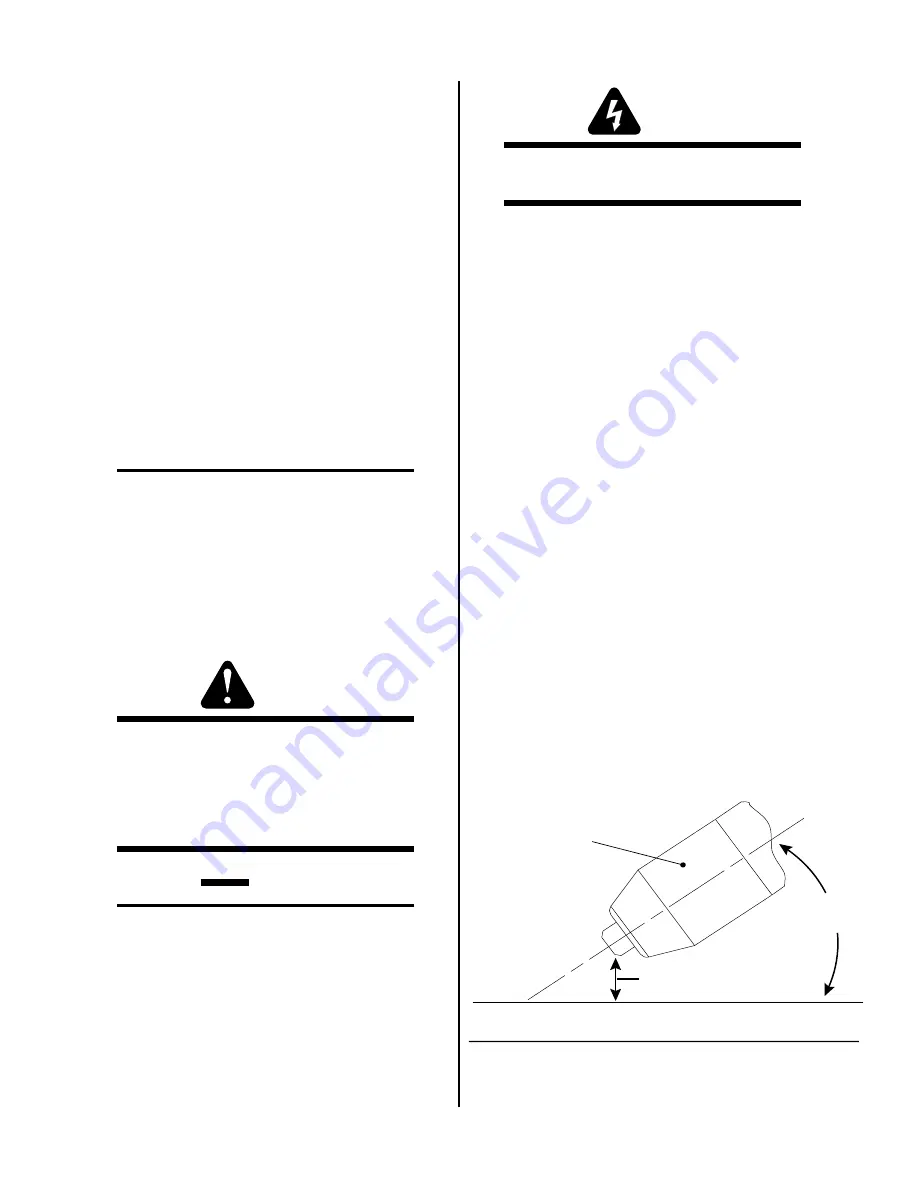
Manual 0-2583
23
OPERATION
tance for optimum speed and cut quality. Clean spat-
ter and scale from the shield cup and the tip as soon
as possible. Spraying or dipping the shield cup in
anti-spatter compound will minimize the amount of
scale which adheres to it.
4.09 Recommended Cutting Speeds
Cutting speed depends on material, thickness, and the
operator’s ability to accurately follow the desired cut line.
The following factors may have an impact on system per-
formance:
• Torch parts wear
• Air quality
• Line voltage fluctuations
• Torch standoff height
• Proper work cable connection
NOTE
This information represents realistic expectations
using recommended practices and well-maintained
systems. Actual speeds may vary up to 50% from
those shown.
Refer to Appendix I, Cutting Speed Charts, for complete
chart data.
4.10 Gouging
WARNING
Be sure the operator is equipped with proper gloves,
clothing, eye and ear protection and that all safety
precautions at the front of this manual have been
followed. Make sure no part of the operator’s body
comes in contact with the workpiece when the torch
is activated.
CAUTIONS
Sparks from plasma gouging can cause damage to
coated, painted or other surfaces such as glass, plas-
tic, and metal.
Check torch parts. The torch parts must correspond
with the type of operation. Refer to Section 4.04,
Torch Parts Selection.
WARNING
Disconnect primary power to the system before
disassembling the torch, leads, or power supply.
A. Gouging Parameters
Gouging performance depends on parameters such
as torch travel speed, current level, lead angle (the
angle between the torch and workpiece), and the dis-
tance between the torch tip and workpiece (standoff).
B. Torch Travel Speed
Optimum torch travel speed for gouging is 20 inches
per minute (0.5 meters per minute) at 3/16 inch (4.7
mm) standoff. Travel speed is dependent on current
setting, lead angle, and mode of operation (hand or
machine torch).
C. Current Setting
Current settings depend on torch travel speed, mode
of operation (hand or machine torch), and the amount
of material to be removed.
D. Lead Angle
The angle between the torch and workpiece depends
on the output current setting and torch travel speed.
At 70 amps, the recommended lead angle is 35° (refer
to Figure 4-9). At a lead angle greater than 45° the
molten metal will not be blown out of the gouge and
may be blown back onto the torch. If the lead angle is
too small (less than 35°), less material may be removed,
requiring more passes. In some applications, such as
removing welds or working with light metal, this may
be desirable.
35˚
Workpiece
Torch Head
Standoff Height
1/8 - 1/4"
A-00941
Figure 4-9 Gouging Angle and Standoff Distance
Summary of Contents for PCH-100XL
Page 2: ......
Page 6: ......
Page 18: ...INTRODUCTION DESCRIPTION 12 Manual 0 2583...
Page 22: ...INSTALLATION PROCEDURES 16 Manual 0 2583...
Page 38: ...SERVICE 32 Manual 0 2583...