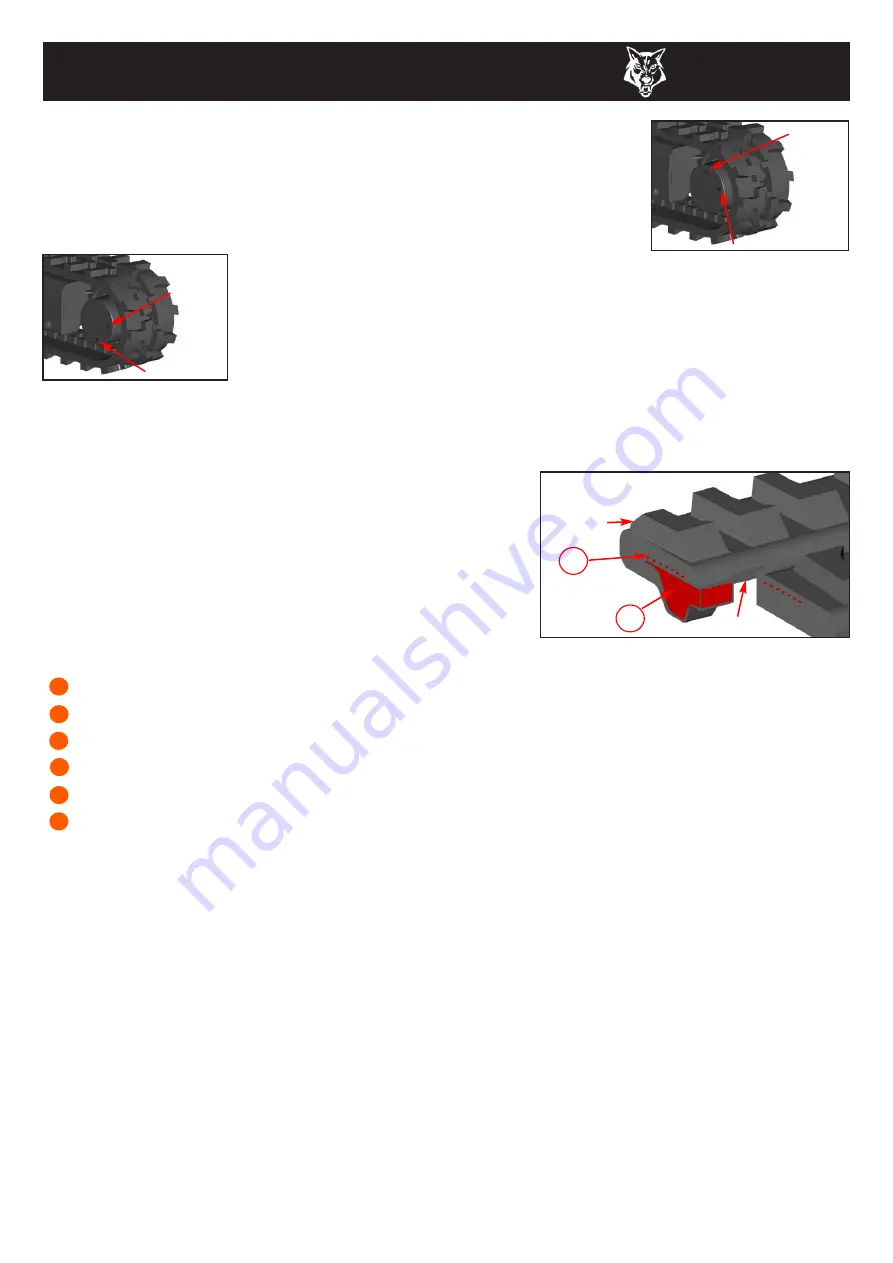
TIMBERWOLF
TW 150VTR
23
SERVICE INSTRUCTIONS
To drain the oil, track the machine until a plug is at 6 o’clock as shown.
Unscrew both plugs and allow oil to discharge into a suitable container.
Dispose of waste oil in a safe and approved way.
We recommend, for track drive gearboxes, using gear oils with E>P. additives and viscosity to SAE
80W/90 or ISO VG 150. Continuous duty temperature must not exceed 90
o
C.
The structure of the rubber track is shown in this diagram. The
steel cables (1) and metal core (2) are embedded in the
rubber.
There are many ways in which rubber tracks may be
damaged. Some of these are terminal for the tracks, others
are only cosmetic.
BREAKAGES OF STEEL CABLES AND METAL CORES.
Excess track tension can cause steel cables to break. Excess tension may be caused by;
Stones or foreign matter accumulating between the track and the undercarriage frame.
The track slipping off its guide system.
Extreme friction such as rapid changes in direction.
Improper contact between track and sprocket.
Operation on sandy terrain.
FATIGUE CRACKS AND ABRASION.
Cracks at the base of tile carved profiles are caused by rubber fatigue due to bending.
Cracks and bends on the edge of the rubber are caused by manoeuvring the track on concrete edges
and curbs.
Cracks and abrasions in the rubber on the guide roller paths are caused by compression fatigue of the
rubber due to the weight of the wheel combined with operation on sandy terrain or repeated sudden
changes in direction.
Abrasion of the carved profile may be caused, in particular, by rotation on concrete or gravel surfaces
or hard surfaces.
Cracks on the outside surface of the track are often due to contact with gravel, sharp stones and sharp
materials such as sheet metal, nails and glass.
Cracks on the inside surface of the circumference and on the edge of the rubber are caused by
contact between track and the undercarriage structure or with sharp concrete edges.
These methods of damage are progressive. The track can continue to be used until wear exposes the
metal cores. If this exposure extends for more than half of the circumference of the track then it is time
to replace the track, even though it can still be used.
SPROCKET HOLE
CARVED
PROFILE
1
2
To fill with oil, track the machine until the gearbox casing is level with a plug
positioned at 12 o’clock as shown. Unscrew the two plugs and fill from the
upper hole until oil reaches the level of the lower hole.
NOTE - Ensure the correct grade of oil is used: Gear Oil EP80W-90 GL5
OIL FILL
MAXIMUM LEVEL
DRAIN PORT
VENTING
REPLACE OIL IN THE TRACK DRIVE UNIT
DRAINING THE OIL IN THE TRACK DRIVE UNIT
REDUCTION UNIT OIL TYPES
CHECKING THE RUBBER TRACKS