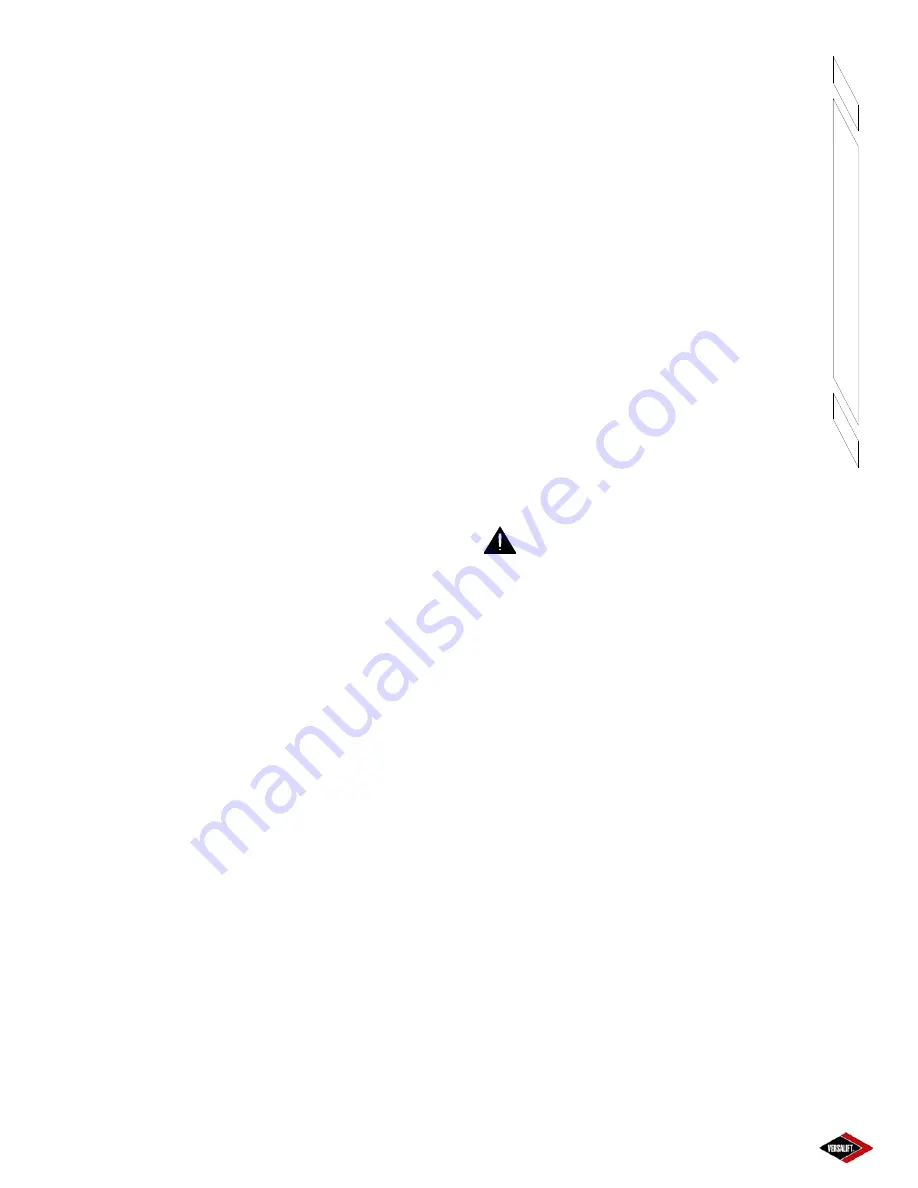
4-7
29084-05 03/17
VERSALIFT VST-7500-I
OPERA
TION
the toggle switch to the “ON” position and operate the
appropriate lift controls.
To deactivate the backup pump from the turret
,
push the toggle switch down (towards the “30
SECOND INTERMITTENT” message).
UPPER CONTROL OPERATION
This section describes the controls at the platform.
The standard, individual single stick control is
presented in this section.
Never allow an untrained individual to operate the aerial
lift. When operating the lift all lift movements must be
started and stopped gradually. Never operate the
upper controls without using the personnel restraint
system.
Before operating the aerial lift, the operator must be
familiar with the built-in compensation link system
that affects boom movements. The connecting
components are shown on the “Major Components”
drawing in Section 1 When the lower boom function
is activated the lower boom will respond as directed
and the upper boom will move and maintain its initial
position in relation to the turret. However, activating
the upper boom function will not affect the lower boom.
Speed and smoothness of lift operation are controlled
by feathering the control valves. Feathering a control
function allows the operator to change the speed by
adjusting how far the control is moved. Flow can be
directed to one function or multiple functions
simultaneously. Function speed depends on flow to
each valve. Regular practice will develop operator
proficiency.
UNITROL 3 OR 4-FUNCTION CONTROLS
- This
multi-jointed handle operates the valve spools and
enables the operator to control all lift movements.
Lift operations are selected by depressing the safety
trigger while actuating the single stick control handle.
Slowly move the single stick lever in the desired
direction until motion begins. Further movement of
the handle in the same direction will increase the
speed of the motion. To stop a lift movement, move
the single stick lever back to the neutral position and
release the trigger. Releasing the safety trigger in
any position except neutral will cause the selector
valve to slam shut and stop lift travel with an abrupt
jerking motion resulting in unnecessary loads and
stresses.
To operate two or more functions at the same time,
position the single stick handle anywhere in an area
between the separate paths of the desired functions.
EMERGENCY STOP (Standard)
- The primary
purpose of the emergency stop valve is to deactivate
all the upper controls in the event of a control valve
malfunction (i.e. a valve spool stuck in the open
position) or other hydraulic emergency. Push the
knob labeled “PUSH FOR EMGY. STOP”; then the
upper controls are inoperable and pressure at the tool
ports is relieved. When the emergency stop knob is
pulled up, the upper controls and tool power are
functional.
ENGINE START/STOP (Standard)
- The start/stop
system has been designed so that the engine cannot
be strarted unless the ignition switch is in the “RUN”
position and the master control switch is activated.
This feature makes it difficult for unauthorized
individuals to operate the lift when the truck is locked.
The engine start/stop system is operated by an air
cylinder at the upper controls.
DANGER
:
THE TRUCK TRANSMISSION
MUST BE IN NEUTRAL BEFORE USING THE
ENGINE START/STOP. STARTING THE TRUCK IN
GEAR WILL CAUSE MOVEMENT WHICH MAY
CAUSE DEATH OR SERIOUS INJURY TO THE
OPERATOR IN THE LIFT OR ANYONE IN THE PATH
OF THE TRUCK.
To start the truck engine from the upper controls
,
push the air cylinder plunger knob down and hold the
knob until the engine starts. If the truck starter does
not engage, release the plunger knob and allow the
plunger to rise to the neutral position. A second push
on the plunger may be required to get the latching
relay into position so the engine will start.
To stop the truck engine from the upper controls
,
push the air cylinder plunger knob down to get the
latching relay into the stop position.
HYDRAULIC PLATFORM LEVELING (Standard)
-
Platform leveling is achieved with a master and slave
cylinder arrangement. However, the hydraulic platform
control at the platform and turret can be used to adjust
platform leveling, tilt the platform for cleanout, or ease
the removal of an injured operator.
HYDRAULIC TOOL POWER (Standard)
- The
hydraulic tool power ports are mounted outside the
fiberglass guard that surrounds the upper controls.
Always relieve the pressure to the tool ports before
connecting or disconnecting the hydraulic tool hoses.
Summary of Contents for VERSALIFT VST-7500-I
Page 2: ......
Page 4: ......
Page 6: ......
Page 8: ...1 2 29084 05 03 17 VERSALIFT VST 7500 I INTRODUCTION Figure 1 1 Model VST 7500 I Nomenclature...
Page 11: ...2 3 29084 05 03 17 VERSALIFT VST 7500 I RESPONSIBILITIES SAFETY...
Page 12: ...2 4 RESPONSIBILITIES SAFETY 29084 05 03 17 VERSALIFT VST 7500 I...
Page 13: ...2 5 29084 05 03 17 VERSALIFT VST 7500 I RESPONSIBILITIES SAFETY...
Page 24: ...3 6 29084 05 03 17 VERSALIFT VST 7500 I SPECIFICATIONS...
Page 25: ...3 7 29084 05 03 17 VERSALIFT VST 7500 I SPECIFICATIONS...
Page 27: ...3 9 29084 05 03 17 VERSALIFT VST 7500 I SPECIFICATIONS...
Page 28: ......
Page 42: ......
Page 50: ...6 4 29084 05 03 17 VERSALIFT VST 7500 I DAILY VISUAL INSPECTION...
Page 51: ...6 5 29084 05 03 17 VERSALIFT VST 7500 I DAILY VISUAL INSPECTION...
Page 52: ...6 6 29084 05 03 17 VERSALIFT VST 7500 I DAILY VISUAL INSPECTION...