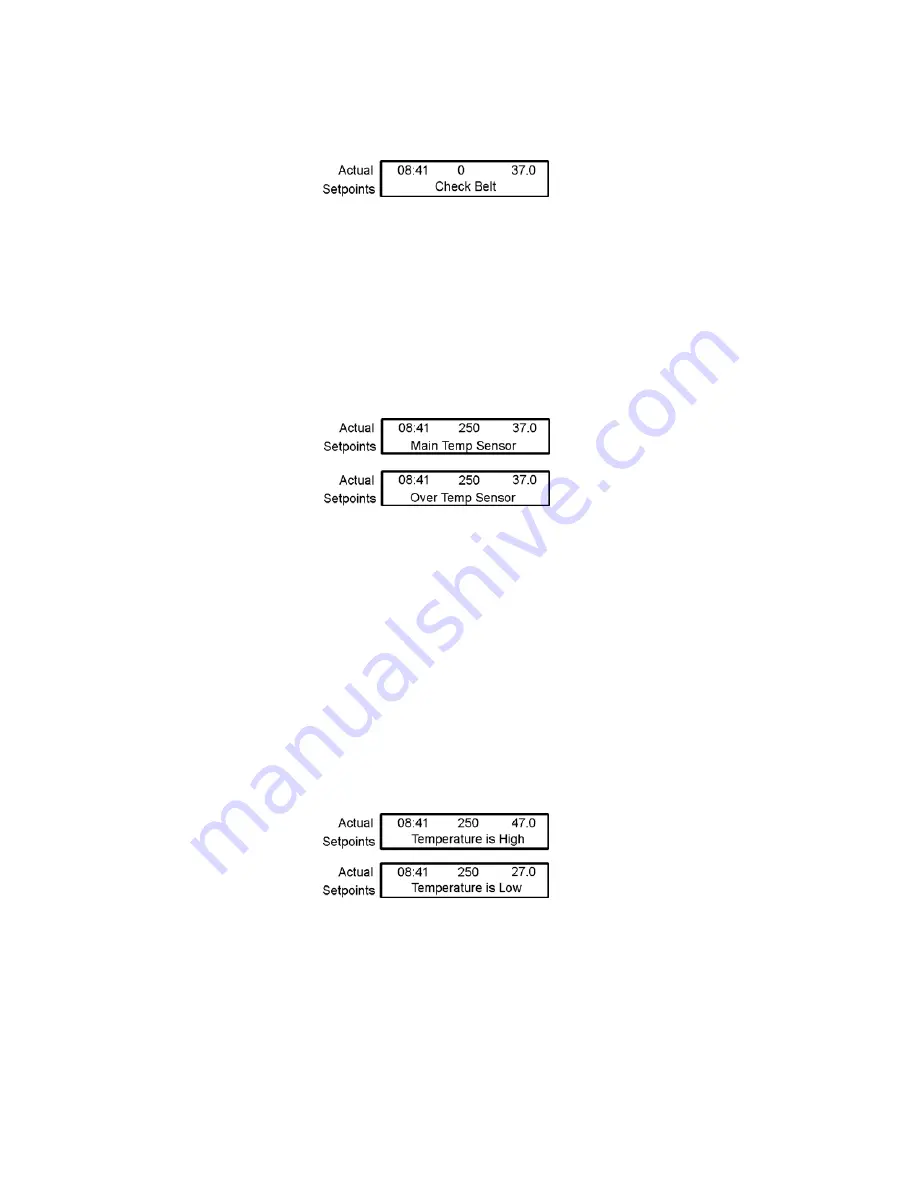
Check Belt alerts the operator that the drive belt may have broken or
something is slowing or preventing platform movement.
In the alarm state, the audible alarm is silenced by pressing the Silence
button, but will ring back in about 30 minutes. The screen message and
warning lights, however, will continue until the fault is corrected. Then,
the alarm message is cleared by cycling power to the unit OFF, then ON.
Sensor Fault alerts the operator that either of the shaker’s two temperature
sensors have failed. An alarm message similar to those shown below will
show which sensor has failed.
When in the alarm state, the audible alarm is silenced by pressing the
Silence button, but rings back in about 15 minutes if the fault condition
persists. The screen message and warning lights continues until the fault is
corrected.
When the sensor problem is corrected, the alarm message is cleared by
pressing the Silence button.
Temperature High or Temperature Low alerts the operator that the
operating temperature of the shaker has risen above or fallen below the
programmed temperature tracking limit control point. Therefore, either of
the alarm messages shown below will be displayed.
In the alarm state, the audible alarm is silenced by pressing the Silence
button, but rings back in about 15 minutes if the fault condition persists.
The screen message and warning lights continues until fault is corrected.
After the temperature problem is corrected, press the Silence button to
clear the alarm message.
2-8
Orbital Shaker
Thermo Scientific
Section 2
Operation
Check Belt
Sensor Fault
Temperature High or Low
Summary of Contents for 420 Series
Page 37: ......
Page 38: ......
Page 39: ......
Page 57: ......
Page 59: ......
Page 60: ...Orbital Shaker 7 1 Thermo Scientific Section 7 Electrical Schematics ...
Page 61: ...7 2 Orbital Shaker Thermo Scientific Section 7 Electrical Schematics ...
Page 64: ...Orbital Shaker 9 1 Thermo Scientific ...
Page 65: ......