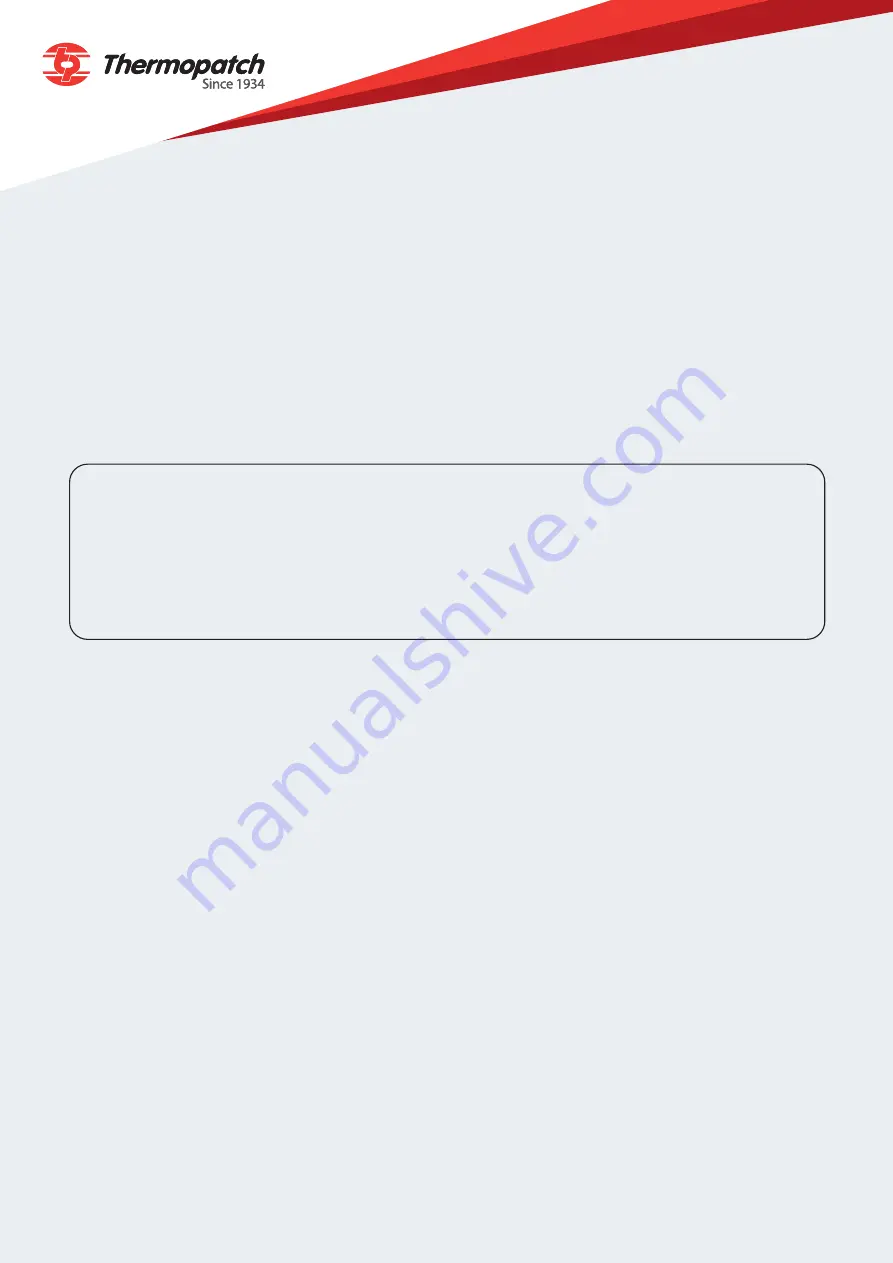
18
For more information about our products and how to contact us, please visit thermopatch.com
8. Maintenance
Before starting any maintenance or repairs, make sure that the machine has finished its work cycle.
Depending on the planned job you want to perform both the air - and electrical supply can be
disconnected.
The air cylinder and other parts of the machine are maintenance free and the bearings are self lubricating.
The precondition for a good working performance is the supply of dry and clean compressed air.
The mounted water condenser and pressure regulator is an added safety feature. Moisture and unclean air
disrupt the self lubricating properties of the air cylinder.
Arrange for your maintenance to be performed by qualified staff or a maintenance service.
Temperature:
The temperature of the heating platen can be tested regularly by using temperature indicator strips. These
can be obtained through your Thermopatch supplier.
Teflon cover:
The teflon sheet that protects the element has to be cleaned regularly to prevent sticking of labels and
patches or transfer of dirt to the garments. Clean the teflon cover with a dry and clean cloth when the
machine is still warm. Repeat the procedure regularly as often as is necessary. Damaged or soiled teflon
protection should be replaced. These can be obtained through your Thermopatch supplier.
Sealing pad:
Clean the sealing pad while still warm, with a clean lint free piece of cloth. Clean it as often as is necessary.
Damaged or soiled sealing pads have to be replaced. These can be obtained through your Thermopatch
supplier.
Replacement of the teflon protection and the sealing pad:
The teflon protection sheet and the silicone rubber sealing pad have to replaced regularly. At replacing
these consumable parts the machine should be cooled down sufficiently to avoid burns from the heating
platenn.
Remove the teflon protection cover like a band aid when the platenn is still warm to the touch. Remove any
glue residue from the heatin element carfully. When placing the new self adhesive teflon ensure a smoot
and clean surface in order to have a bubble free adhesion.
The sealing pad can easily be worked loose with a screwdriver after which the replacement sealing pad can
be clicked into place on the mounting platen.
Both the teflon cover and the sealing pad are available through your Thermopatch supplier.
WARNING!
The supplied pressure should not be higher than a maximum of 6 bar
WARNING!
Remove the plug from the wall socket before starting loosening any screws and housing parts