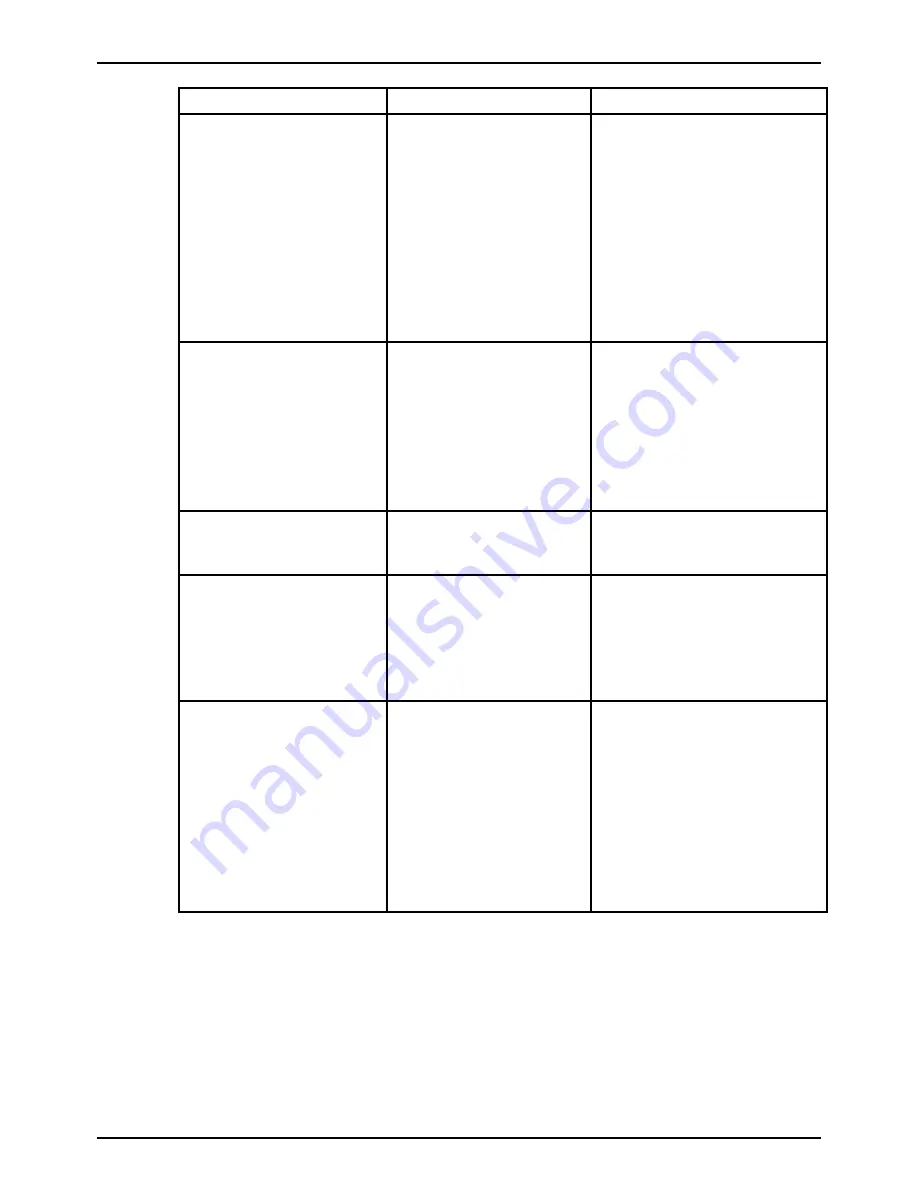
Viking 210GM, 250GM
30
12.2 Welding Problems
FAULT CAUSE REMEDY
1 Undercut.
A Welding arc voltage too
high.
A Reduce voltage by reducing
the voltage selection switches
position or increase the wire
feed speed.
B Incorrect torch angle
B Adjust angle
C Excessive heat input
C Increase the torch travel
speed and/or reduce welding
current by reducing the
voltage selection switches
position or reducing the wire
feed speed.
2 Lack of penetration.
A Welding current too low A Increase welding current by
increasing wire feed speed
and increasing voltage
selection switch position.
B Joint preparation too
narrow or gap too tight
B Increase joint angle or gap
C Shielding gas incorrect
C Change to a gas which gives
higher penetration
3 Lack of fusion.
Voltage too low
Increase voltage by
increasing voltage selection
switches position.
4 Excessive spatter.
A Voltage too high
A Lower voltage by reducing
the voltage selection switches
or increase wirespeed control.
B Voltage too low
B Raise voltage by increasing
the voltage selection switches
or reduce wirespeed control.
5 Irregular weld shape.
A Incorrect voltage and
current settings.
Convex, voltage too low.
Concave, voltage too
high.
A Adjust voltage and current by
adjusting the voltage
selection switches and the
wirespeed control.
B Wire is wandering
B Replace contact tip
C Incorrect shielding gas
C Check shielding gas.
D Insufficient or excessive
heat input
D Adjust the wirespeed control
or the voltage selection
switches.
Summary of Contents for Viking 210GM
Page 21: ...Viking 210GM 250GM 16 6 WELDING GUIDE VIKING 210GM...
Page 22: ...Viking 210GM 250GM 17 7 WELDING GUIDE VIKING 250GM...
Page 40: ...Viking 210GM 250GM 35 14 VIKING 210GM CIRCUIT DIAGRAM...
Page 41: ...Viking 210GM 250GM 36 15 VIKING 250GM CIRCUIT DIAGRAM...
Page 42: ...Viking 210GM 250GM 37 16 PRINTED CIRCUIT BOARD CIRCUIT DIAGRAM CAT NO 10 6100...