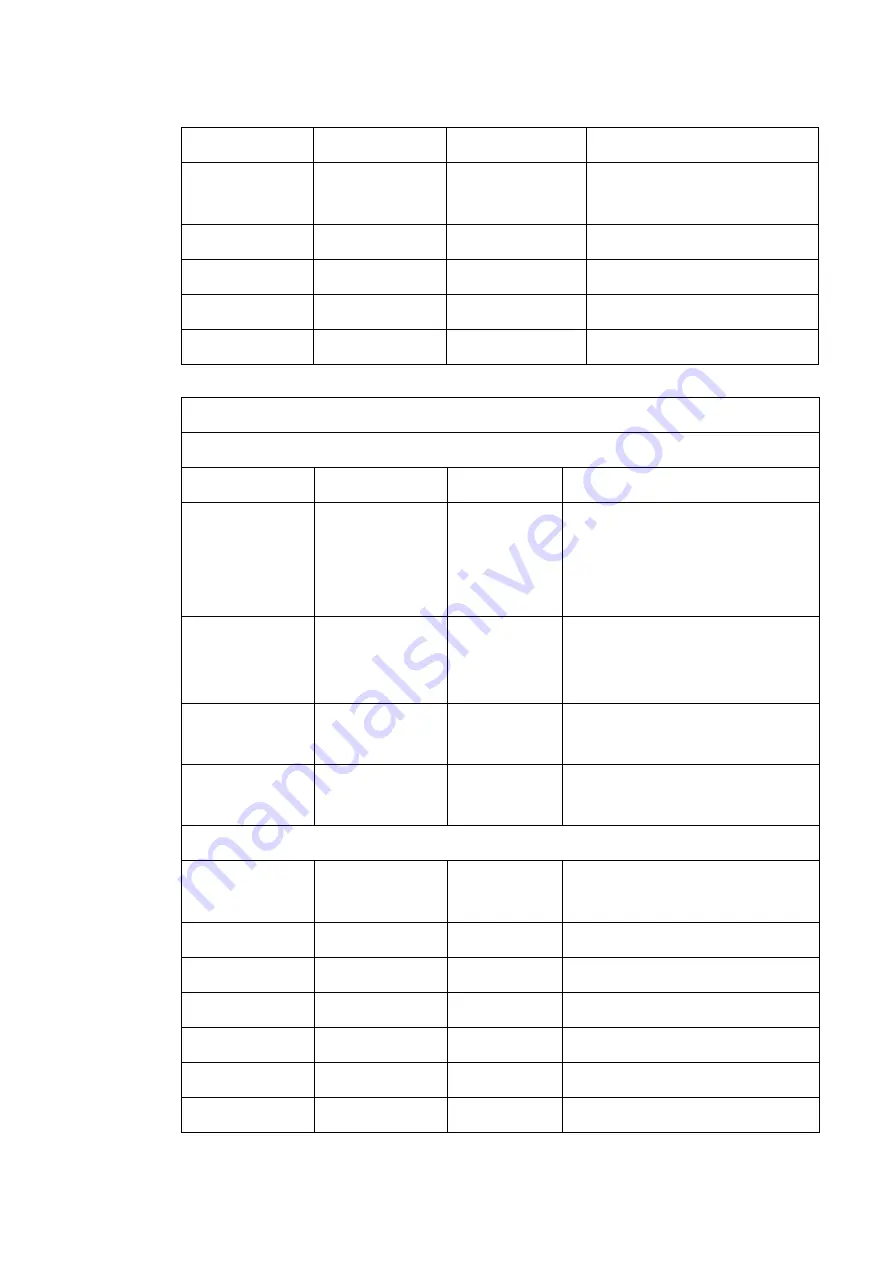
Operation - UT150 Controller
UP150 Controller Overview
6-4
Thermo Scientific
Table 2. Access to Operating Parameters
PSL
0
0
Protocol Selection
Adr
1
1
Controller Address, selec-
tion upto 99
bPS
9600
9600
Baud Rate
Pr 1
EVN
EVN
Parity (even)
StP
1
1
Stop Bit
dLn
8
8
Data Length.
Press and Hold SET/ENT for three second
Press SET/ENT to view each parameter, Arrows to select values.
Parameter
°C Value
°F Value
Description
node
rES
rES
Operation Mode: reset (no
output)
rUn, running the program;
LCL, local (single setpoint)
PrG
0
0
Program access, select
“1”and SET/ENT to enter
menu
£ HoLd
oFF
oFF
Program hold mode: on to
suspend program time
£ AdV
oFF
oFF
Program advance mode: to
skip the current segment
£ Parameter and value only displayed while program is running
LSP
0 to 1200
32 to 2192
Local Setpoint: selectable
through equipment range
CtL
Pid
Pid
Control Mode
At
oFF
oFF
Auto Tuning
P
26
47
Proportional Band
I
73
73
Integral Time
d
18
18
Derivatives Time
Ct
1
1
Heat Cycle Time
Summary of Contents for CC58114PBC
Page 1: ......
Page 6: ...List of Figures ii Thermo Scientific ...
Page 12: ...Introduction 2 2 Thermo Scientific ...
Page 14: ...Unpacking 3 2 Thermo Scientific ...
Page 20: ...Installation Thermocouple Wiring Installation 4 6 Thermo Scientific ...
Page 22: ...Initial Start up 5 2 Heratherm Thermo Scientific ...
Page 46: ...Communication Option Addresses for Multiple Controllers 7 6 Thermo Scientific ...
Page 50: ...Excess Temperature Option Excess Temperature Controller Operation 8 4 Thermo Scientific ...
Page 57: ...Replacement Parts Thermo Scientific Heratherm 11 3 Figure 5 Wiring Diagram ...
Page 58: ...Replacement Parts 11 4 Heratherm Thermo Scientific ...
Page 59: ...Thermo Scientific 12 1 12 Error Codes This chapter is not applicable ...
Page 60: ...Error Codes 12 2 Thermo Scientific ...
Page 62: ...WEEE Compliance 13 2 Thermo Scientific ...
Page 63: ...Thermo Scientific 14 1 14 14 Spare Parts and Accessories This chapter is not applicable ...
Page 64: ...Spare Parts and Accessories 14 2 Thermo Scientific ...