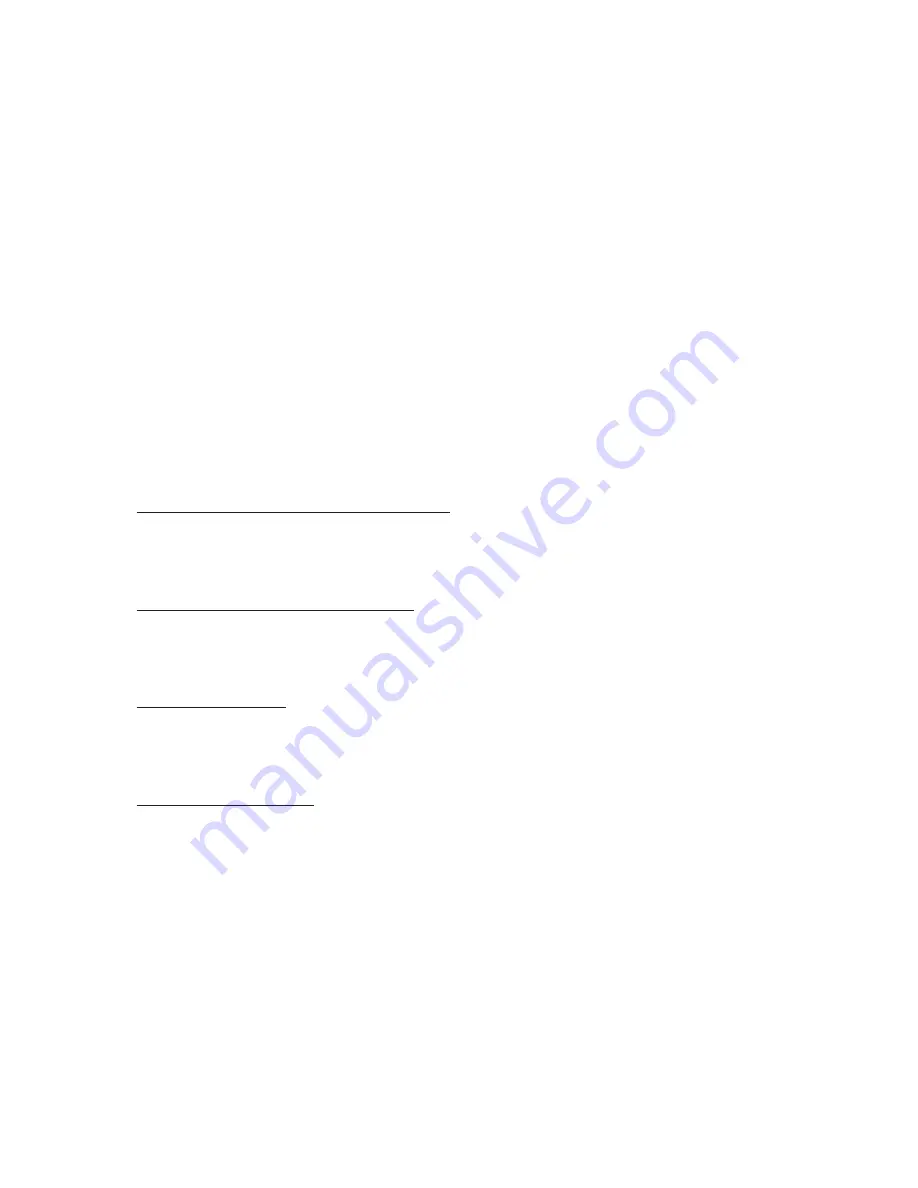
7
increased if you have a vented dryer in the basement or other venting fans in the home.
Boilers located in confined spaces shall be provided with two permanent openings, one
near the top and one near the bottom of the enclosure. Each opening shall have a free
area of not less than one square inch per 1000 BTU per hour input rating of the boiler,
freely communicating with interior areas having adequate infiltration from the outside.
8) Fill boiler and system with water. Be sure entire system has been purged of air and the
desired pressure is obtained. Leak-check the boiler and piping system by turning off the
make-up water supply and observing the boiler pressure gage. A loss of pressure indi-
cates a system leak that must be repaired prior to operating the boiler.
9) Remove the nozzle line assembly and check that the correct nozzle is installed for the
desired firing rate. Check that burner settings are correct for the nozzle that is installed.
See the Installer/Serviceman Label.
10) Connect burner to fuel supply. Refer to fuel unit manufacturer literature for piping, connec-
tions, lift and tank installation. If such information is unavailable use the following guide lines.
FUEL UNITS/FUEL LINES
Fuel supply “level with” or “above” burner:
A single stage fuel unit connected to the fuel
supply with a single supply line is the most common type of installation for these conditions.
Manual venting of the fuel unit is usually required on initial start-up. Failure to vent air could
result in an air lock/oil starvation condition. (One pipe)
Fuel supply below the level of burner:
Use a single stage fuel unit in lift conditions of up to
10 ft., and a two stage fuel unit when the lift exceeds 10 ft. Both conditions require the use of
a return line which purges the fuel unit of air returning it to the fuel tank. The “by-pass” plug
must be inserted into the fuel unit when installing a return line. (Two pipe)
Fuel line installation:
Continuous lengths of heavy wall copper tubing are recommended
and should be installed under the floor when possible. Always use flare fittings. Always install
fittings in accessible locations. Never use teflon tape on any fuel fitting. Use of teflon will void
any warranty. Fuel lines should not run against the appliance or the ceiling joists.
Fuel line valve and filter:
Install two high quality shutoff valves in accessible locations on
the oil supply line. Locate one close to the tank and the other close to the burner ahead of the
filter. Some filters come with built-in shutoff valves. Install a generous capacity filter inside the
building between the fuel tank shutoff valve and the burner locating both the filter and the
valve close to the burner for ease of servicing.
CAUTION:
All oil feed lines to burners must be air tight. Use only flare fittings when assem-
bling oil lines since the slightest air leak, caused by loose fittings, bad gaskets or any other
reason, can cause a foaming oil stream which will cause any of the following conditions:
a) Intermittent firing, causing safety shutdown
b) Poor starts
c) Smokey starts
d) Continual sooting of boiler and burner parts including the cad cell
e) Reduced firing rate, inefficient operation and erratic fire pattern
f) A dangerous combustion condition, allowing the firebox to fill with a lean mixture (too
much air in the oil stream) which could cause a delay in ignition of the fuel mixture until
the danger point has been reached.