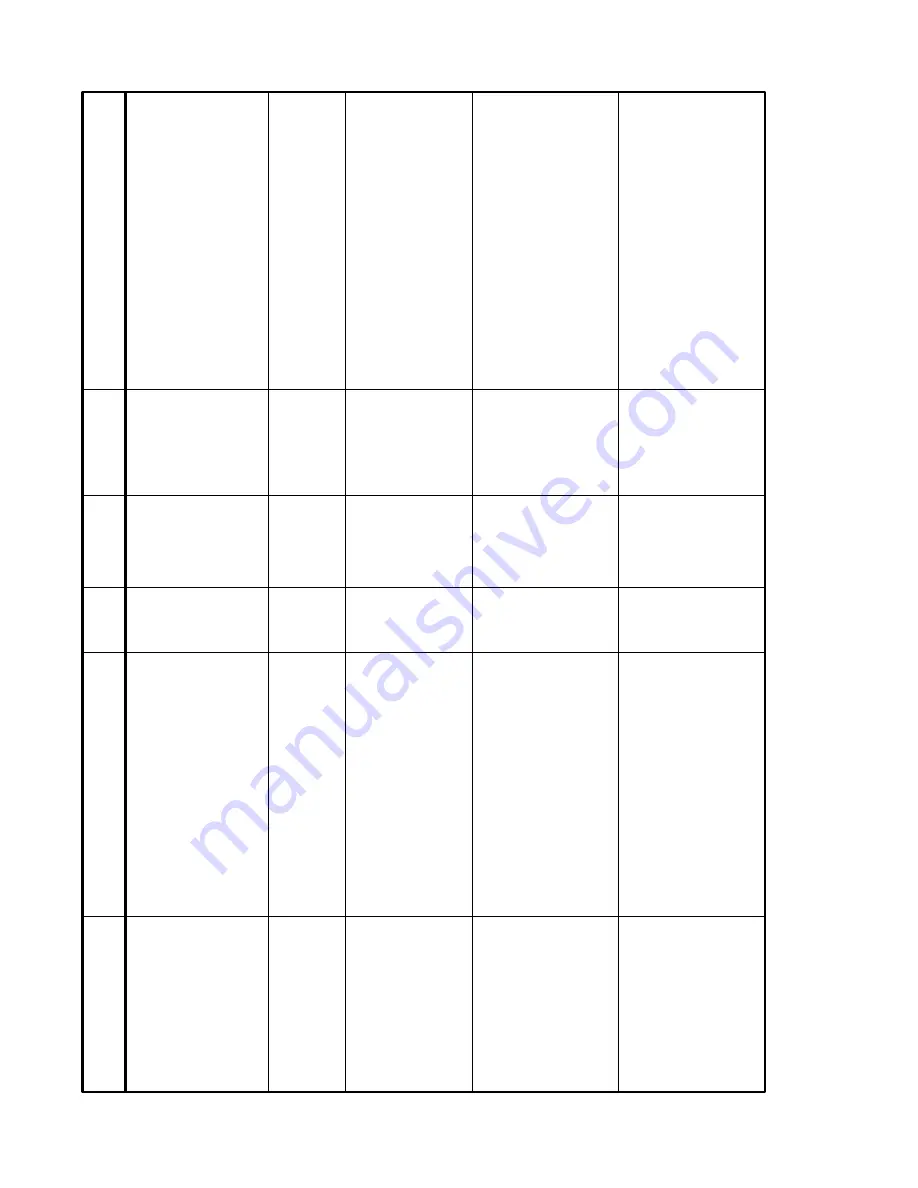
Alarm Message
Alarm Criteria
Alarm Delay*
Alarm
Ringback*
System State
Corrective
Action
Electrical power has been disrupted
Upon
power up
15 min.
None
Alarm light on
Audible alarm on
Blower fans on
Shaker motor on
Heaters on
Not af
fected
Press
to silence the audible alarm
Check if lid is completely closed
Check temperature tracking limit
Check sensor circuit
Replace main temperature sensor
Call
SILENCE
T
echnical Services Department
W
arning notice only
Press
to silence the audible alarm
SILENCE
T
emperature is Low
Power Failure
T
emperature is above the control system’
s
temperature tracking limit
*
Alarm Delay and Ringback times are approximate
**
A
3.5
hour
time delay
is built into
the
system
to
allow
the
shaker to
reach
the
temperature setpoint.
When
this
point
is reached,
a 20
minute delay
becomes ef
fective.
When
the
lid
is opened, a 15
minute interval is added
to
allow
the
system
to
recover
to
the
set temperature. (Note:
All times are approximate)
Count-down time has reached zero
RPM is above control set point by
tracking limit
RPM is below control set point by
tracking limit
None
2 min.
2 min.
None
15 min.
15 min.
Alarm light on
Audible alarm on
Blower fans on
Shaker motor of
f
Heaters on
Alarm light on
Audible alarm on
Blower fans on
Shaker motor on
Heaters on
Alarm light on
Audible alarm on
Blower fans on
Shaker motor on
Heaters on
Advisory notice only
Press
to silence the alarm
SILENCE
Press
to silence the audible alarm
Check platform loading
Check RPM tracking limit setting
Shut the unit of
f and call
Department
SILENCE
T
echnical Services
Press
to silence the audible alarm
Check for overloaded platform
Check for obstruction to edges of platform
Check for low input
AC mains voltage
Shut the unit of
f and call
SILENCE
T
echnical Services
Cycle Complete
RPM High
RPM Low
Department
* *
Summary of Contents for SHKE8000 Series
Page 1: ...Model SHKE8000 Series MaxQ Orbital Shaker Operating and Maintenance Manual 7000443 Rev 4 ...
Page 9: ......
Page 46: ...Model SHKE8000 Series Shakers 2 23 Thermo Scientific Section 2 Operation ...
Page 47: ...2 24 Model SHKE8000 Series Shakers Thermo Scientific Section 2 Operation ...
Page 48: ...Model SHKE8000 Series Shakers 2 25 Thermo Scientific Section 2 Operation ...
Page 49: ...2 26 Model SHKE8000 Series Shakers Thermo Scientific Section 2 Operation ...
Page 50: ...Model SHKE8000 Series Shakers 2 27 Thermo Scientific Section 2 Operation ...
Page 51: ...2 28 Model SHKE8000 Series Shakers Thermo Scientific Section 2 Operation ...
Page 63: ...4 8 Model SHKE8000 Series Shakers Thermo Scientific Section 4 Service ...
Page 64: ...Model SHKE8000 Series Shakers 4 9 Thermo Scientific Section 4 Service ...
Page 65: ...4 10 Model SHKE8000 Series Shakers Thermo Scientific Section 4 Service ...
Page 66: ...Model SHKE8000 Series Shakers 4 11 Thermo Scientific Section 4 Service ...
Page 67: ...4 12 Model SHKE8000 Series Shakers Thermo Scientific Section 4 Service ...
Page 68: ...Model SHKE8000 Series Shakers 4 13 Thermo Scientific Section 4 Service ...
Page 79: ...6 4 Model SHKE8000 Series Shakers Thermo Scientific Section 6 Parts List ...
Page 80: ...Model SHKE8000 Series Shakers 6 5 Thermo Scientific Section 6 Parts List ...
Page 81: ...6 6 Model SHKE8000 Series Shakers Thermo Scientific Section 6 Parts List ...
Page 82: ...Model SHKE8000 Series Shakers 6 7 Thermo Scientific Section 6 Parts List ...
Page 83: ...6 8 Model SHKE8000 Series Shakers Thermo Scientific Section 6 Parts List ...
Page 84: ...Model SHKE8000 Series Shakers 6 9 Thermo Scientific Section 6 Parts List ...
Page 85: ...6 10 Model SHKE8000 Series Shakers Thermo Scientific Section 6 Parts List ...
Page 86: ...Model SHKE8000 Series Shakers 6 11 Thermo Scientific Section 6 Parts List ...
Page 87: ......
Page 88: ...Model SHKE8000 Series Shakers 7 1 Thermo Scientific ...
Page 89: ......
Page 90: ...Model SHKE8000 Series Shakers 8 1 Thermo Scientific ...
Page 91: ...8 2 Model SHKE8000 Series Shakers Thermo Scientific ...
Page 92: ...Model SHKE8000 Series Shakers 8 3 Thermo Scientific ...
Page 93: ...8 4 Model SHKE8000 Series Shakers Thermo Scientific ...
Page 94: ...Model SHKE8000 Series Shakers 8 5 Thermo Scientific ...
Page 95: ...8 6 Model SHKE8000 Series Shakers Thermo Scientific ...
Page 96: ...Model SHKE8000 Series Shakers 8 7 Thermo Scientific ...
Page 97: ...8 8 Model SHKE8000 Series Shakers Thermo Scientific ...
Page 98: ...Model SHKE8000 Series Shakers 8 9 Thermo Scientific ...
Page 99: ...8 10 Model SHKE8000 Series Shakers Thermo Scientific ...
Page 100: ...Model SHKE8000 Series Shakers 8 11 Thermo Scientific ...
Page 101: ...8 12 Model SHKE8000 Series Shakers Thermo Scientific ...
Page 104: ......
Page 105: ......