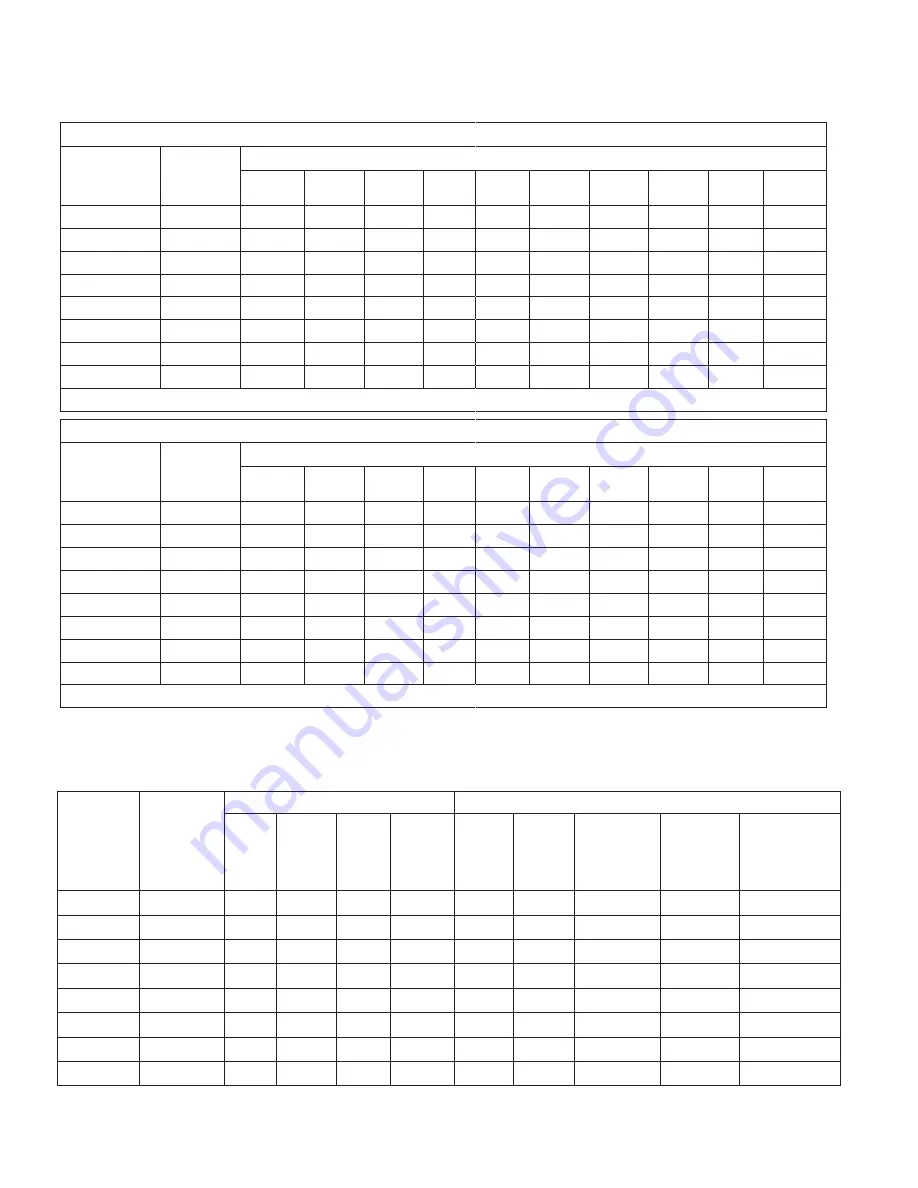
60
. Gas Piping
(continued)
Natural Gas, Inlet Pressure 14.0 in wc (3.4 kPa)or less; 0.5 in wc (0.12 kPa) Pressure Drop
Nominal
Pipe Size
(In)
Inside
Diameter
(In)
Length of Pipe (Ft)
10
20
30
40
50
60
70
80
90
100
½
0.622
172
118
95
81
72
65
60
56
52
50
¾
0.824
360
247
199
170
151
137
126
117
110
104
1
1.049
678
466
374
320
284
257
237
220
207
195
1¼
1.380
1390
957
768
657
583
528
486
452
424
400
1½
1.610
2090
1430
1150
985
873
791
728
677
635
600
2
2.067
4020
2760
2220
1900 1680
1520
1400
1300
1220
1160
2½
2.469
6400
4400
3530
3020 2680
2430
2230
2080
1950
1840
3
3.068
11300
7780
6250
5350 4740
4290
3950
3674
3450
3260
*1 CFH of Natural Gas is approximately equal to 1 MBH; contact your gas suppliers for the actual heating value of your gas.
Nominal
Pipe Size
Inside
Diameter
(in)
Valves (Screwed) - Fully Open
Screwed Fittings
Gate Globe Angle Swing
Check
45°
Elbow
90°
Elbow
180 Close
Return
Bend
90 Tee
Flow
Through
Run
90 Tee, Flow
Through
Branch
½
0.622
0.4
17.3
8.7
4.3
0.7
1.6
3.5
1.6
3.1
¾
0.824
0.5
22.9
11.4
5.7
1.0
2.1
4.6
2.1
4.1
1
1.049
0.6
29.1
14.6
7.3
1.2
2.6
5.8
2.6
5.2
1¼
1.38
0.8
38.3
19.1
9.6
1.6
3.5
7.7
3.5
6.9
1½
1.61
0.9
44.7
22.4
11.2
1.9
4.0
9.0
4.0
8.0
2
2.067
1.2
57.4
28.7
14.4
2.4
5.2
11.5
5.2
10.3
2½
2.469
1.4
68.5
34.3
17.1
2.9
6.2
13.7
6.2
12.3
3
3.068
1.8
85.2
42.6
21.3
3.6
7.7
17.1
7.7
15.3
Table 31:
Maximum capacity of schedule 40 black pipe in CFH*
Table 32:
Equivalent Lengths of Standard Pipe Fittings & Valves (ft)
Propane Gas, Inlet Pressure 11.0 in wc (2.7 kPa); 0.5 in wc (0.12 kPa) Pressure Drop
Nominal
Pipe Size
(In)
Inside
Diameter
(In)
Length of Pipe (Ft)
10
20
30
40
50
60
70
80
90
100
½
0.622
116
80
64
55
48
44
40
38
35
33
¾
0.824
242
166
134
114
101
92
85
79
74
70
1
1.049
456
314
252
215
191
173
159
148
139
131
1¼
1.380
937
644
517
442
392
355
327
304
285
269
1½
1.610
1403
964
775
663
588
532
490
456
427
404
2
2.067
2703
1858
1492
1277 1131
1025
943
877
823
778
2½
2.469
4308
2961
2377
2035 1803
1634
1503
1399
1312
1239
3
3.068
7615
5234
4203
3567 3188
2889
2658
2472
2320
2191
*1 CFH of LP gas is approximately equal to 2.5 MBH; contact your gas supplier for the actual heating value of your gas.
Summary of Contents for AMP 1000
Page 85: ...85 Notes...