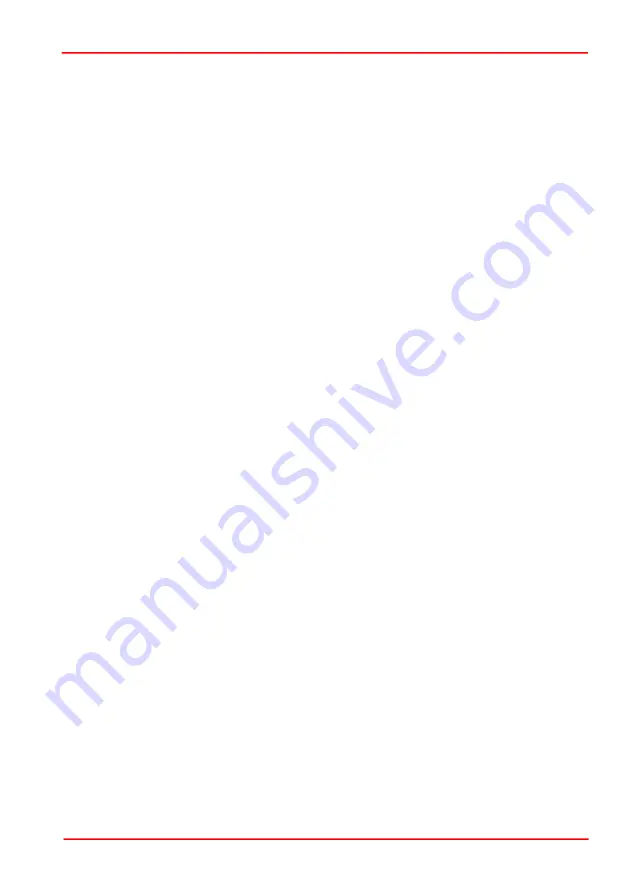
Rev F Dec 2018
Page 2
Chapter 1 Overview
The APT piezo unit operation is fully configurable (parameterized) with key settings
exposed through the associated graphical interface panel. Open or closed loop
operating modes can be selected 'on the fly', and in both modes the display can be
changed to show drive voltage or position (in microns). In the closed loop operation
mode, both the P & I (proportional and integral) components of the feedback control
loop can be altered to adjust the servoloop response. For convenience and ease of
use, adjustment of many key parameters is possible through direct interaction with the
graphical panel. For example, the output drive voltage or position can be adjusted by
rotating a "software-panel" control knob (see the tutorial in Chapter 4 for further
details). Note that all such settings and parameters are also accessible through the
ActiveX programmable interfaces which allow the user to build automated alignment
routines. See Section 1.2. for a full description of the APT system software and
background on the advantages of the ActiveX Control technology.
The key innovation of the APT range of controllers and associated mechanical
products is the ease and speed with which complete automated alignment systems
can be engineered at both the hardware and software level. All controllers in the APT
range are equipped with USB connectivity. The 'multi-drop' USB bus allows multiple
APT units to be connected to a single controller PC using commerical USB hubs and
cables. When planning an alignment application, simply add up the number and type
of drive channels required and connect together the associated number of APT
controllers. In the remainder of this handbook, the Tutorial section (Chapter 4)
provides a good initial understanding on using the unit, and the reference section
(Chapter 5) covers all operating modes and parameters in detail.