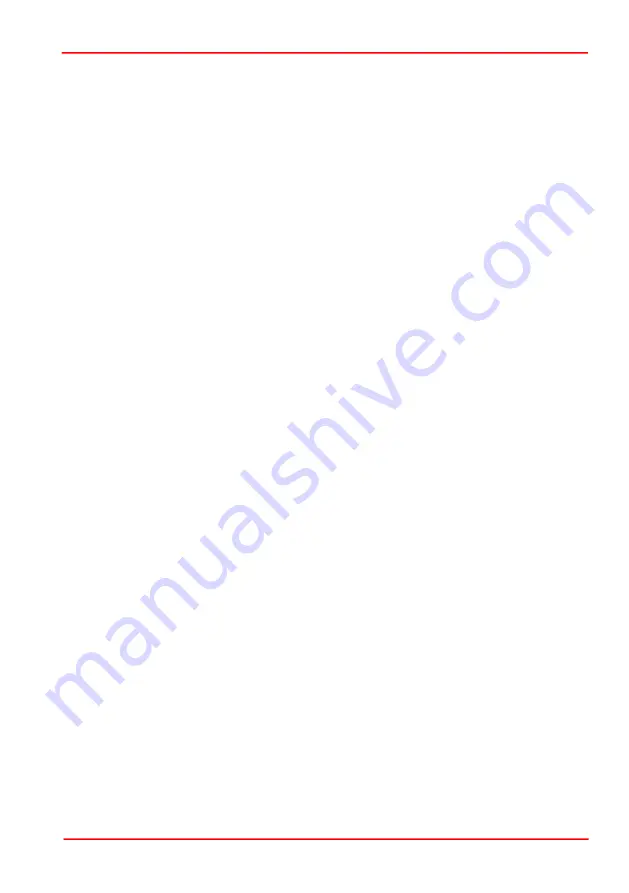
Rev F Dec 2018
Page 0
Chaper 4 PC Operation - Tutorial ...........................................................................19
4.1 Introduction ...................................................................................... 19
4.2 Using the APT User Utility ............................................................... 19
4.3 Setting the Position Sensor Zero .................................................... 21
4.4 Moving the Piezo .............................................................................. 22
4.4.1 Entering the piezo position ................................................................... 22
4.4.2 Moving the Piezo using the ‘Output’ control ......................................... 22
4.4.3 Jogging the Piezos ............................................................................... 23
4.5 Using the Controller as a Piezo Amplifier ...................................... 24
4.6 Thermal Shutdown ...........................................................................24
4.7 Using the Controller with a Force Sensor ...................................... 25
4.8 Using the MZF001 Joystick ............................................................. 26
4.9 Load Response ................................................................................. 28
4.10 Creating a Simulated Configuration Using APT Config ............... 29
Chaper 5 Software Reference .................................................................................. 32
5.1 GUI Panel .......................................................................................... 32
5.2 Settings Panel ................................................................................... 33
5.2.1 General tab. .......................................................................................... 34
5.2.2 Output tab. ............................................................................................ 35
5.2.3 Force Sensing tab ................................................................................ 36
5.2.4 Setting the Position Sensor Zero .......................................................... 36
5.2.5 Choice of Display Mode ........................................................................ 36
5.2.6 Detection of Range of Travel ................................................................ 37
Appendices
Appendix A Rear Panel Connector Pinout Detail ...................................... 38
Appendix B Preventive Maintenance ......................................................... 41
Appendix C Specifications........................................................................... 44
Appendix D Piezo Control Method Summary............................................. 47
Appendix E Regulatory ............................................................................... 53
Appendix F Thorlabs Worldwide Contacts ................................................ 55