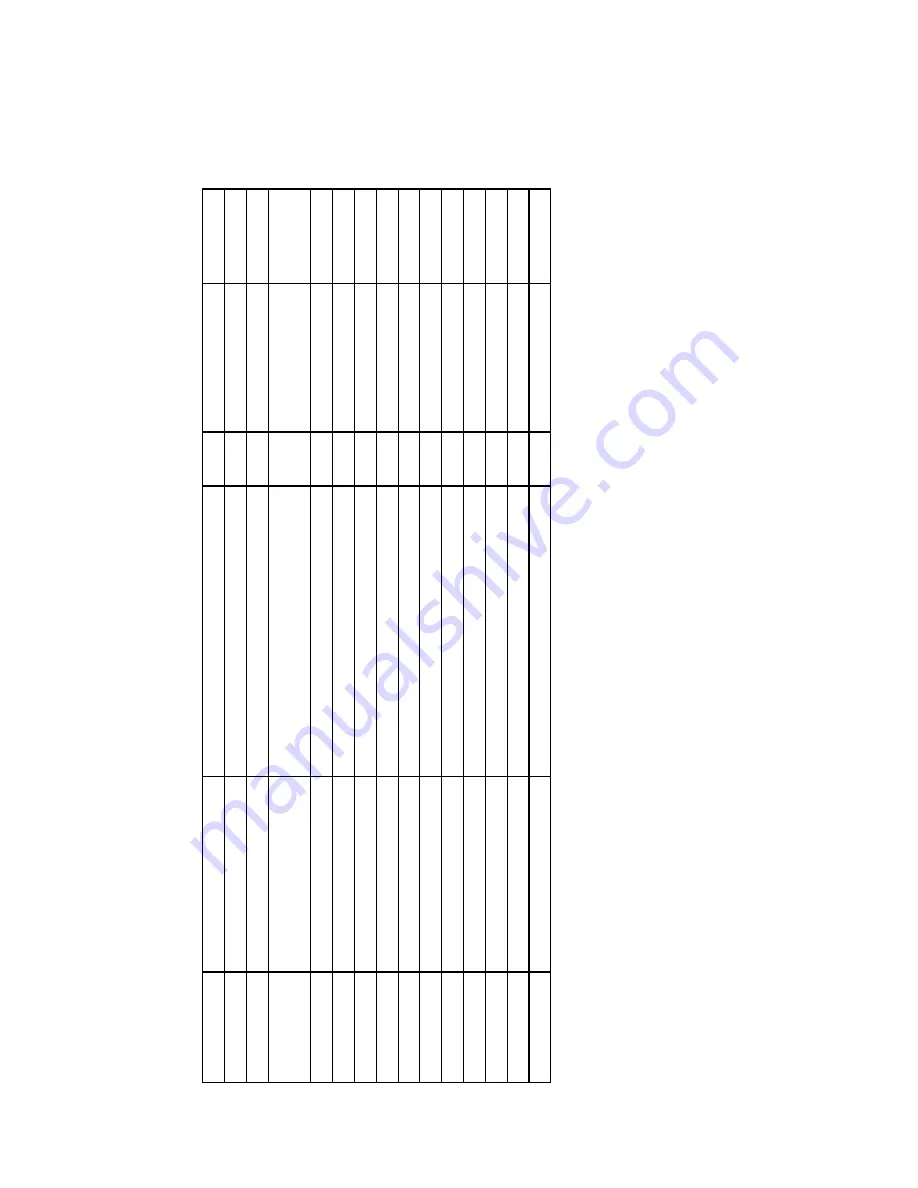
50
12.0 P
A
RTS
LIST
D
W
G
. N
o
.
D
escr
ip
ti
on
T
y
pe & R
a
ti
ng
QT
Y
.
C
ode N
o
.
O
rder
N
o
.
C
1
C
apaci
tor
EC
QE12
104M
Z D
C
1
250
V
0.1
u
F
1
424
221
3
71
00
10-
22
70
C
C
1
C
oupl
in
g
C
o
il
F2A75
420
0 2
5
0
A
C
C
1
F
2A75
420
0
10-
67
59
C
O
N
1
R
e
mot
e
S
o
cket
206
433-
1
8P
(wit
h
W
iri
n
g
A
sse
mb
ly
)
1
U
0A70
610
0
10-
66
27
D
1
D
iode
D
F
A75BA
160
1
454
170
1
60
10-
67
35
D
2
D
iode
D
BA20
0
U
A
40
1
458
2A0
0
40
10-
66
87
D
3
D
iode
D
BA20
0
U
A
40
1
458
2A0
0
40
10-
66
87
D
4
D
iode
D
BA20
0
U
A
40
1
458
2A0
0
40
10-
66
87
D
5
D
iode
D
BA20
0
U
A
40
1
458
2A0
0
40
10-
66
87
FAN
1
Fan
109E
57
24H
50
7 D
C
2
4
V
16.8
W
1
U
0A73
350
0
10-
68
39
FC
H
1
Induc
tor
F
2A67
690
0 2
5
0
A
T
IG FC
H
1
F2A67
6
90
0
10-
67
60
H
C
T
1
C
ur
rent Se
nsor
H
C
-T
N
200V
4B1
5
M
200
A
4V
1
112
510
0
30
00
10-
50
03
HF.UNIT
1
HF. Un
it
HF.UNIT
(
W
K-4
8
4
0
U02
)
1
U
0
A
6
3
2
2
00
1
0
-6
6
3
2
H
F
. Gap
U
0A60
110
0
1
U
0
A60
1
10
0
10-
66
33
L10
5
Induc
tor
161
5M
R
E
R
IN
G
C
O
R
E
1
632
000
0
65
00
10-
65
38
Summary of Contents for 250TS DC CC
Page 2: ......
Page 4: ...4 PAGE LEFT INTENTIONALLY BLANK ...
Page 22: ...22 PAGE LEFT INTENTIONALLY BLANK ...
Page 54: ...54 APPENDIX A INTERCONNECT DIAGRAM ...
Page 55: ...55 ...