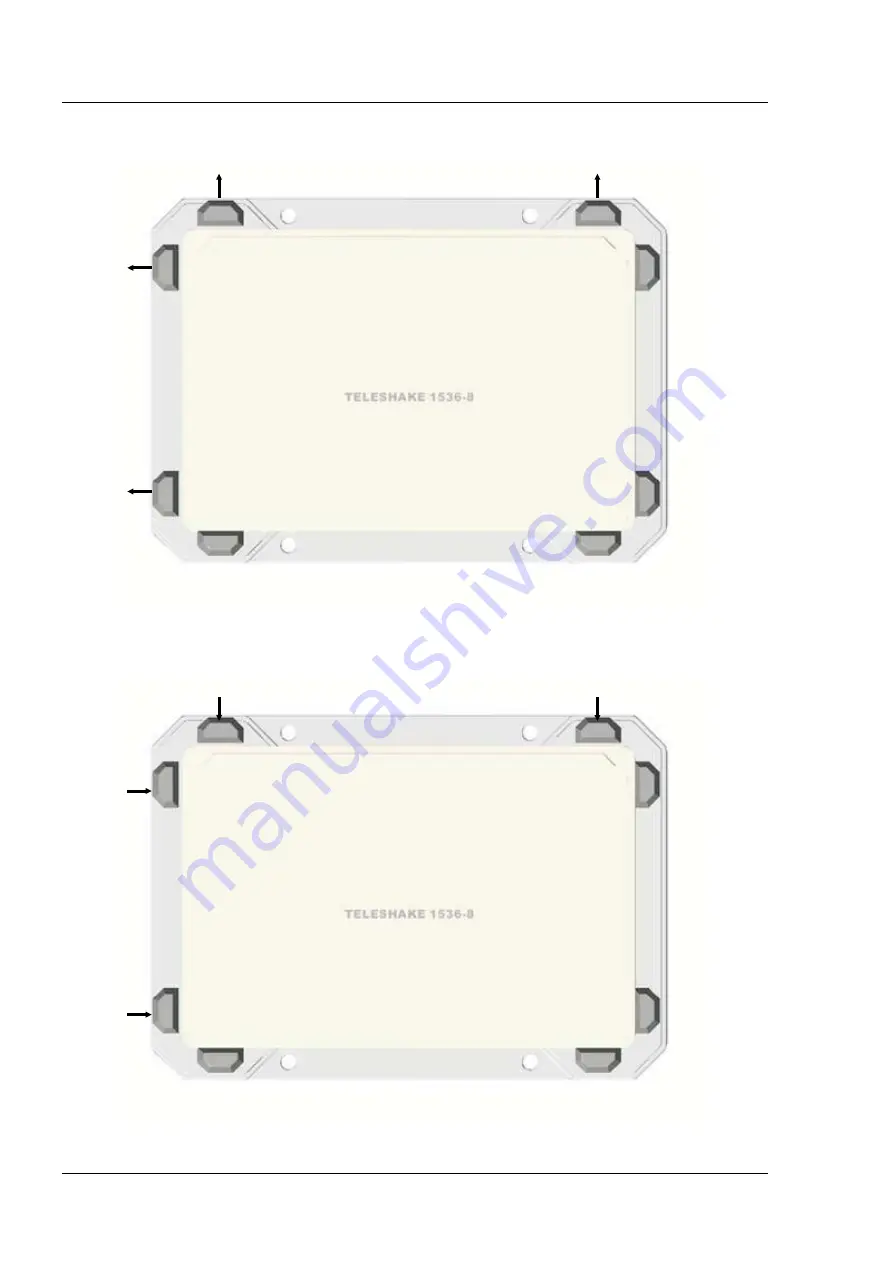
5 Manual operation
Thermo Scientific
16
50134830_03.2012
Figure 8 : TELESHAKE 1536-8 and LIFT, open fixating elements
Figure 9 : TELESHAKE 1536-8 and LIFT, locked fixating elements
Back: movable fixating elements
Front: stationary fixating elements
L
ef
t:
m
o
v
ab
le
f
ix
a
ti
n
g
e
lem
e
n
ts
R
ig
h
t:
s
ta
ti
o
n
ar
y
f
ix
at
in
g
el
em
en
ts
Back: movable fixating elements
Front: stationary fixating elements
L
ef
t:
m
o
v
ab
le
fi
x
at
ing
el
e
m
en
ts
R
ig
h
t:
s
ta
ti
o
n
ar
y
f
ix
at
in
g
el
em
en
ts