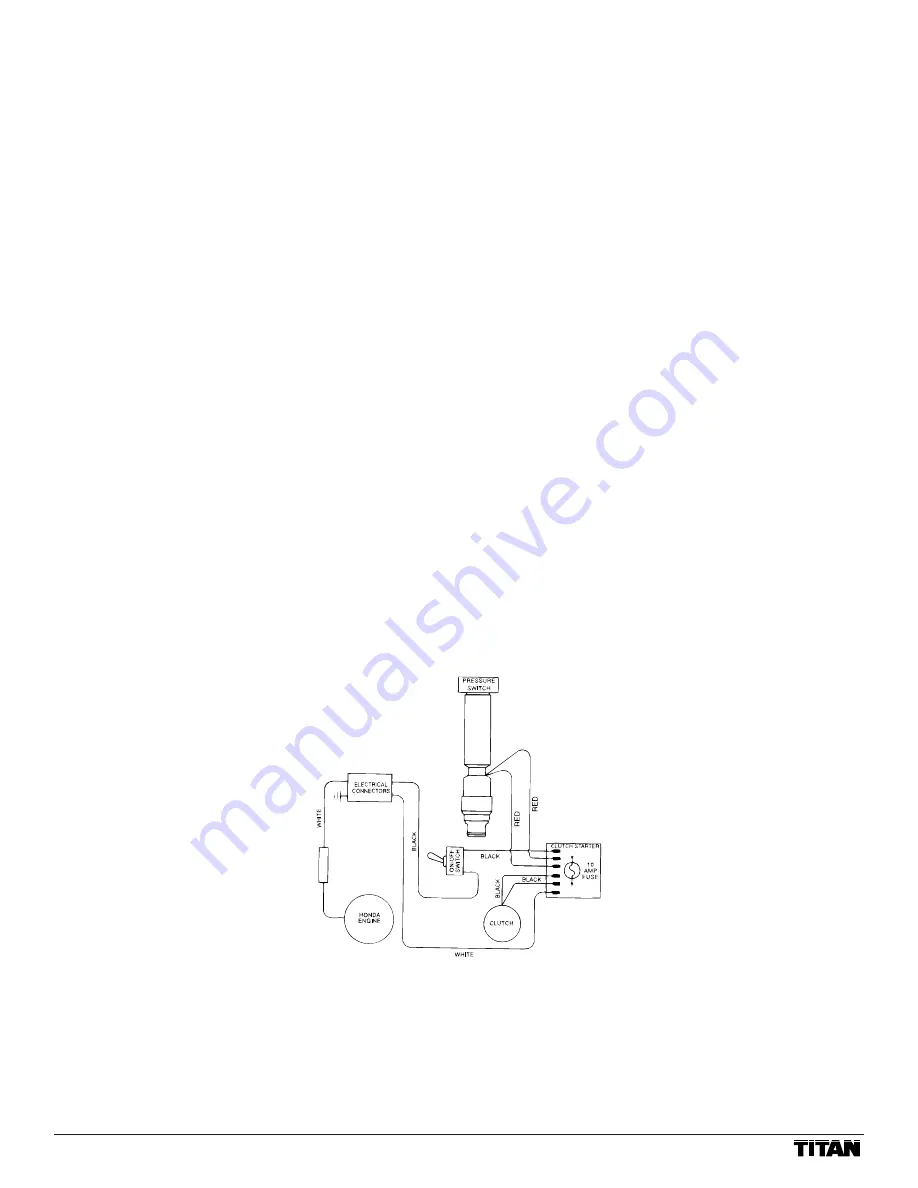
© Titan Tool Inc. All rights reserved.
21
Service / Replacement of the Clutch
Rotor
WARNING: Before proceeding, follow the Pressure Relief
Procedure outlined on Page 5. Additionally, follow all
other warnings to reduce the risk of an injection injury,
injury from moving parts or electric shock.
1. Remove (4) screws #54.
2. Remove Engine Assembly #12 (on pg. 18).
3. Remove (3) Screws #20.
4. Remove Clutch Rotor #21.
5. To install new Rotor, reverse procedures above.
Replacement of the On/Off Switch
WARNING: Before proceeding, follow the Pressure Relief
Procedure outlined on Page 5. Additionally, follow all
other warnings to reduce the risk of an injection injury,
injury from moving parts or electric shock.
1. Remove the Cover Plate and Insulator #60 & 66.
2. Disconnect the two black wires from the On/Off
Switch #62.
3. Remove the Rubber Boot and On/Off Plate #64 & 63
with a wrench.
4. Remove the On/Off Switch #62.
5. Install a new Switch and reattach the Plate and Rubber
Boot. Tighten securely.
6. Reconnect the two black wires to the On/Off Switch.
7. Reinstall the Cover Plate and Insulator with Warning
Label facing out.
Gear Repair / Service
WARNING: Before proceeding, follow the Pressure Relief
Procedure outlined on Page 5. Additionally, follow all
other warnings to reduce the risk of an injection injury,
injury from moving parts or electric shock.
1. Remove safety plate #70, from front of pump.
2. Remove front cover #41.
3. Remove (4) socket head screws #42 and slide pump
housing assembly #43 from gear box housing #53.
4. Inspect gears beginning with crank shaft assembly #45,
then output pinion gear #48.
5. Reassemble by reversing steps 1–4 above. When
reassembling, make sure that all washers are in place
and that gears and bearings are properly lubricated.
6. Remove Cover #41 and grease the Crankshaft located
within the Pump Housing #43 and the Crank Slide &
Connecting Rod #300 (on page 24) every 100 hours.
Replacement of Clutch Starter
WARNING: Before proceeding, follow the Pressure Relief
Procedure outlined on Page 5. Additionally, follow all
other warnings to reduce the risk of an injection injury,
injury from moving parts or electric shock.
1. Remove the Cover Plate and Insulator #60 & 66.
2. Disconnect the six wires that connect to the Clutch
Starter #58.
3. Remove the two screws #57.
4. Reassemble in reverse order. Refer to the Wiring
Diagram for the correct placement of the wires.
Gear Box Assembly Procedures
¤