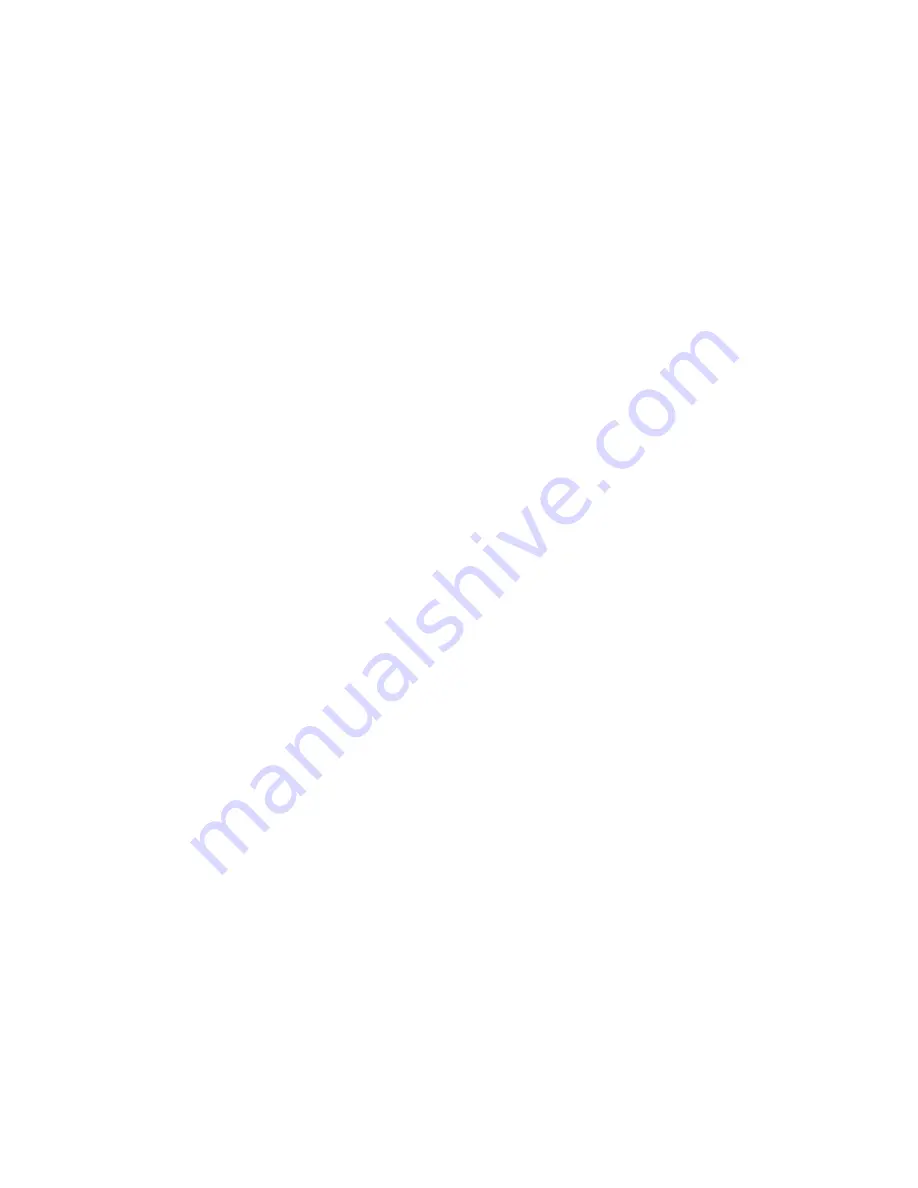
Clean Room Oven
4-3
Thermo Scientific
Section 4
Unpacking and Installation
Inert gas, such as nitrogen, can be injected into the chamber to flush out
impurities. The gas inlet, on the back of the oven, is a 1/8-inch NPT pipe.
Connect Tygon® R-3603 tubing to this pipe and to the dual regulator on
the gas source. Leave the gas turned off until the oven is being operated.
If the oven is to be operated without gas, keep the inlet capped-DO NOT
USE THE PLASTIC SHIPPING CAP.
Warning
Inject only an inert gas into the oven. The use of any other type
gas may lead to fire or explosion and serious injury or death and property
damage.
▲
During shipping, the oven door may have been knocked out of line. The
following procedure will correct door-to-body and door-to-gasket
misalignment.
1. Lay the unit on its back. If exhaust and purging ports are fitted,
support the unit on 2' x 4's to protect these components.
2. Remove the pivot bolt and flat washer from the top door hinge.
3. Unlatch the door handle to release the door, then slide the door out
and off the bottom hinge pivot bolt to gain access to hinge screws.
4. Slightly loosen hinge screws on top and bottom hinges, so hinges
require firm hand pressure to reposition. DO NOT REMOVE
HINGE SCREWS - complete removal of screws will make it extremely
difficult to reassemble the hinge.
5. Replace the door on the bottom hinge pin and fit the door in place.
Loosen the bottom hinge pivot bolt with an open-end wrench. Replace
the top hinge pivot bolt and set it to be finger-tight.
6. Align the door to the body-top, bottom and sides.
7. Remove the top hinge pivot-bolt again, noting the position of properly
aligned hinges. Remove the door carefully without moving the hinges
out of position.
8. Tighten all hinge screws VERY securely.
9. Replace door on bottom hinge pivot bolt. Replace the top pivot bolt
and washer. Tighten top and bottom hinge pivot bolts VERY securely
to maintain proper alignment.
Gas Connection
Door Adjustment