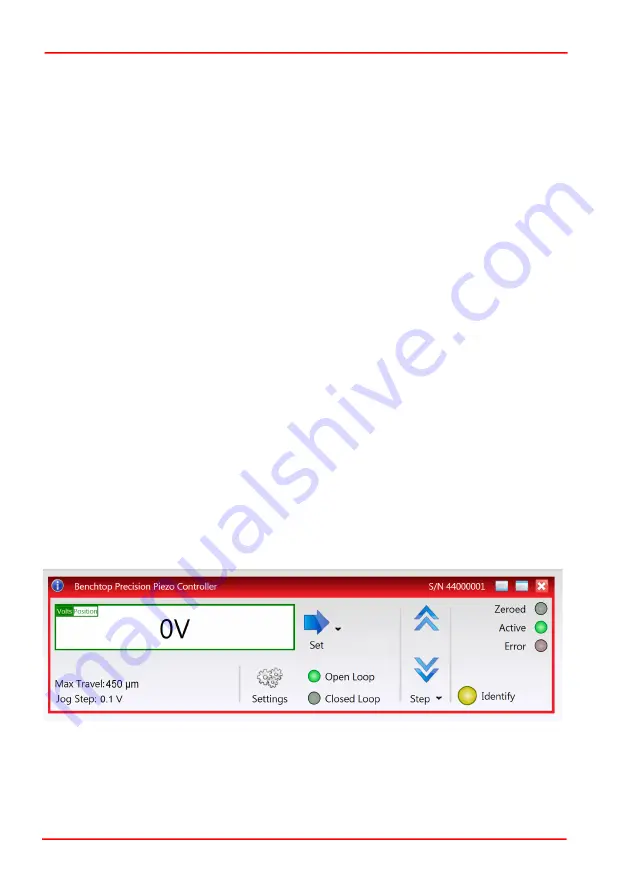
Page 3
ETN018233-D03
PFM450E Piezo Focus Mount and Controller
1.2 Software Overview
1.2.1 Introduction
The PPC001 piezo controller features USB connectivity (allowing multiple units to be
used together on a single PC), fully featured Graphical User Interface (GUI) panels,
and extensive software function libraries for custom application development.
The Kinesis software suite provides a flexible and powerful PC based control system
both for users of the equipment, and software programmers aiming to automate its
operation.
The User Interface allows full control of all settings and operating modes enabling
complete ‘out-of-box’ operation without the need to develop any further custom
software. It provides all of the necessary system software services such as generation
of GUI panels, communications handling for multiple USB units, and logging of all
system activity to assist in hardware trouble shooting. The Kinesis server is also used
by software developers to allow the creation of advanced automated positioning
applications very rapidly and with great ease. The server is described in more detail
in the following section.
1.2.2 Kinesis Server
With the Kinesis system, .Net Controls are deployed to allow direct control over (and
also reflect the status of) the range of electronic controller units, including the Piezo
controller. Software applications that use .Net Controls are often referred to as 'client
applications'. A .Net Control is a language independent software component.
Consequently the controls can be incorporated into a wide range of software
development environments for use by client application developers. Development
environments supported include Visual Basic, Labview, Visual C++, C++ Builder,
HPVEE, Matlab, VB.NET, C#.NET and, via VBA, Microsoft Office applications such as
Excel and Word.
Consider the control supplied for the PPC001 controller.
The system provides a separate control for each piezo drive channel to allow the
piezo unit to be manually operated, as well as a complete set of software functions to
allow all parameters to be set and operations to be automated by a client application.
The instrument panel reflects the current operating state of the driver unit to which it
is associated (e.g. such as piezo drive voltage). Updates to the panel take place
automatically when a user (client) application is making software calls into the same