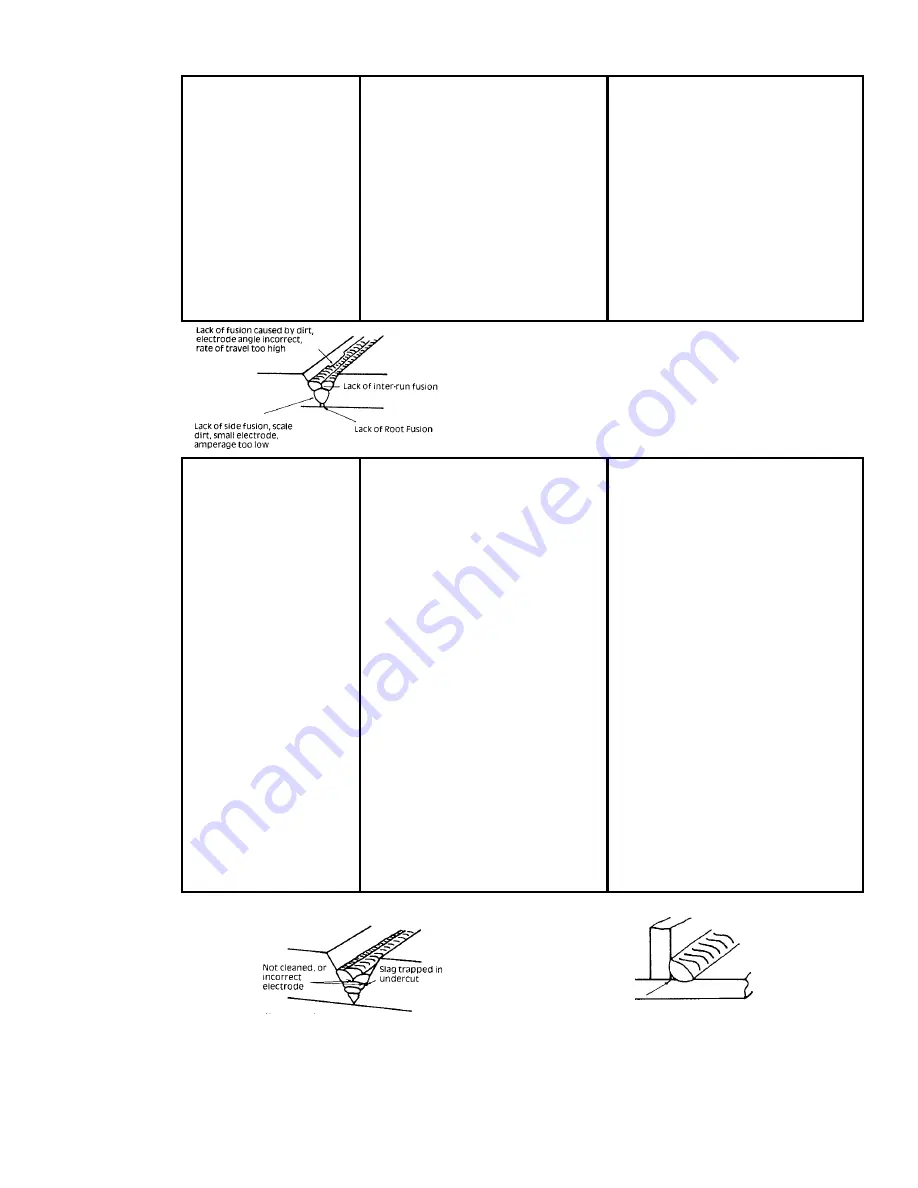
43
4 Portions of the
weld run do not
fuse to the surface
of the metal or
edge of the joint.
A
B
Small electrodes used on
heavy cold plate.
Welding current is too low.
A
B
Use larger electrodes and pre-
heat the plate.
Increase welding current
C Wrong electrode angle.
C Adjust angle so the welding
arc is directed more into the
base metal
D Travel speed of electrode is
too high.
D Reduce travel speed of
electrode
E Scale or dirt on joint surface.
E Clean surface before welding.
Figure 9 – Example of lack of fusion
5 Non-metallic parti-
cles are trapped in
the weld metal
(slag inclusion).
A Non-metallic particles may
be trapped in undercut from
previous run.
A If bad undercut is present,
clean slag out and cover with a
run from a smaller diameter
electrode.
B Joint preparation too
restricted.
B Allow for adequate
penetration and room for
cleaning out the slag.
C Irregular deposits allow slag
to be trapped.
C If very bad, chip or grind out
irregularities.
D Lack of penetration with slag
trapped beneath weld bead.
D Use smaller electrode with
sufficient current to give
adequate penetration. Use
suitable tools to remove all
slag from corners.
E Rust or mill scale is
preventing full fusion.
E Clean joint before welding.
F Wrong electrode for position
in which welding is done.
F Use electrodes designed for
position in which welding is
done, otherwise proper control
of slag is difficult.
Figure 10 –
Examples of slag inclusion
Summary of Contents for 250TS DC CC
Page 2: ......
Page 4: ...4 PAGE LEFT INTENTIONALLY BLANK ...
Page 22: ...22 PAGE LEFT INTENTIONALLY BLANK ...
Page 54: ...54 APPENDIX A INTERCONNECT DIAGRAM ...
Page 55: ...55 ...