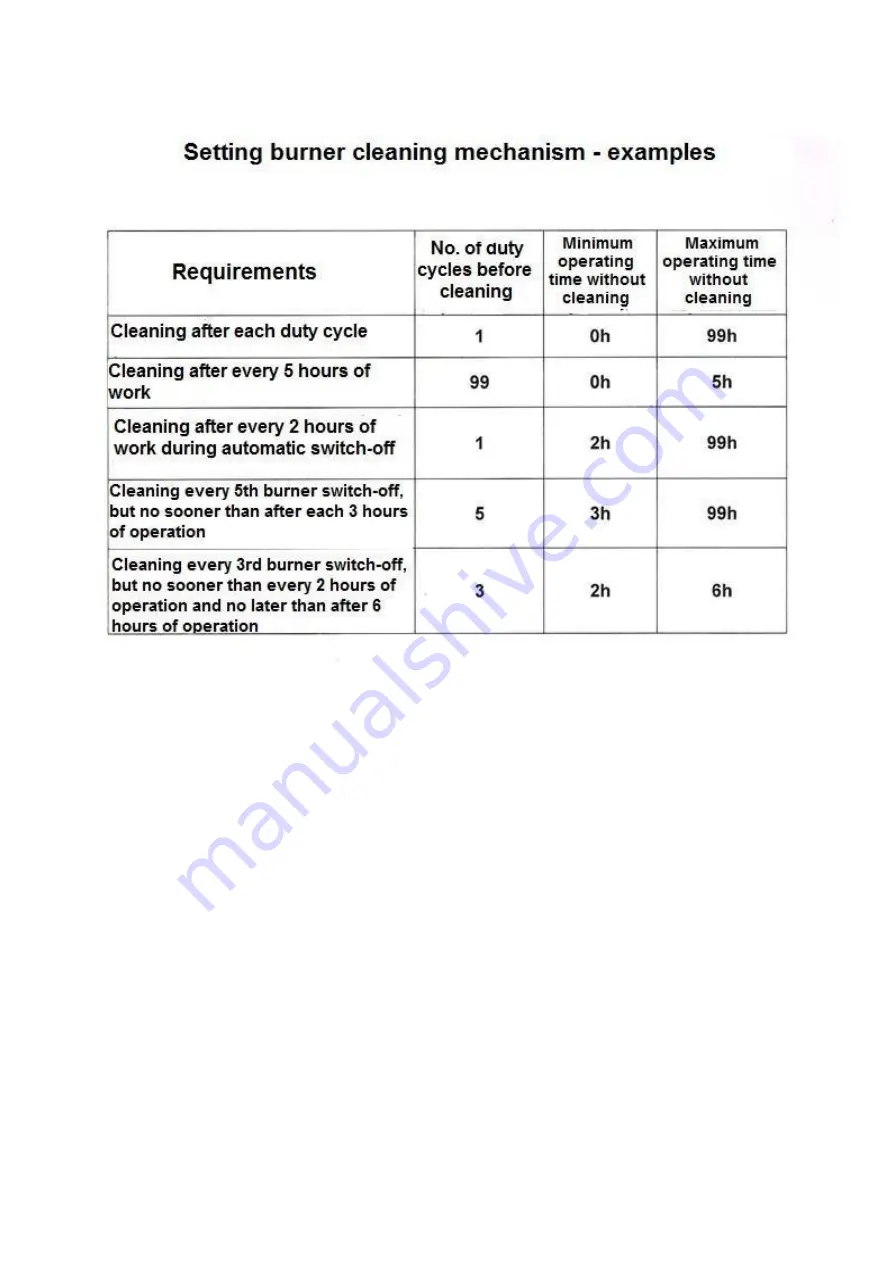
23
4.1 Cleaning - setting burner cleaning mechanism
Table below includes examples of cleaning algorithms:
It is recommended to clean the burner after each work cycle because this guarantees
unhindered ignition in each subsequent work cycle.
It is worth emphasizing here that failure-free and automatic operation of the
burner is influenced both by the automatic cleaning mechanism as well as by the
conditions present in the boiler room. It is suggested to avoid excessive moisture and
dusting in the boiler room as well as to keep this room in neat condition because
controlling devices, particularly the central processing unit, photo sensor etc., are
equipped with sensitive electronic parts.
4.2 Replacing the ignition device
The ignition device is one of those elements which wear out mostly and which are
subject to the greatest loads. It is made of ceramic elements and its nominal life-span
Summary of Contents for Ecomat 15
Page 1: ...TERMOTECHNIKA OPERATION AND MAINTENANCE MANUAL FOR PELLET BURNERS ECOMAT ...
Page 5: ......
Page 12: ...3 2 Burner and feeder dimensions and conditions for installation in the boiler ...
Page 13: ......
Page 14: ......
Page 15: ......
Page 16: ......
Page 17: ...Assembly hole dimensions ECOMAT100 Pellet burner ...
Page 30: ...30 Burner serial number Burner production date Date of purchase ...
Page 33: ...33 ...