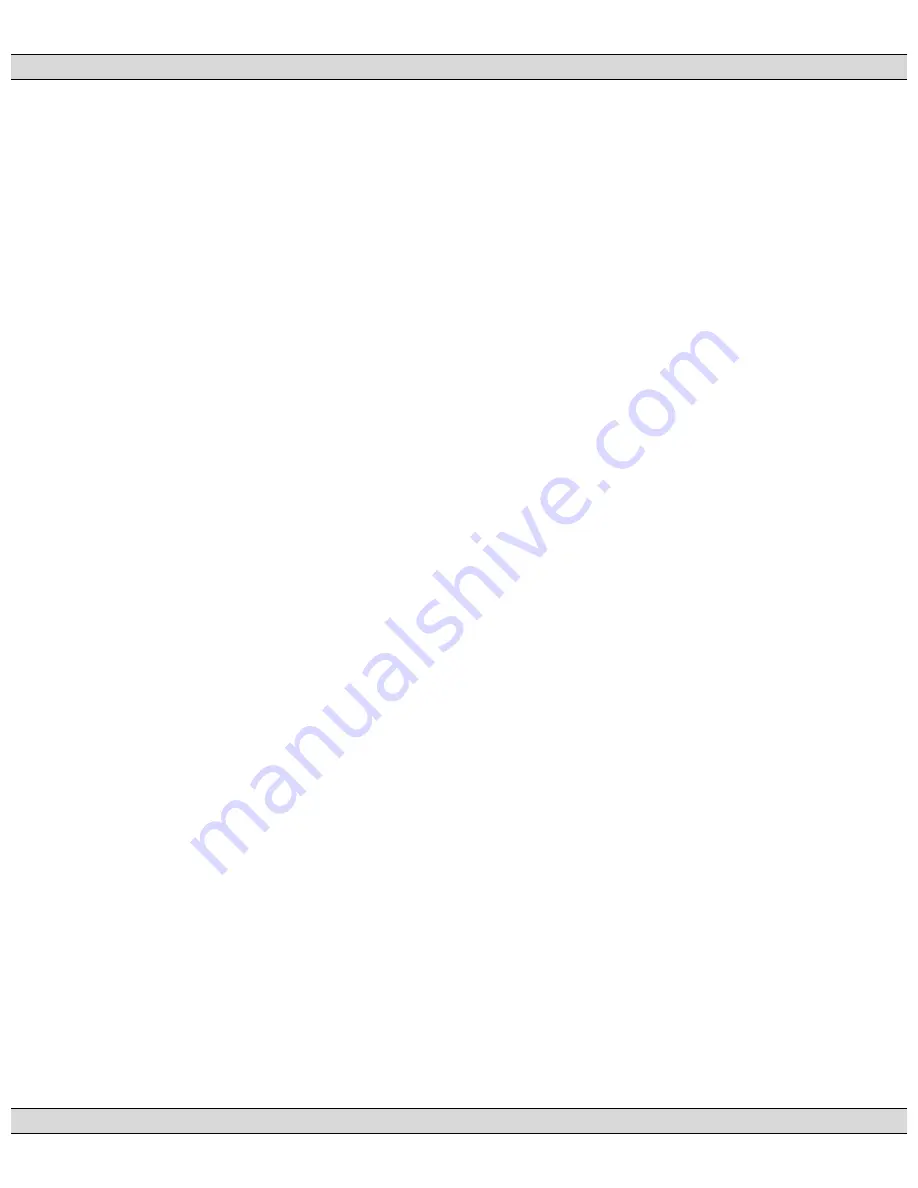
MEC 20 MICROPROCESSOR ENGINE/GENERATOR CONTROLLER
PM047 Rev 13 05/03/30
62
Thomson Technology
10.3.16. COOLDOWN TIME
Set to desired cooldown time in seconds. Up to 9999 seconds of cooldown time
may be programmed. Set to zero if not required.
Note:
If the controller is used
in an AMF application it is recommended to set the cooldown timer to a minimum
of 10 seconds to allow the generator to transfer Off Load before enabling the
cooldown time. (Ensures the load is transferred off of generator prior to stopping
the engine.)
10.3.17. NOMINAL ENGINE RPM
Set to the nominal engine speed in revolutions per minute (RPM).
10.3.18. FLYWHEEL TEETH
Set to the number
of ring gear teeth on the engine flywheel. The magnetic pick-
up must be installed to sense the same teeth for speed sensing as programmed.
10.3.19. CRANK DISCONNECT SPEED
Set crank disconnect speed in percentage of nominal speed, i.e. 30% or 540
RPM on a 1800 RPM engine.
10.3.20. OVERSPEED
Set overspeed shutdown point in percentage of nominal speed (i.e. 110% or
1980 RPM on a 1800 RPM engine).
10.3.21. OVERSPEED TRANSIENT DELAY
Select desired overspeed transient delay time in seconds. Time setting may be
entered in tenths of seconds.
10.3.22. RUN OUTPUT FAIL-SAFE
When enabled, this feature will inhibit the run output until the controller receives a
speed sensing signal, thus preventing possible damage from starting the engine
with no speed sensing for crank disconnect and overspeed. If selected, ensure
that the speed signal is not less than 3.0Vac from the magnetic pick up while the
engine is cranking.
Note:
If this feature is disabled, no overspeed protection or
crank disconnect will be provided if the speed signal fails. Should the user elect
to disable this feature Thomson Techology strongly recommends that backup
crank disconnect protection and additional overspeed protection is utilized.
Summary of Contents for MEC 20
Page 2: ......
Page 6: ...MEC 20 MICROPROCESSOR ENGINE GENERATOR CONTROLLER...