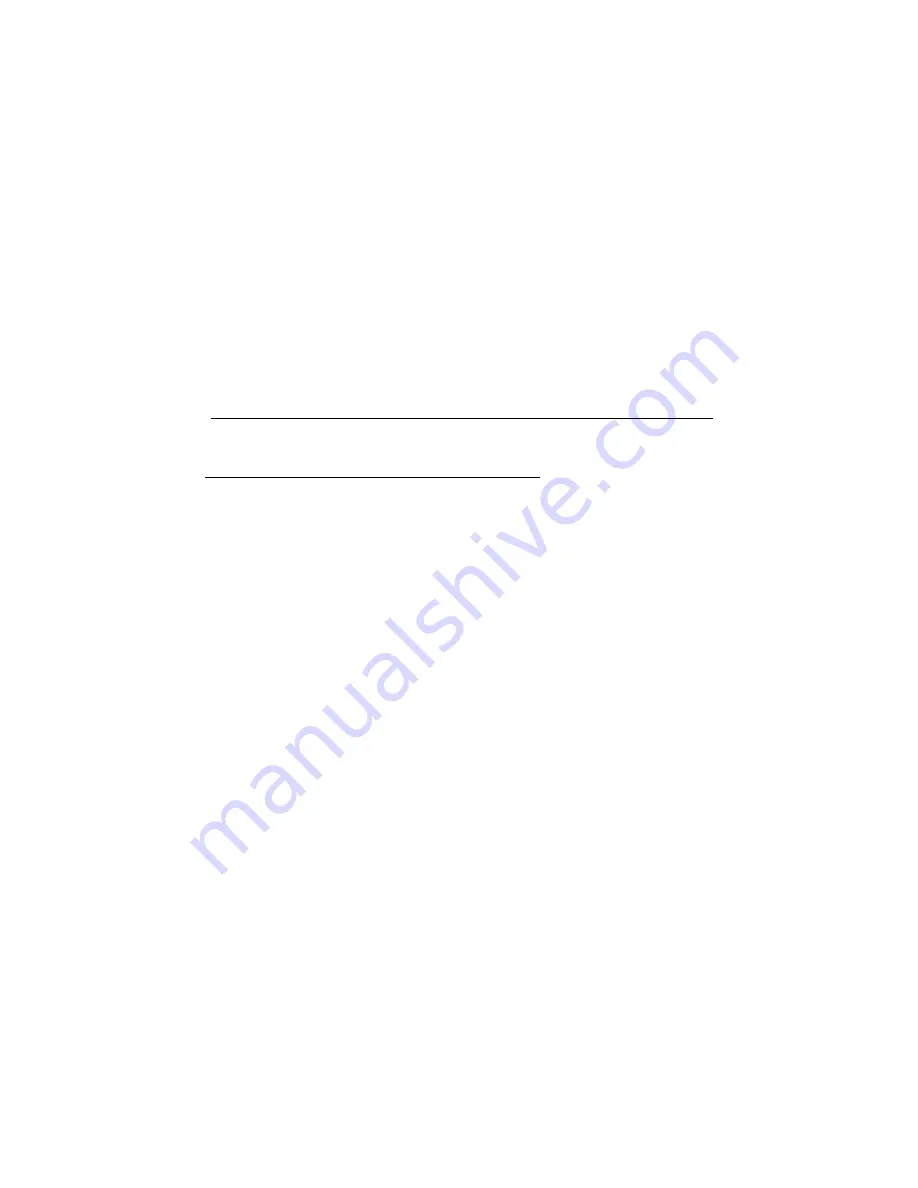
All installations and services must be performed by qualified service personnel.
28
elevation of 2,000 feet or less, no reduction in input is required. Your gas supplier will supply you with the correct
BTU and orifice sizing information.
To check the input of your natural gas furnace, proceed as follows:
a. Call your gas supplier and ask for the BTU content (heating valve) of one cubic foot of the gas, supplied to the
installation area. An alternate approach is to assume a value of 1025 BTU/Cu Ft that is the national average.
b. With all other gas appliances turned off, allow the unit to operate for 10 to 15 minutes. Using a stopwatch, clock
the time required for the (small) dial on the gas meter to make one full revolution. The meter will state how many
cubic feet are flowing for each revolution usually one, two or five. The unit must have been in operation at least 10
minutes before clocking.
FORMULA:
BTU/Cu
Ft
x
Number
of
Cu
Ft
x
3600
Seconds
=
Input
BTU/hr
Seconds for one revolution
EXAMPLE:
1025 BTU/Cu Ft x 2 Cu Ft x 3600 = 98.663 BTU Input
74.8 Seconds
Check for the model number of this furnace, its input, the type of gas and the manifold pressure on the information
plate located on the vestibule panel behind the upper front panel. If using the above example, the furnace was a
PGT5-100 model the 98,663 BTU input would be acceptable because it was within 2% of the listed input of
100,000.
c. Make sure that the gas supply pressure to the furnace falls within the maximum range of 5-1/2" to 14" WC
pressure on natural gas and 11.0" to 14.0" WC on LP gases. The pressure to the furnace must be checked while the
furnace burner and any other gas appliances on the same supply system are operating, using the test procedure
outlined in Section H of this manual.
This gas furnace is equipped with a fixed orifice sized for the manifold pressure shown in the burner manual. The
input can be increased or decreased by adjusting the manifold pressure. Remove the 1/8" threaded pipe plug located
on the bottom right side of the gas valve. Use a U tube manometer or pressure gage to measure the pressure. To
adjust the pressure, remove the cap from the regulator on the top of the gas valve and using the adjustment screw,
decrease the pressure by turning the screw counterclockwise or increase it by turning the screw clockwise.
ADJUSTMENTS TO THE LISTED PRESSURE MUST NOT EXCEED the recommended maximum manifold
pressures in the burner manual.
If a gas meter is not available for natural gas, or the unit is installed on liquified petroleum gases which are not
metered, the correct input can be assumed if the furnace manifold pressure is the same as that shown on the
information label and the orifices are sized correctly.
Shut off the gas supply to the furnace. Remove the pressure gage and re-install the pipe plug using a thread
compound resistant to the action of LP gases.
If the rated input cannot be obtained with the present orifice at the correct pressure, your local gas supplier will assist
in sizing the proper orifice. Our Engineering Department will gladly assist in sizing the orifice if you provide them
with the heating value in BTU per cubic foot and the specific gravity of the gas.
Summary of Contents for PGL20-180
Page 24: ...All installations and services must be performed by qualified service personnel 22...
Page 25: ...All installations and services must be performed by qualified service personnel 23...
Page 26: ...All installations and services must be performed by qualified service personnel 24...
Page 27: ...All installations and services must be performed by qualified service personnel 25...
Page 35: ...All installations and services must be performed by qualified service personnel 33...
Page 36: ...All installations and services must be performed by qualified service personnel 34...
Page 37: ...All installations and services must be performed by qualified service personnel 35...
Page 38: ...All installations and services must be performed by qualified service personnel 36...