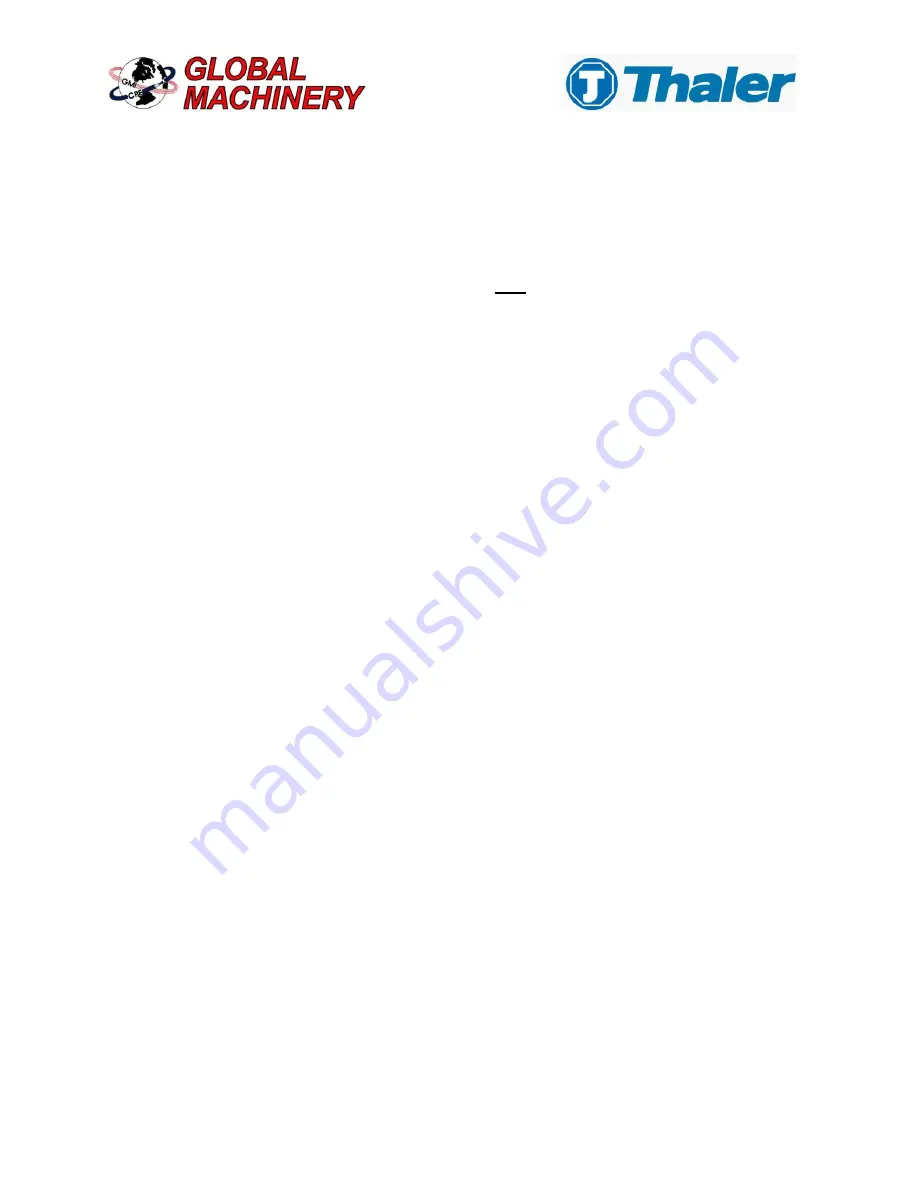
Page 3
1.7
Product Description:
This cable capstan winch represents the latest modern technical standard in the area of
hydraulically operated cable pulling winches. It is specifically designed for pulling in and out
communication and power cables of all types.
The winch is designed for pulling horizontally. It is
NOT
to be used as a means for lifting loads.
The single axle chassis consists of a rubber suspension axle with electric brakes. The hitch is
height adjustable and equipped with a forged 4-bolt mount hitch. A crank jack is fitted to the trailer
tongue. The tire size is 215/75R 17.5. The lighting system is 12 Volt.
Rear adjustable stabilizers control the stability of this winch during the pulling operation. For
transportation the stabilizers may be raised up and be secured with the appropriate pins.
The capstan unit is hydraulically driven. The power pack consists of a 36HP (27.1 kW) water-cooled
diesel engine (corresponding to the EPA norms) and a pressure and flow controlled hydraulic pump.
The steel wire rope of the winch runs directly from the capstan system to the rope drum. The
machine is equipped with an automatic level-wind system with cross groove spindles so that even
layering of the rope onto the rope drum is guaranteed.
Drive and brake operation of the drum is powered hydraulically.
The boom is hydraulically raised and lowered, manually p/-45° laterally and is secured by
a manually adjusted boom support.
The measurement of the pulling force is controlled and monitored by an electronic measuring
system (KPR 2000) with a record printer mounted at the control panel. The measuring system
has the following functions:
- Indication of pulling force, length and pulling speed
- Adjustable maximum pulling force limit with automatic stopping function of the winch drive
system when the adjusted pulling force is exceeded
- The ability to print out a complete pull report while in the field
The separate card writer is connected to the KPR 2000 system by a serial cable and has a 32 MB
storage card with card adaptor for storing cable pull data.
By pushing a single button at the KPR 2000, each job can be stored on the card as MS-
DOS/Windows compatible data. A name for each pulling job is automatically generated. The data
can be evaluated on a PC or Laptop and shown in tabular form. If the data is required in graphic
form, it can be opened in Excel for analysis.
All operator controls are centrally mounted at the operation panel. The following controls exist:
- Remote control joystick with deadman switch for controlling the pulling direction and speed
-Throttle lever for engine speed
- Key-operated switch for engine start
- Control indicators for diesel engine
- Fuel gauge
- Working hour meter
- Electronic measuring system (KPR 2000)
- Card-writer with adaptor
- Raise/Lower lever for hydraulic boom
- On/Off switch for rotating beacon light