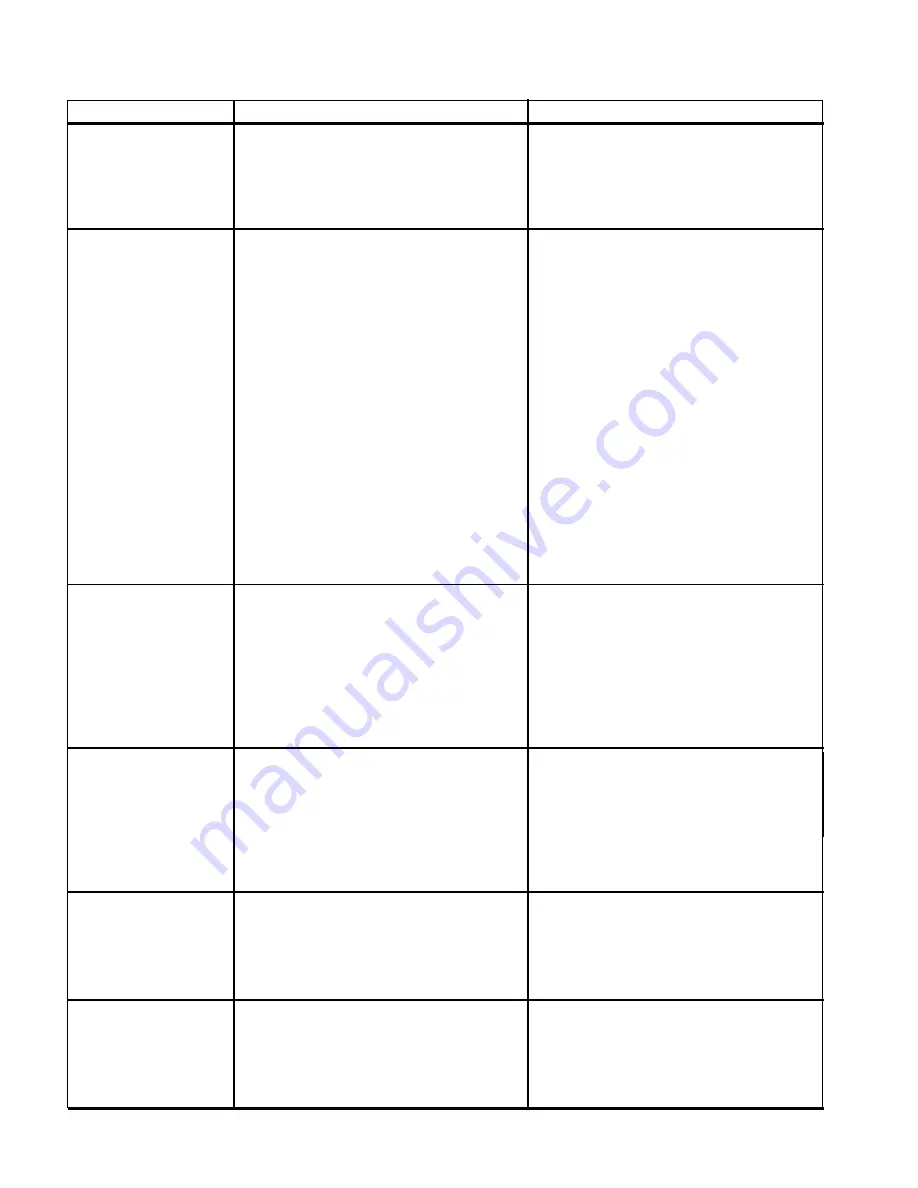
33
V
alue
S
erieS
V-710DM M
anual
Feed belts are
operating, but ma-
terial not feeding
(continued)
Problem
Cause
Solution
5. Gate assembly may be down too tight.
6. Too much weight in hopper.
1. Excessive weight in hopper.
2. Excessive down pressure on gate as-
sembly.
3. Off-centered product from center point
of machine.
4. Stack is bearing down on edge of belt.
5. Belt wear.
6. Rollers out of adjustment.
1. Improperly adjustment in one or more
of the following:
• gate assembly
• back wedge
1. Back wedge not aligned properly.
2. Hold down spring tension too tight or
too loose.
3. Improperly adjusted gate horizon.
1. Photo sensor "staging" leading edge of
material too far from hopper plate.
2. Gripper jaw adjusted too far from edge
of hopper plate.
1. Photo sensor "staging" leading edge of
material too far past hopper plate.
2. Gripper jaw adjusted too close to lead-
ing edge of hopper plate.
Review gate assembly adjustment
procedure.
Remove material from stack. Test
again.
Reduce weight. Test again.
Rotate gate adjustment 1/8 turn to
increase gap and manually test. Review
gate assembly adjustment procedure.
Review side guide setting procedure.
Move stack away from belt, even if this
causes stack to be off center from cen-
ter line of feeder.
Review gate assembly adjustment
procedure. Also review inspection and
care procedures. If wear is excessive,
consult with a qualified technician.
Consult with a qualified technician.
1. Turn the Power switch to "Off" by
pressing the circle (O).
2. Remove jammed material from
feeder. While doing so, try to deter-
mine the cause of the jam.
3. Verify each adjustment by reviewing
the "Preparing for Operation" section
of the manual.
Review back wedge adjustment proce-
dure.
Review hold-down spring installation
procedure.
Review gate assembly adjustment
procedure.
Review photo sensor adjustment proce-
dure.
Adjust gripper jaw as required per in-
serter owner's manual.
Review photo sensor adjustment proce-
dure.
Adjust gripper jaw as required per in-
serter owner's manual.
Feed belt(s) not
tracking on rollers
Material skewing
Material too far
from gripper jaw
(Inserter Applica-
tions only)
Table 5-1.
Quick-Look Troubleshooting (continued)
Jamming occurs
during operation
Material too deep
in gripper jaw (In-
serter Applications
only)
Summary of Contents for Streamfeeder V-710DM
Page 1: ...Manual Value Series V 710DM ...
Page 7: ...v Value Series V 710DM Manual ...
Page 47: ...40 Value Series V 710DM Manual 7 Mechanical Components BASE FEATURES ...
Page 49: ...42 Value Series V 710DM Manual BASE FEATURES ...
Page 51: ...44 Value Series V 710DM Manual CARRIAGE ASSEMBLY Assembly 10501102 ...
Page 55: ...48 Value Series V 710DM Manual HOLD DOWN ASSEMBLY Assembly 10501109 ...
Page 57: ...50 Value Series V 710DM Manual GATE PLATE ASSEMBLY Assembly 84111006 ...
Page 59: ...52 Value Series V 710DM Manual TRIANGLE WEDGE ASSEMBLY Assembly 63311018 ...
Page 61: ...54 Value Series V 710DM Manual 8 Electrical Components ...
Page 62: ...55 Value Series V 710DM Manual ...
Page 63: ...56 Value Series V 710DM Manual ...
Page 64: ...57 Value Series V 710DM Manual ...
Page 71: ...64 Value Series V 710DM Manual ...
Page 72: ......