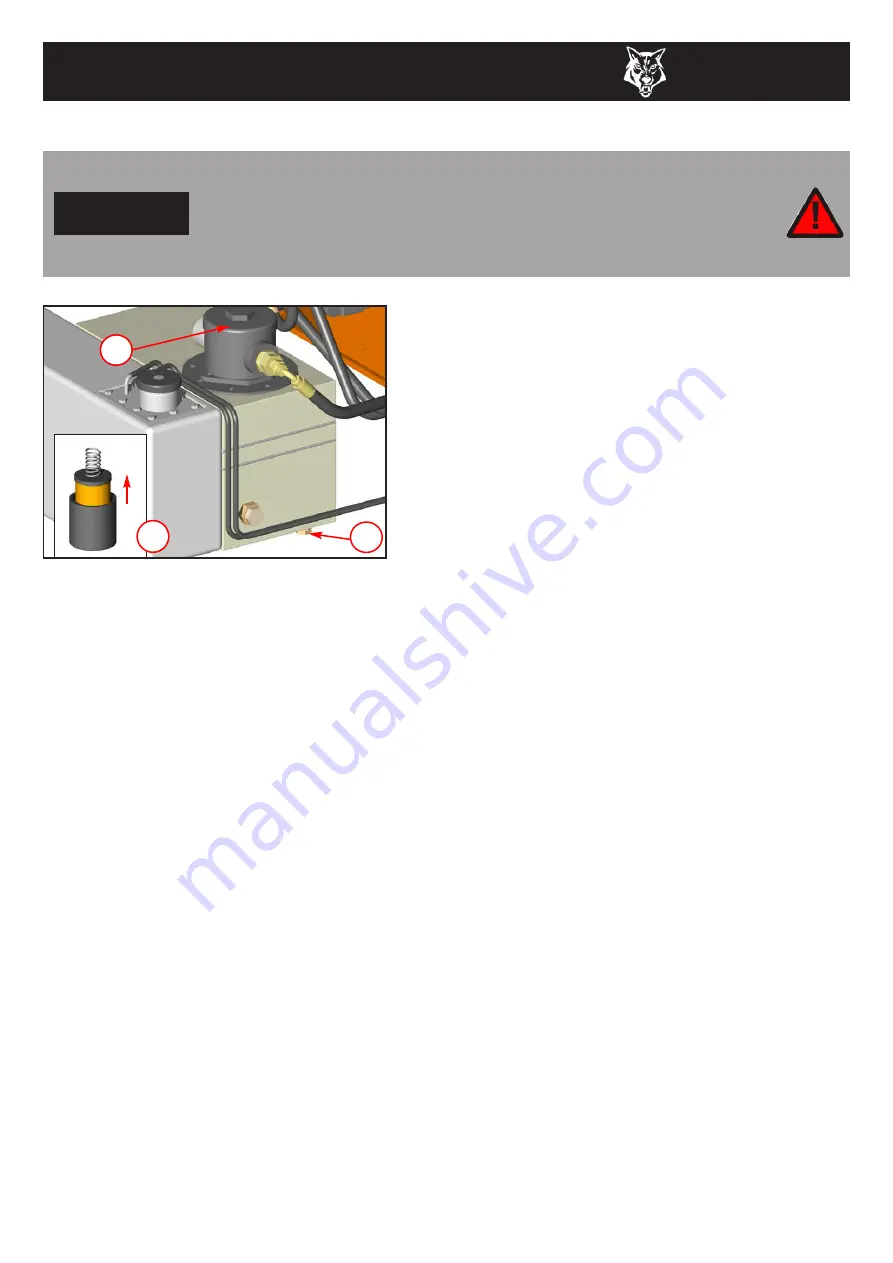
TIMBERWOLF
TW 150VTR
19
SERVICE INSTRUCTIONS
All the hydraulic hoses should be regularly inspected for chafing and leaks. The hydraulic system is
pressurized to over 150 Bar (2175 PSI) and thus the equipment containing it must be kept in good condition.
Identify the hoses that run to the top motor. These have the highest chance of damage as they are
constantly moving. If any hydraulic components are changed new seals should be installed during
reassembly. Fittings should then be retightened.
CHECK HOSES
1. Remove the black screw cap from the top of the
filter housing.
2. Partially remove filter element from inner cup. Leave
filter to drain for 15 minutes.
3. Remove filter element from cup when clear of hydraulic oil.
4. Remove drain plug and drain oil into a suitable container.
5. Replace drain plug.
6. Refill with VG 32 hydraulic oil until the level is between
the min and max lines on the tank (about 15 litres).
7. Refit the filter cup, install a new filter element and refit
the black screw cap, to the filter housing, ensuring
o-ring remains in place.
2
1
4
NOTE: This is a non-adjustable
air breather filter.
CHANGE HYDRAULIC OIL AND FILTER
WARNING
Use plastic gloves to keep oil off skin and dispose of the used oil
and filter in an ecologically sound way. The oil and filter should be
changed once a year or at any time it becomes contaminated.
Before starting check that the chipper is standing level and brush
away loose chips.
Size
Pitch
Head
Torque Ibft Torque Nm
Blade Bolts
M10
Standard
T50 Torx
45
61
Hyd Motor Retaining Bolts
M10
Standard
17mm Hex
34
46
Funnel Retaining Nuts
M12
Standard
17mm Hex
38
51
General
M8
Standard
13 mm Hex
17
23
General
M10
Standard
17 mm Hex
34
46
General
M12
Standard
19 mm Hex
60
80
Drain Bung in Fuel Tank 3/8” BSP
-
22 mm Hex
25
33.8
CHECK FITTINGS
The Timberwolf TW 150VTR is subject to large vibrations during the normal course of operation.
Consequently there is always a possibility that nuts and bolts will work themselves loose. It is
important that periodic checks are made to ensure the security of all fasteners. Fasteners should be
tightened using a torque wrench to the required torque (see below).
Uncalibrated torque wrenches
can be inaccurate by as much as 25%. It is therefore essential that a calibrated torque wrench
is used to achieve the tightening torques listed below.