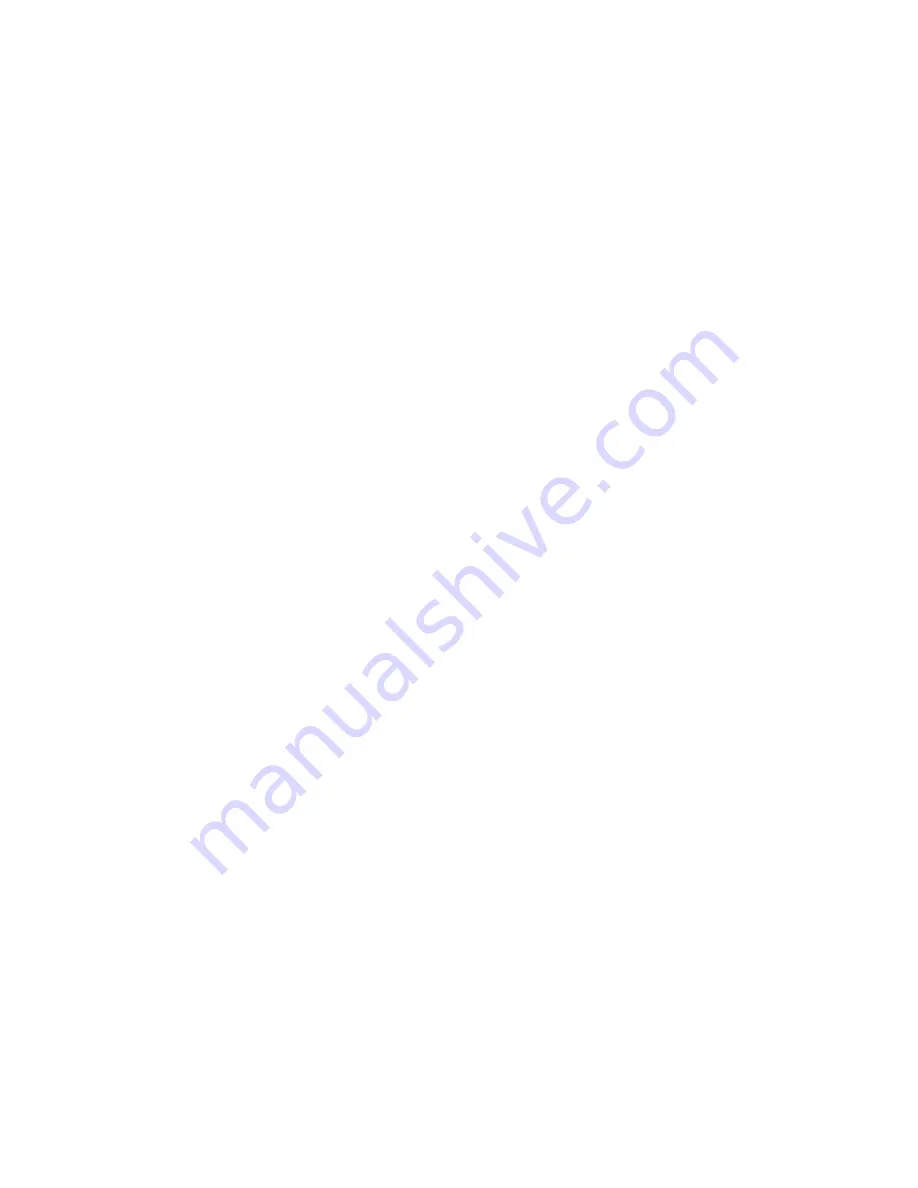
(by-pass) by the lever. The smoke will leave by the tamper to the chimney. All boilers
have heat exchanger for cooling the boiler and protect them in case of overheating.
The boiler design allows achieving high efficiency and the efficient combustion
guarantees minimum exhaust emission of harmful substances and fuel economy.
Combustion process
Phase 1:
Drying of wood.
Phase 2:
Gasification of wood at 450
o
C.
Phase 3:
Burning of mixture of gasified woods with the secondary air at 560
o
C.
Phase 4:
Combusting with increasing flame temperature at 1200oC, at the lower
combustion chamber.
Phase 5:
Outlet the exhaust gases through the torch at 165
o
C.
3.1. Boiler design
Boiler Body
PYROGAS gasification boiler is made of St 37.2 steel plates according to DIN 1700.
Non-metallic parts are made of special materials with high temperature resistant and
designed in that way to have long life time and strength ant to protect the metallic
parts of boiler against the high temperatures.
The boiler is separated in 3 parts; The upper chamber for wood feeding, drying of
wood and gasification of wood, the ceramic plate where burning the gasified woods
with the secondary air and the lower combustion chamber where the flame transfers
the heat to the water. The produced flue gases are directed by three triangle paths
into the smoke chamber and subsequently to the chimney.
An air fan is equipped at the front side of boiler and supplies with primary and
secondary air the upper chamber and the area around the ceramic plate. The
quantity of air is controlled by two switches with screws, one for the primary and one
for the secondary air. The outer of the boiler body is coved with glass wool insulation
and metallic covers.
Doors
The boiler has 3 doors. The first one allows the access to the upper chamber. It is
used for the feeding of boiler with woods. The second one is the middle door and is
used for the cleaning of the openings for the primary and secondary air and also for
the inspection of ventilator and finally the third one is the lower door and is used for
cleaning of the bottom ash. The amount of bottom ash in the boiler is about 1 to 2%
of the total amount of fuels. The lower door is also equipped with a window for
inspection of flame during the operation of boiler.
Ceramic plates
The boiler is equipped with two ceramic plates. The ceramics are constructed to
resist at very high temperature. During the operation the temperature of flame
reaches up to 1200
o
C. The first one is a ceramic plate with jets where the secondary
air is mixed with the gasified woods. The second ceramic plate is placed at the
bottom of the combustion chamber, receives the flame with the high temperature,
protects the boiler against the high temperatures and transfers the heat equally to the
boiler water.