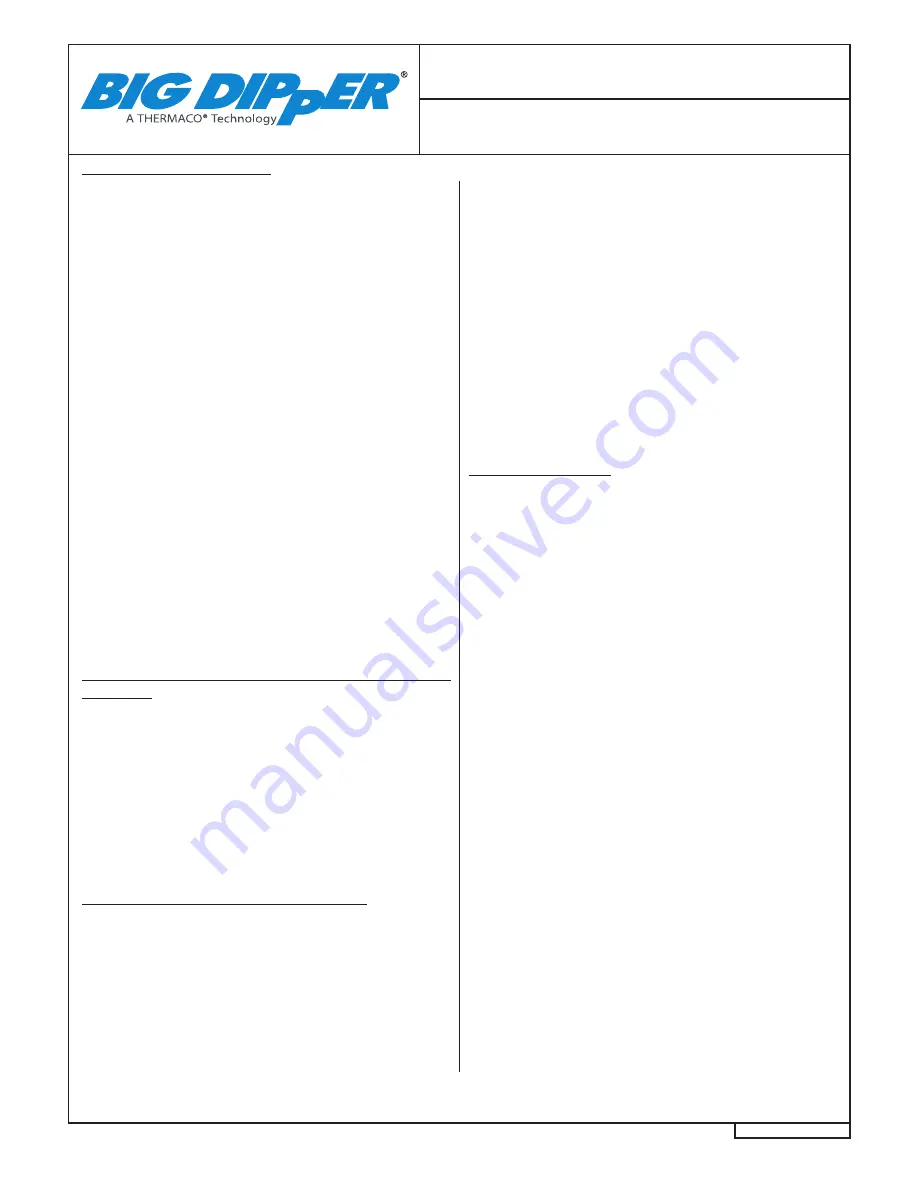
©2014 Thermaco, Inc. All rights reserved • Patented/Patents Pending • Specifications subject to change without notice
Thermaco, Inc. • 646 Greensboro St. • Asheboro, N. C. 27204-2548 • Phone (336) 629-4651
MNL-ISCU40000 7
40000 Series
Big Dipper
®
IS System
Troubleshooting
Big Dipper unit overflows
(1) Check to see that the outlet pipe is not reduced to a
smaller size, the outlet piping is vented, has as few 90
degree outlet turns as possible, and that no “P” trap is
installed on the outlet. Re-plumb the piping, if neces-
sary. Check outlet piping for clogs. Have a plumber
clean the line, if necessary.
(2) Make sure that the solids strainer is in place and
emptied daily.
(3) Check the bottom of the grease chamber for exces-
sive solids and silt buildup which may be blocking the
outlet baffle. Disconnect the power and use a long
handled spatula or similar instrument to stir the bottom
while water flows through the unit. If necessary, drain
and clean the sediment from the unit. To prevent recur-
rence, schedule this cleaning to be done on a regular
basis (properly used, a wet vac may be appropriate for
cleaning sediment from the bottom of the unit).
(4) Make sure the flow rate to the unit does not exceed
the maximum flow rate, which is shown on the nameplate.
If necessary, have a plumber install an approved flow
control to restrict the inlet flow to the specified level or
install a properly sized Big Dipper for the application.
Excessive water observed in the grease collection
container
(1) Check Digital Control for excessive “on” time. Unit
will pick up incidental water after all grease is removed.
If necessary, reduce the digital control setting (i.e.
Moderate [II] to Light [I]) until no water is observed in
the grease collection container.
(2) Make sure that the water flow to the unit does not
exceed the rated flow and there are no drain line clogs
downstream from the unit.
No grease is collected in the container
(1) Check to be sure the power is on and the correct
setting is chosen. One of the setting buttons should be
illuminated. If none of the setting buttons are illuminated,
the unit is not powered.
(2) Lift the sump cover and clean away any buildup
that may be present on the wiper blades or collection
trough. Make sure the wiper blade(s) are properly in
place on the skimmer wheels. Replace wiper blades
when worn or warped.
(3) Press the Start Button on the bottom of the user inter-
face to ensure that the skimming wheel turns
.
CAUTION: Keep your hands away from moving parts
to avoid possible injury. If the skimmer motor does not
come on, the motor assembly may need to be replaced.
(4) Check for congealed grease in the unit. If the Big
Dipper’s heating element is not warming the unit, the
heating element may need to be replaced.
(5) Some sites do not generate enough grease to be
captured by the skimming process. Set Control for
minimum operation - Setting [I] for Light Skimming
Operation.
Objectionable odor
(1) Make sure grease/oil is being skimmed properly
from the unit.
(2) Check Digital Control for excessive “on” time. Unit
will pick up incidental water after all grease is removed.
If necessary, reduce the digital control setting (i.e.
Moderate [II] to Light [I]) until no water is observed in
the grease collection container.
(3) If excessive sediment has collected on the bottom
of the unit, clean the unit as described in item 3 in “Big
Dipper unit overflows.”
(4) Clean the solids strainer and grease collection
container more frequently.
(5) Grease interceptors, grease traps, automatic re-
covery units, grease removal devices and other similar
plumbing devices receiving kitchen flows from sinks,
floor drains, woks and other food bearing sources may
generate odors. There are many factors influencing
odor evolution and dissemination. These include room
ventilation, kitchen menu, ambient temperatures, ware
washing practices, grease/oil input, daily input fluid vol-
ume, sanitizers, installation plumbing design and product
maintenance/upkeep. Odors are usually prevented by
good area ventilation, frequent fluid inputs, good product
maintenance practices and proper product installa-
tion. Additional steps, including aeration, chlorination,
improved area ventilation and additional maintenance
control, may be needed at some sites.