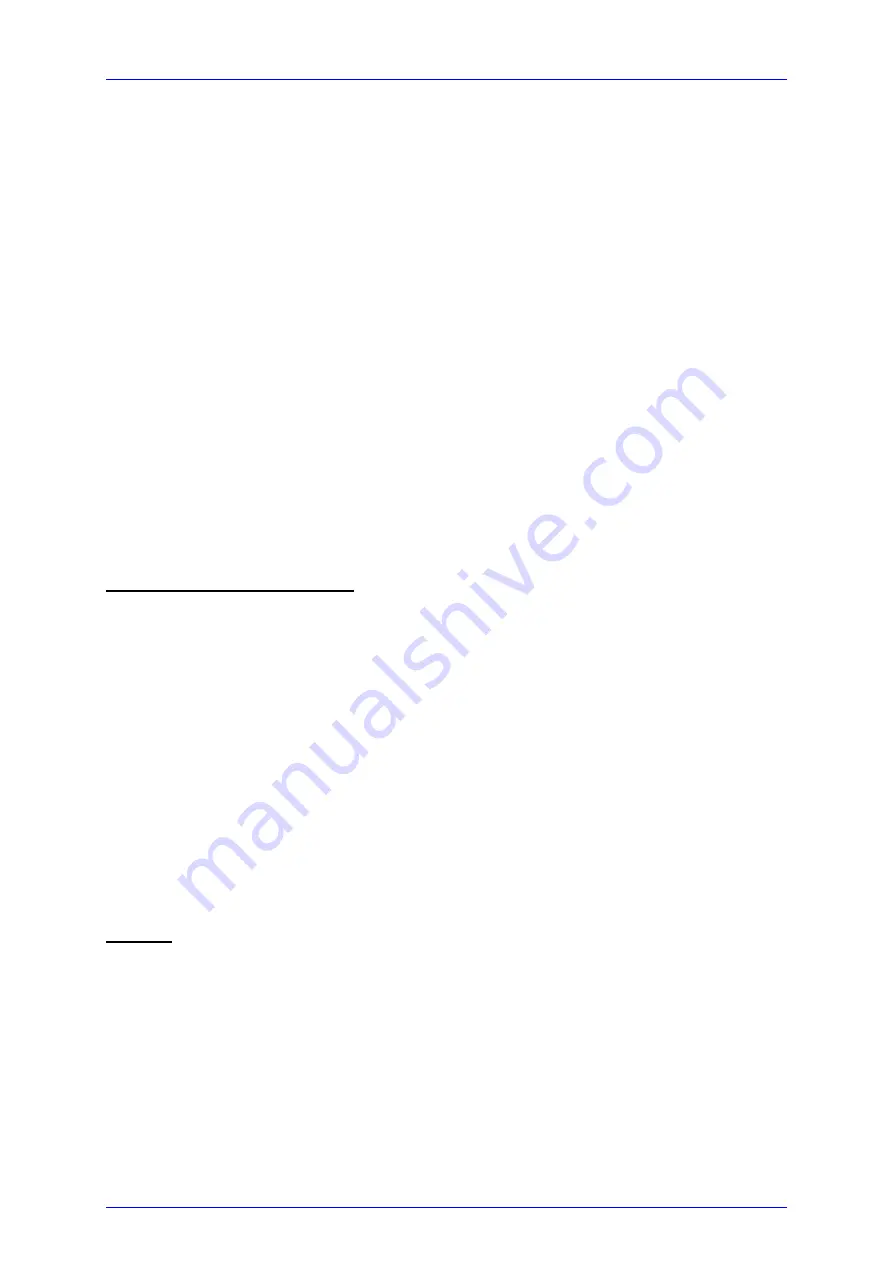
2.2 Optimization of temperature control loops
TED350 / page 26
To 3. The transient response by setting a new temperature is limited since the heat
transport in the copper bloc is relatively slow. Furthermore the temperature
slope in the copper must form anew. The sensor (which also possesses a
significant heat capacity) must settle to the laser temperature.
Possibility of optimization: PID adjustment
2.2.2 PID adjustment
Temperature control loops are comparatively slow control loops with control
oscillations in the Hertz range.
PID adjustment optimizes the dynamic behavior. With the TED350 the three
parameters P, I and D can be selected independently.
Example of a PID adjustment
(Preconditions: All limit values, all polarities have been set correctly, a suitable
sensor is connected and selected, the ambient temperature is about 20 °C)
1.
Set the P- and D-share to 0 (7 o'clock)
2.
Switch off the I-share (SW6 of the DIP switch on the rear).
(Refer to chapter 2.1.9, "Wakeup setting DIP switch" starting on page 22)
3.
Switch on the output (button TEC ON) and observe the actual temperature.
P-share
4.
Change repeatedly between set temperatures of about 18 °C and 22 °C while
observing the settling behavior of the actual temperature.
Increase the P-share gradually by turning the corresponding potentiometer
clockwise.
Higher values increase the settling speed but the same time the stability
reserve is decreased so that number and amplitude of overshoots increases.