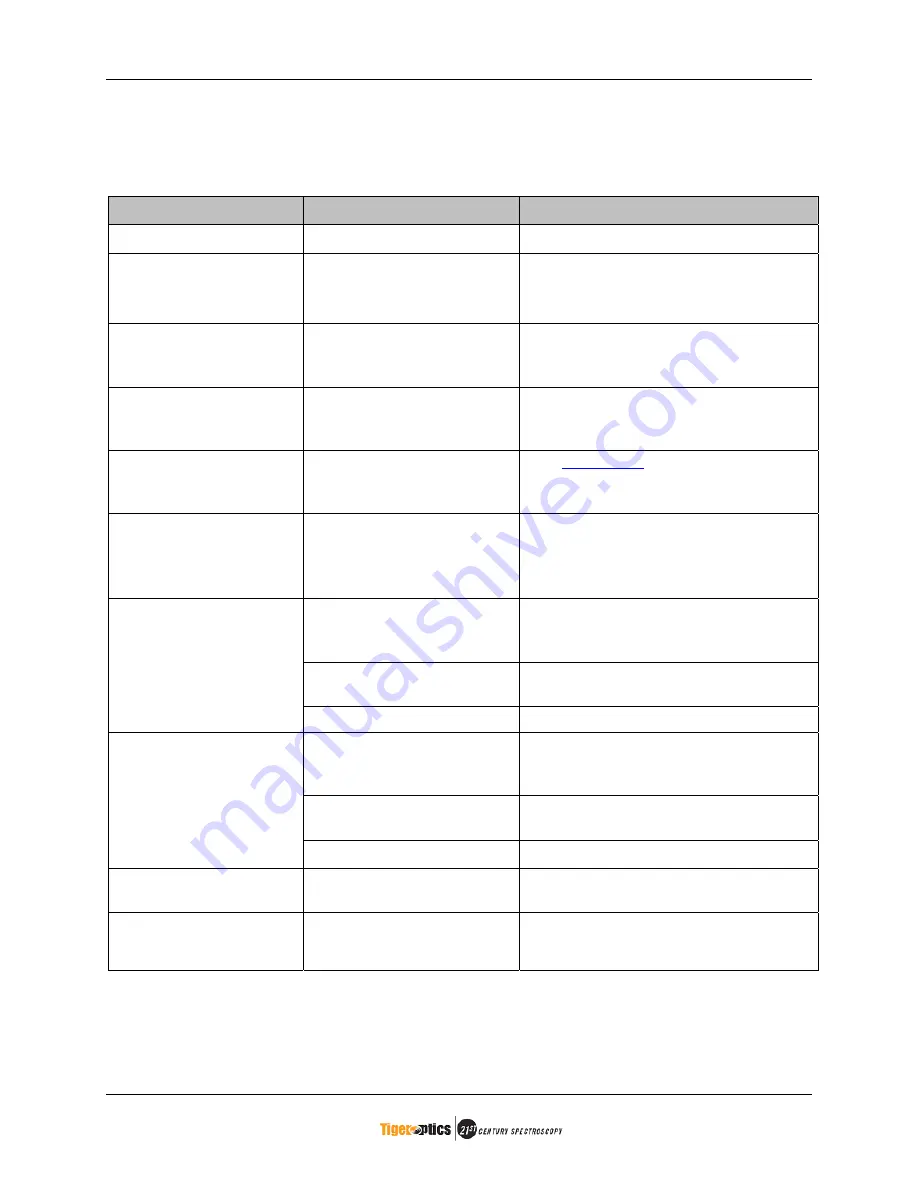
HALO Users Manual
Revision G
44
7.3 Troubleshooting Guide
Table 7-1 contains a troubleshooting guide of the most common problems associated with the
unit’s operation. System Fault alarms are included in the Table. If none of these step helps to
resolve the problem, contact trained Tiger Optics service personnel immediately.
Table 7-1 Troubleshooting
Circumstance
Probable Cause
Corrective Action
No display
Unit not powered up
Check fuse and plug.
Reading higher than
expected
Dead-legs, leaks, or
moisture traps in the
sampling system
Follow the “Preparing the Sample
Line” and “Leak Check” procedures.
Slow response time
Dead-legs, leaks, or
moisture traps in the
sampling system
Follow the “Preparing the Sample
Line” and “Leak Check” procedures.
Reading continues to
decrease
Reading not yet stable
Purge with dry gas then reapply the
sample. Repeat as often as required
until the reading stabilizes.
Not reading correct
concentration of a span
gas
Incorrect gas type chosen. See
Section 4.2
Reading is erratic
Contaminated optics
Consult with factory.
Fine air leaks in sample
line
Leak test the sample line and
connections following the procedure in
Table 3-3.
Fine air leaks in sample
cavity
Leak test following the procedure in
Table 3-3.
Reading is noisy
Optics need re-alignment
Consult with factory.
Above the maximum ring-
down value, too much
water.
Stop and purge the unit with a dry gas
until on scale.
Optical bench out of
alignment
Consult with factory.
Ring-down Alarm
Detector failure
Consult with factory.
Ring-down Fault and
Laser Current Fault
Laser is not operating
Check that there is current. If not,
consult factory.
Ring-down Fault and
Laser Temperature
Fault
Temperature controller has
failed
Consult with factory.