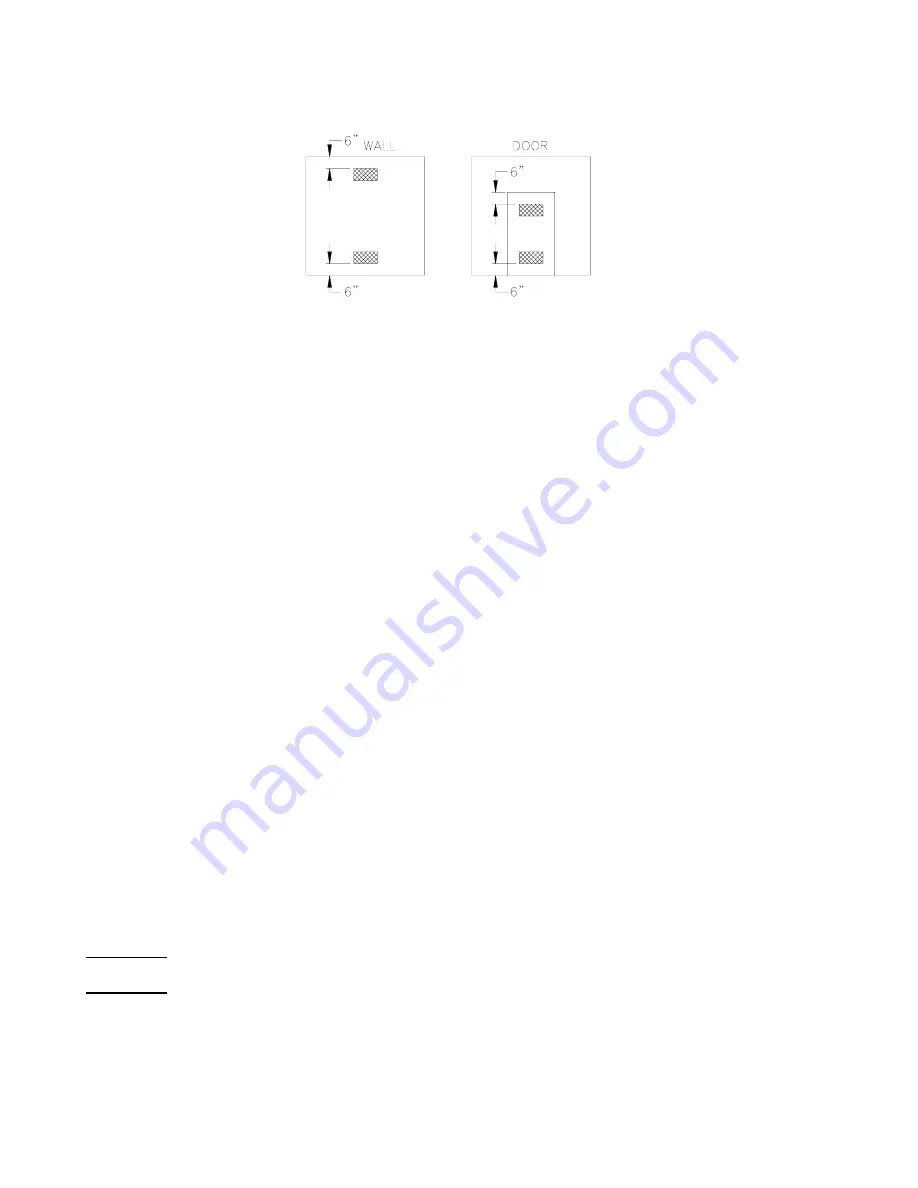
All installations and services must be performed by qualified service personnel.
5
EXAMPLE:
100,000 BTUH input furnaces requires "two" openings of 100 square inches each. A minimum opening of
100 square inches is required regardless of the input.
If the building is tightly constructed and or has an exhaust fan(s) that creates a negative pressure, air for combustion and
ventilation must be supplied from the outdoors or from spaces freely communicating with the outdoors. When
communicating directly with the outdoors or with vertical ducts to the outdoors, two openings each having a minimum free
area of 1 square inch per 4,000 BTU of the input rating of all gas appliances in the area are required. When horizontal ducts
are used to communicate with the outdoors, the free area must be based on 2,000 BTUH per square inch of the total input
rating of all gas appliances in the area. The minimum dimension of an air duct must be at least 4 inches in diameter.
EXAMPLE:
100,000 BTU input furnace, 40,000 BTU input water heater and 30,000 BTU gas dryer would require two
openings of 42.5 square inches each if ducted vertically to the outdoors or 85 square inches each if horizontal ducts are
used.
MAKE-UP AIR
Today's emphasis on home insulation and tightness increases the problem of air supply to the furnace. Heavy insulation cuts
off infiltration of outside air, which previously replaces inside air removed by bathroom, kitchen and laundry vent fans and
air escaping up chimneys. This tightness can cause a negative pressure condition to develop within the home. For this
reason, it is recommended that in tightly constructed and insulated homes, make-up air be provided. This can be done with
Skuttle Mfg. Co. 200 Series make-up air control. This control installs quickly and easily on any warm air heating system and
delivers controlled, fresh air automatically during the winter and summer. This type control helps solve a negative pressure
problem in a structure.
D. VENTING:
NOTICE:
A draft control (double acting (MG-1) or hood type) suitable for gas firing, certified by a nationally recognized
testing laboratory and acceptable to local codes must be installed according to the control manufacturer's instructions.
The PGT and PGL series furnaces must be vented in accordance with local codes and the National Fuel Gas Code (ANSI-
Z223.1 Latest Edition) Category 1 vent tables.
The vent connector must be galvanized or stainless steel metal pipe.
The following items are requirements:
1. Flue or vent connection materials must meet requirements of all applicable local codes and the National Fuel Gas Code
(ANSI-Z223.1 LATEST EDITION).
2. A PVC pipe is not an acceptable substitute for a chimney or a flue connector. A chimney with an internal construction of
stainless steel or some other material that will withstand the flue gas temperature of 500°F is required.
3. A type B venting system as well as some masonry systems are acceptable as described in the venting tables included in
the NFGC. These venting tables also include venting combinations, which apply to common venting arrangements of two
appliances.
WARNING:
When common venting two appliances into a common vent, the smallest appliance must be vented into the top
opening.
WARNING:
A Category 1 appliance must never be connected to a chimney that is servicing a solid fuel appliance. If a
fireplace chimney, lined with a metal liner is used to vent this appliance, the fireplace opening must be permanently sealed.
4. The chimney height is determined by the height of the surrounding trees, roof, buildings and terrain. The chimney should
extend 24" above any surrounding obstructions.
Summary of Contents for PGL20-180
Page 24: ...All installations and services must be performed by qualified service personnel 22...
Page 25: ...All installations and services must be performed by qualified service personnel 23...
Page 26: ...All installations and services must be performed by qualified service personnel 24...
Page 27: ...All installations and services must be performed by qualified service personnel 25...
Page 35: ...All installations and services must be performed by qualified service personnel 33...
Page 36: ...All installations and services must be performed by qualified service personnel 34...
Page 37: ...All installations and services must be performed by qualified service personnel 35...
Page 38: ...All installations and services must be performed by qualified service personnel 36...